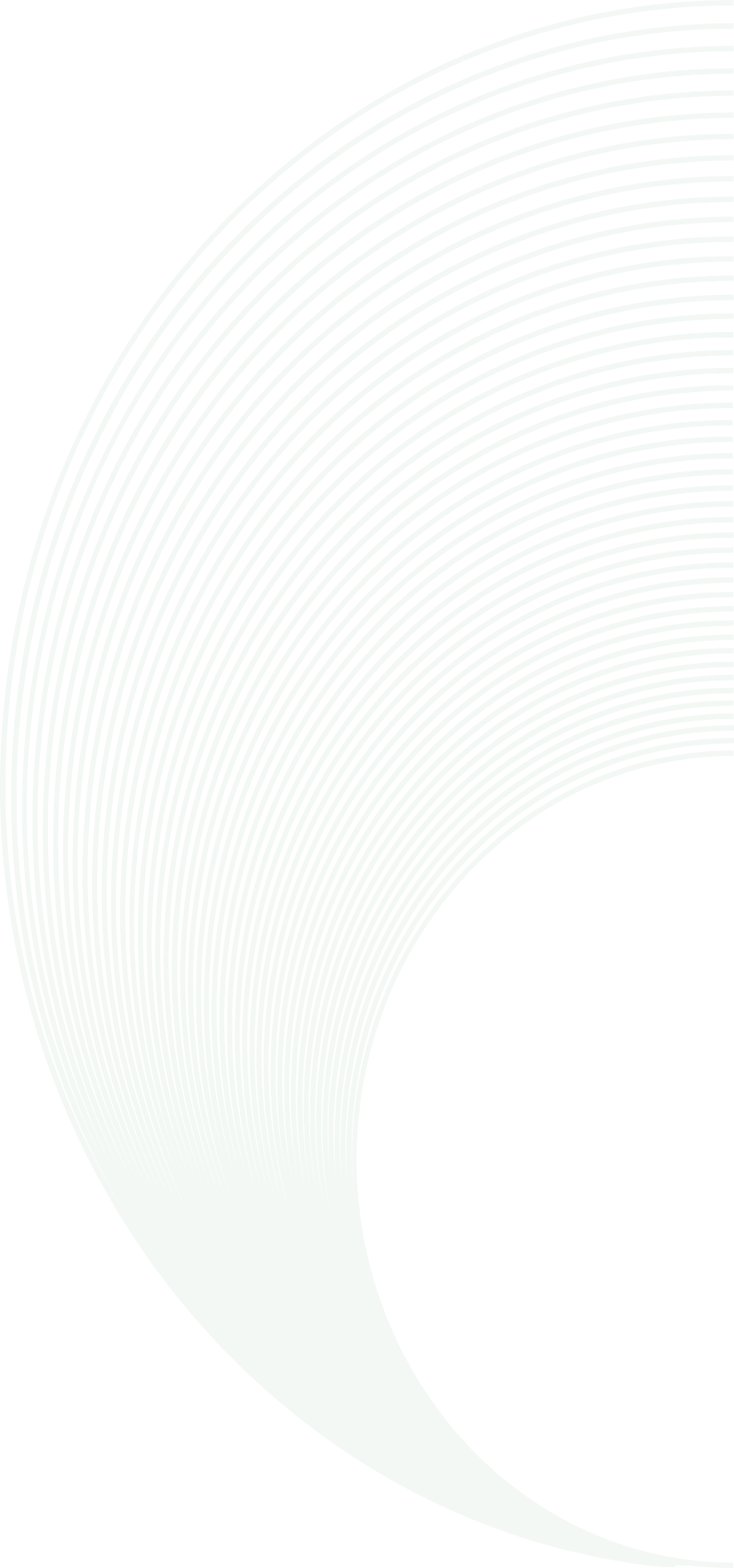
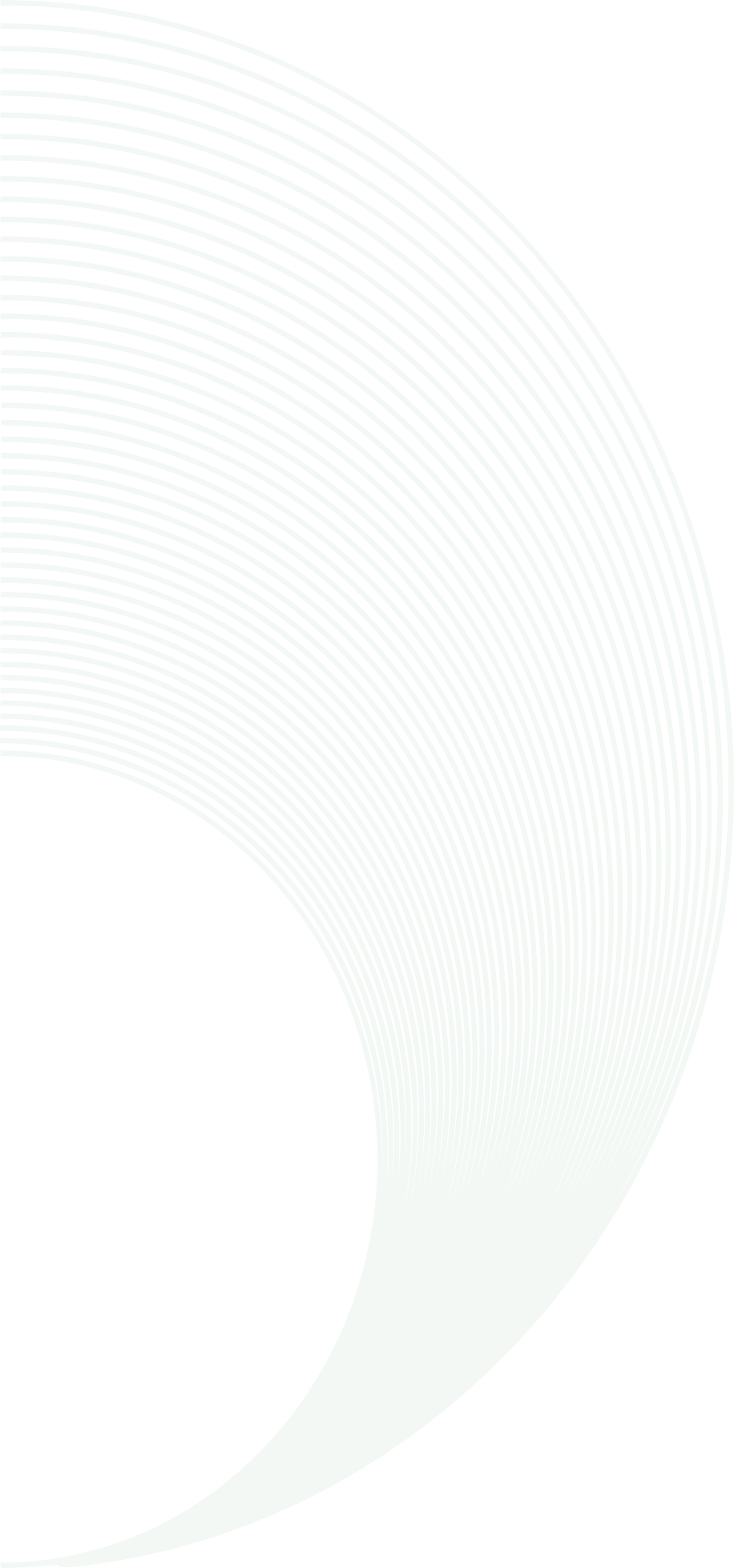
Machines Used to Extract Iron from Iron Ore
The process of extracting iron from its ore involves multiple stages, each requiring specialized machinery designed to handle specific tasks. Iron ore, found mainly as hematite and magnetite, must go through extraction, concentration, reduction, and refining before it becomes usable iron or steel. Each of these stages depends heavily on machines that carry out crushing, separation, heating, and material handling efficiently and at industrial scale.
In modern mining and metallurgy, machines not only speed up production but also improve precision, reduce energy consumption, and enhance safety. These machines range from large surface mining vehicles to complex furnaces and automated refinement units. Their integration into the iron extraction process is essential for meeting industrial demand and maintaining quality standards.
Mining Equipment for Iron Ore Extraction
The first stage in extracting iron from ore involves mining, and this requires large-scale machines to remove ore-bearing rock from the earth. Open-pit mining is the most common method, especially when iron ore is found near the surface. Surface miners and rotary drills are used to break up the ground, followed by the use of electric rope shovels or hydraulic excavators to scoop the ore.
Dump trucks and conveyor systems then transport the ore from the mining site to the processing facility. These vehicles are built to handle extremely heavy loads and are often equipped with onboard monitoring systems that optimize performance and fuel usage.
In underground mining operations, tunnel boring machines and longwall miners may be used to extract ore located deeper below the surface. These machines require advanced ventilation and safety systems due to the confined and hazardous nature of the working environment.
Crushing and Grinding Machines
Once the raw iron ore reaches the processing plant, it must be reduced in size to allow for further separation and refining. This begins with crushing equipment such as jaw crushers, gyratory crushers, and cone crushers. These machines break large chunks of ore into smaller pieces suitable for grinding.
After crushing, the ore is fed into grinding mills—usually ball mills or vertical roller mills—that grind it into a fine powder. This powdered form increases the surface area, making it easier for the next stage of magnetic or gravity separation to remove unwanted materials like silica or clay.
Automated conveyor belts and hoppers ensure the continuous flow of material through the system, and dust collection units are installed to maintain air quality in the processing area.
Separation and Concentration Machinery
With the ore now in a finely ground state, specialized machines are used to concentrate the iron content and separate it from the surrounding impurities. Magnetic separators are commonly used for this purpose, especially when processing magnetite ores. These machines use powerful electromagnets to attract iron particles and separate them from non-magnetic materials.
For ores that are less magnetic, such as hematite, gravity separators or flotation units may be used. Gravity separation machines use differences in particle density to isolate heavier iron-rich materials, while flotation cells rely on chemical reagents and air bubbles to lift iron particles to the surface.
Thickeners and filtration units are then used to remove excess water from the concentrated ore, resulting in a more manageable form such as pellets or sinter, ready for the smelting process.
Blast Furnace and Smelting Equipment
The heart of traditional iron extraction is the blast furnace—a massive steel structure lined with heat-resistant bricks. This machine is designed for the high-temperature reduction of iron ore into molten iron. Large industrial blast furnaces are fed from the top with alternating layers of iron ore, coke, and limestone.
Hot air is blasted into the furnace through tuyeres located near the bottom. This combustion supports the chemical reduction of iron oxides into metallic iron. The furnace also requires automated charging systems, temperature control sensors, and tapping machines to drain molten iron and slag at regular intervals.
Modern blast furnaces are equipped with computer-controlled systems that regulate air flow, monitor internal temperatures, and optimize chemical reactions. These improvements have made the iron extraction process more efficient and consistent across production cycles.
Refining and Steelmaking Machines
Once the molten iron is removed from the blast furnace, it is typically transferred to a basic oxygen furnace or an electric arc furnace for further refining. These furnaces reduce carbon and remove impurities to create various grades of steel.
In a basic oxygen furnace, high-purity oxygen is blown through the molten iron to oxidize carbon and other unwanted elements. This process is facilitated by automated lances and flow control systems that precisely regulate oxygen input. In electric arc furnaces, electric currents are used to melt recycled steel or direct reduced iron, making them a cleaner and more flexible option in modern steel plants.
Ladle metallurgy stations and continuous casting machines follow the refining stage. These machines allow for the fine adjustment of chemical composition and the controlled solidification of steel into billets, blooms, or slabs. Casting machines use molds and rollers to shape the hot metal and prepare it for rolling mills or further fabrication.
Automation and Control Systems
Throughout the iron extraction process, automation plays a vital role in improving efficiency, reducing labor intensity, and maintaining safety. Control rooms oversee every step, from mining and ore preparation to smelting and casting. Sensors and data systems provide real-time feedback on machine performance, product quality, and environmental conditions.
Programmable logic controllers (PLCs), human-machine interfaces (HMIs), and SCADA systems coordinate the complex actions of multiple machines, ensuring that materials flow seamlessly through each stage of production. These systems also support predictive maintenance by identifying wear and tear before it leads to breakdowns.
Conclusion
Extracting iron from iron ore is a highly industrialized process that relies on a wide range of machines at every stage. From heavy-duty mining equipment and crushing machinery to advanced smelting furnaces and refining systems, each machine plays a critical role in transforming raw ore into usable metal.
Advancements in automation and material science continue to reshape the iron extraction process, making it more efficient, sustainable, and technologically sophisticated. As demand for iron and steel grows globally, the machines involved in their production remain at the center of modern industry.