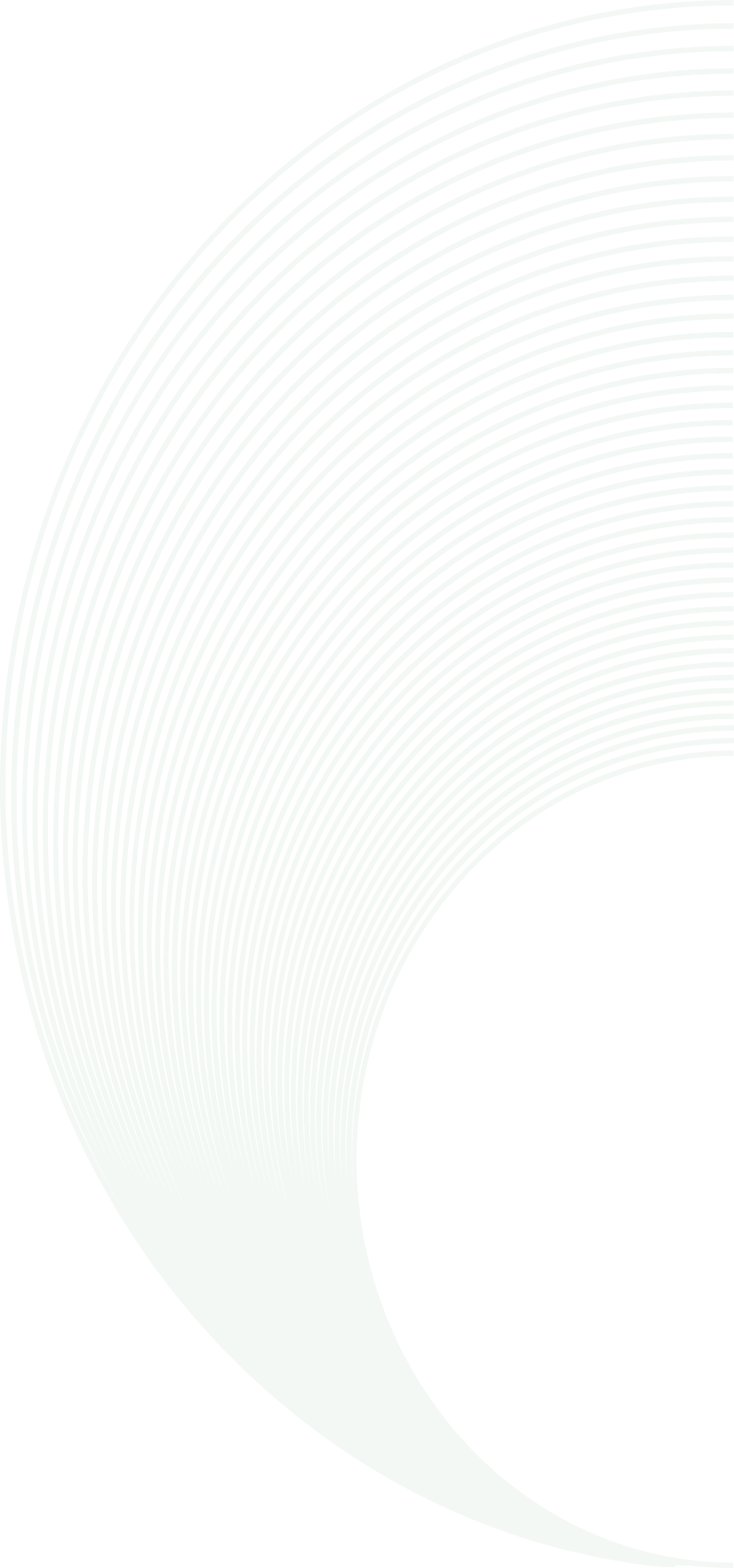
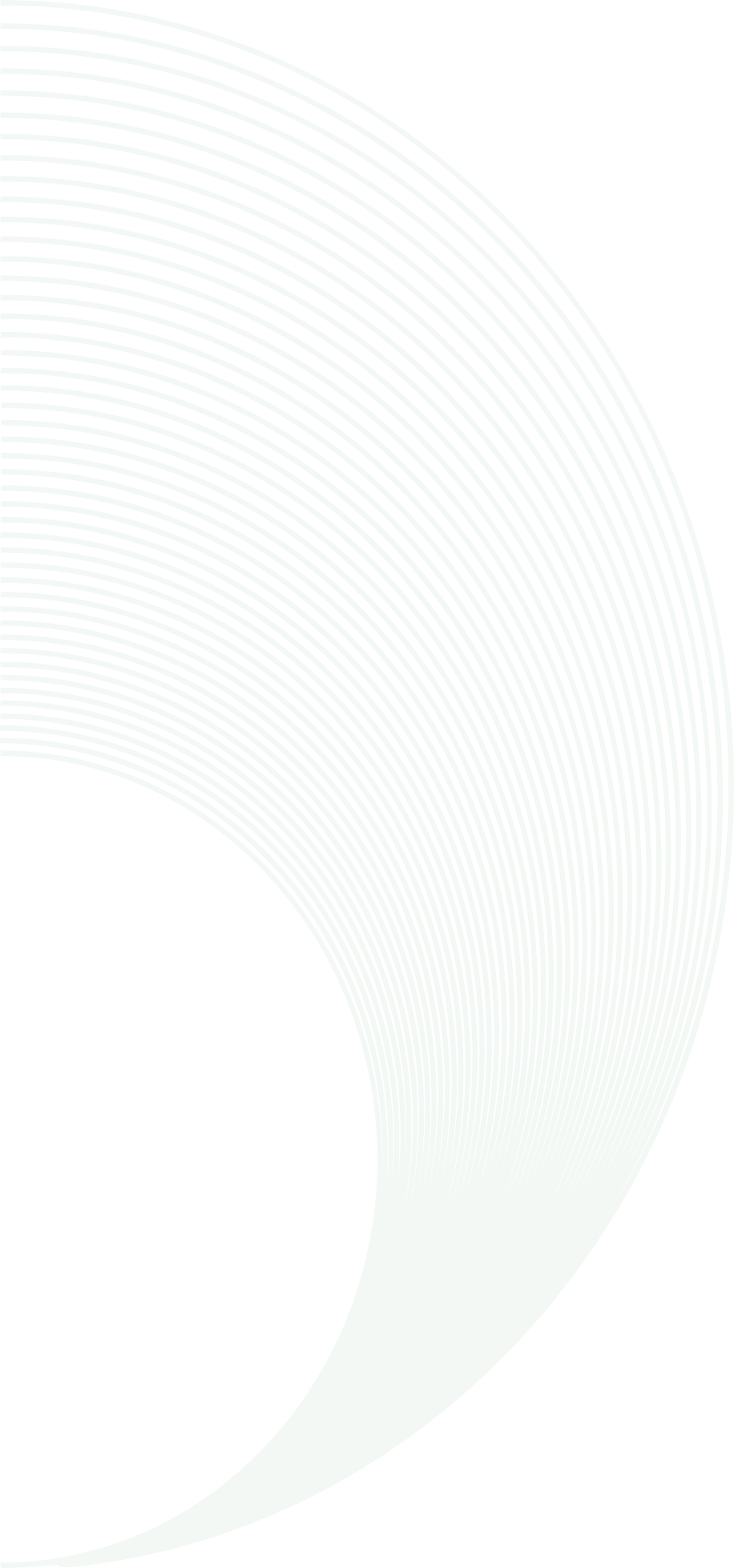
Iron and Steel Production: Processes and Technologies
Iron and steel are foundational materials that drive modern industry, construction, and manufacturing. The production of these metals involves transforming raw iron ore into usable iron and then refining it into various types of steel with tailored properties. This complex process requires a series of carefully controlled steps and advanced machinery to ensure quality and efficiency.
Iron production typically begins with the extraction and processing of iron ore, followed by smelting in blast furnaces. Steel production further refines the iron by adjusting its composition and removing impurities. The resulting steel is then shaped and treated to meet specific industrial needs.
Key Stages in Iron Production
The initial stage in iron production involves preparing iron ore through crushing, grinding, and beneficiation to increase iron content and remove impurities. The prepared ore is then combined with coke and limestone in a blast furnace, where high-temperature chemical reactions reduce iron oxides to molten iron.
Inside the blast furnace, coke acts as both a fuel and reducing agent, while limestone helps remove impurities by forming slag. The molten iron collected at the furnace’s base, often called pig iron, contains high carbon levels and is brittle, requiring further processing to produce steel.
Steelmaking and Refining Processes
Steel is produced by refining pig iron to reduce its carbon content and add alloying elements for desired mechanical properties. This refining occurs mainly in basic oxygen furnaces (BOF) or electric arc furnaces (EAF).
In a basic oxygen furnace, oxygen is blown into molten pig iron to oxidize excess carbon and impurities, transforming it into steel. This process is rapid and efficient for large-scale production.
Electric arc furnaces, on the other hand, use electric arcs to melt scrap steel and direct reduced iron. EAFs offer flexibility and are common in recycling scrap metal, making them vital in sustainable steel production.
After refining, steel may undergo secondary metallurgy treatments to adjust temperature, composition, and remove remaining gases or inclusions. This ensures consistent quality before shaping.
Shaping and Finishing Techniques
Once refined, steel is cast into various shapes through continuous casting or ingot casting. Continuous casting is prevalent in modern plants, where molten steel solidifies into slabs, blooms, or billets that can be further processed.
These semi-finished products are then hot rolled or cold rolled to create sheets, plates, bars, or structural shapes. Additional finishing processes like heat treatment, coating, and surface treatment enhance strength, corrosion resistance, and other properties.
Steel production equipment includes rolling mills, heat treatment furnaces, and finishing lines, which collectively tailor steel products for applications ranging from automotive to construction.
Environmental and Technological Advances
Modern iron and steel production faces challenges related to energy consumption and emissions. Advances in technology aim to improve efficiency and reduce environmental impact.
Processes such as direct reduced iron (DRI) production reduce reliance on blast furnaces by using natural gas to reduce iron ore at lower temperatures. Hydrogen-based reduction methods are also under development, offering potential carbon-free ironmaking.
Recycling scrap steel through electric arc furnaces contributes significantly to sustainability by lowering energy use and conserving natural resources.
Conclusion
Iron and steel production is a complex, multi-step process combining chemistry, engineering, and metallurgy to create essential materials for industry. From raw ore processing and smelting to refining and shaping, each stage requires specialized equipment and careful control.
Ongoing technological innovations continue to improve efficiency and environmental performance, ensuring that iron and steel remain critical to modern infrastructure and manufacturing for years to come.