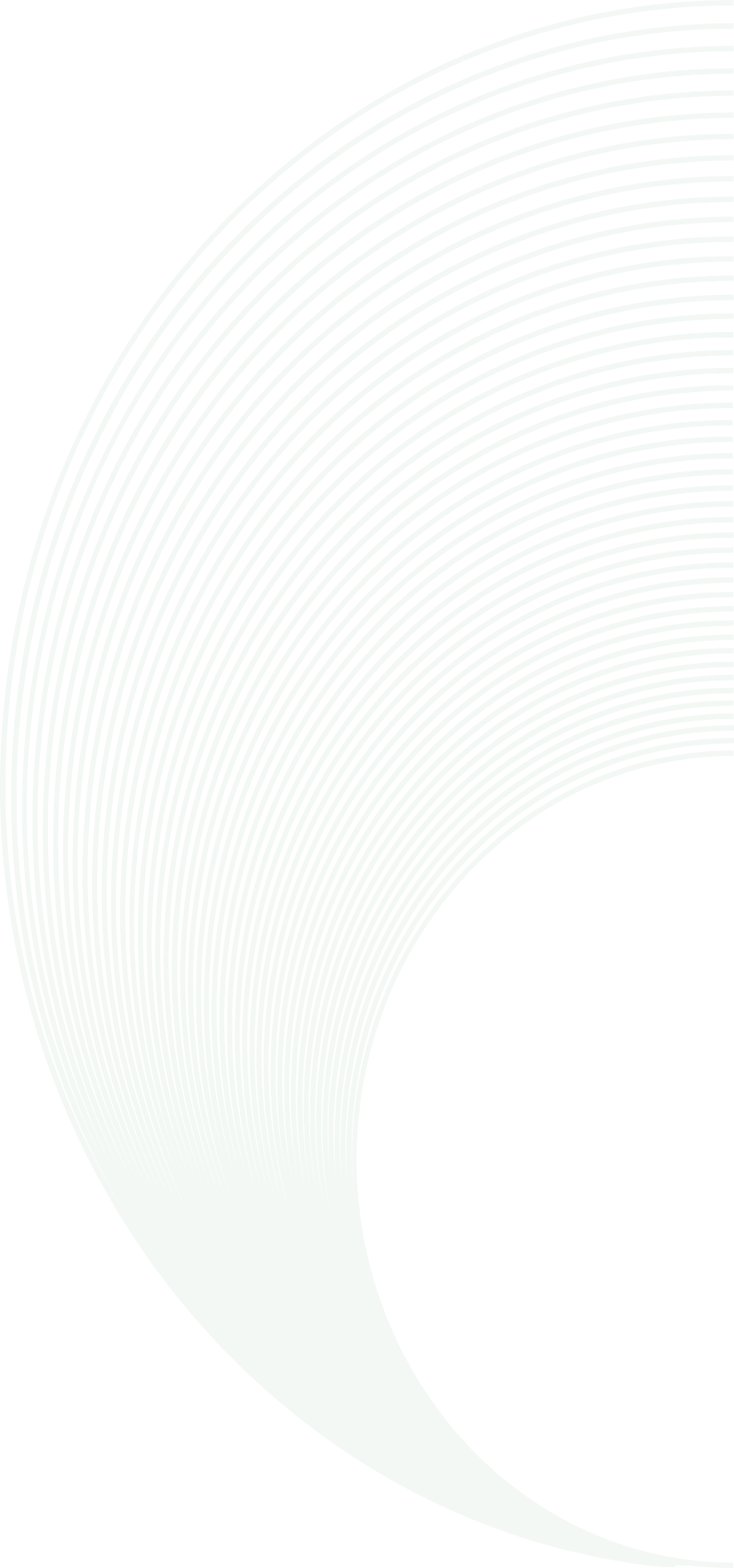
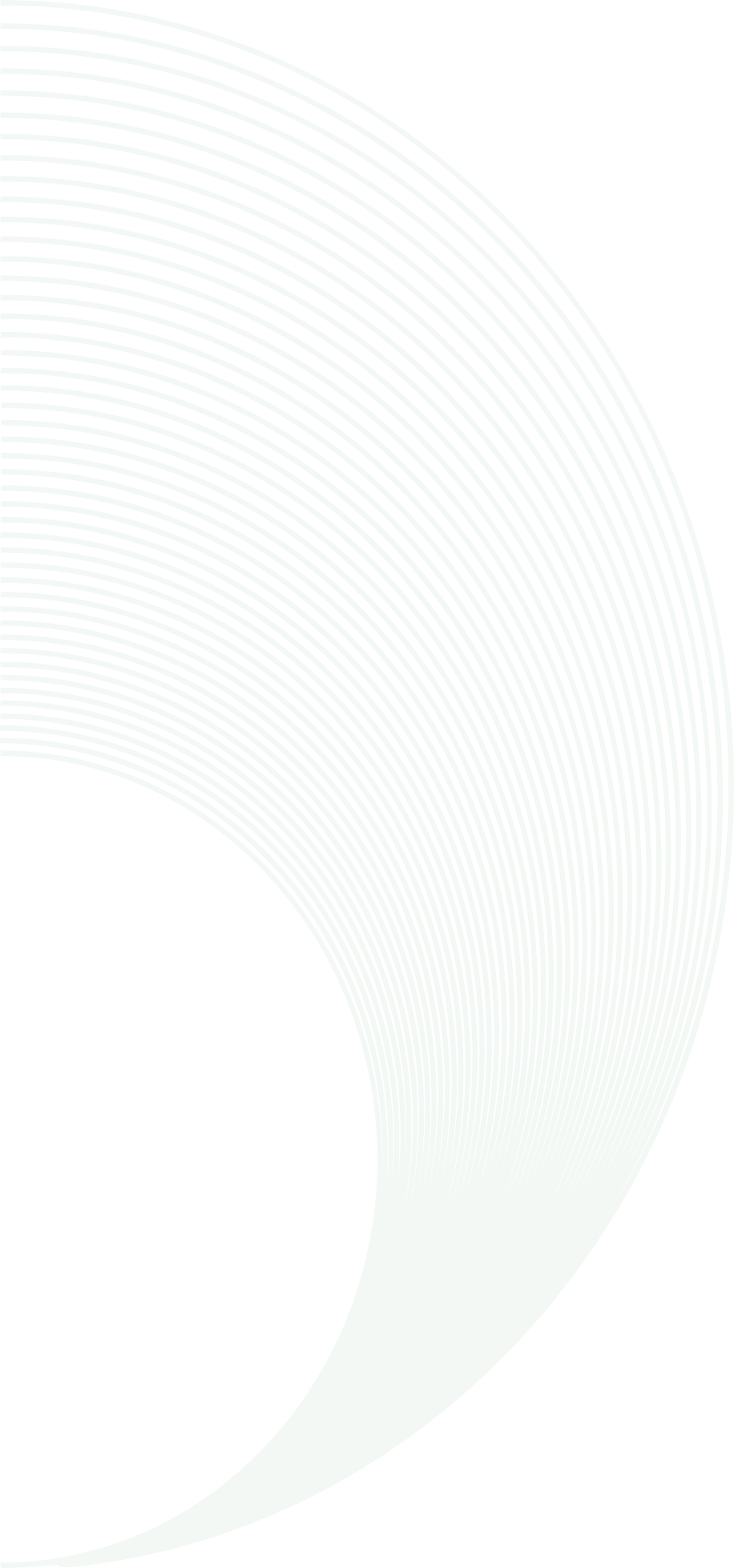
Soybeans Processing Machines for Biodiesel Production
Soybeans are one of the leading sources of vegetable oil for biodiesel production, offering a renewable and environmentally friendly alternative to fossil fuels. The process of converting soybeans into biodiesel involves several stages, each requiring specialized machines that handle tasks such as cleaning, oil extraction, purification, and chemical conversion.
The efficiency and quality of biodiesel depend heavily on the machinery used in these processing steps. Proper equipment ensures maximum oil yield, effective removal of impurities, and successful transformation of soybean oil into biodiesel through transesterification. Understanding these machines provides insight into how soybeans are transformed from raw agricultural produce into a sustainable fuel source.
Cleaning and Preparation Machines
Before oil extraction, soybeans must be cleaned to remove impurities such as dust, dirt, stones, and plant residues. Cleaning machines typically include vibrating sieves, magnetic separators, and air classifiers that sort and clean the raw soybeans. These machines prepare the beans for efficient processing, preventing damage to downstream equipment.
Following cleaning, the soybeans often undergo cracking or dehulling. Crackers break the soybeans into smaller pieces to increase the surface area for oil extraction, while dehullers remove the outer shells, improving oil yield and quality. These preparation machines play a critical role in optimizing the extraction process.
Oil Extraction Machines
The core stage in soybean processing is oil extraction, which can be done through mechanical pressing or solvent extraction. Mechanical screw presses or expellers are common machines that physically squeeze oil from the soybean flakes. These machines operate under high pressure and temperature, yielding crude soybean oil and leftover soybean meal.
For higher oil recovery, solvent extraction machines use solvents such as hexane to dissolve the oil from soybean flakes. After extraction, the solvent-oil mixture is processed to separate and recover the solvent, leaving behind crude oil. These extraction units include extraction vessels, desolventizers, and solvent recovery systems, which require precise control to ensure safety and efficiency.
Oil Refining Machines
Crude soybean oil contains impurities such as free fatty acids, phospholipids, and waxes that must be removed before biodiesel production. Refining machines include degumming units that remove phospholipids by mixing oil with water or acid solutions. Neutralization tanks then remove free fatty acids through chemical reactions with alkali solutions.
Further refining steps involve bleaching and deodorizing. Bleaching filters remove pigments and residual impurities, while deodorizing columns strip off volatile compounds that affect the oil’s smell and taste. These refining machines work together to produce high-quality soybean oil suitable for biodiesel conversion.
Transesterification Equipment
The final and most critical step in biodiesel production is the chemical conversion of refined soybean oil into biodiesel via transesterification. This reaction requires mixing the oil with an alcohol (usually methanol) and a catalyst such as sodium hydroxide or potassium hydroxide.
Transesterification reactors are specialized machines designed to mix, heat, and maintain the reactants under controlled conditions for a specific time. These reactors can be batch-type or continuous-flow systems depending on production scale. Efficient mixing and temperature control are essential for maximizing biodiesel yield and quality.
After the reaction, separation tanks or centrifuges are used to separate biodiesel from glycerol, a byproduct of the process. Washing units then clean the biodiesel to remove residual catalysts and impurities, producing fuel that meets industry standards.
Supporting Equipment
In addition to primary processing machines, several supporting units are essential in a soybean biodiesel plant. Storage tanks hold raw soybeans, crude oil, refined oil, methanol, and final biodiesel. Pumps and piping systems facilitate material transfer between units.
Heating systems, including boilers and heat exchangers, provide the required thermal energy for extraction, refining, and transesterification processes. Control systems with sensors and automation enhance operational efficiency, safety, and product consistency.
Conclusion
The production of biodiesel from soybeans relies on a complex series of machines designed for cleaning, oil extraction, refining, and chemical conversion. Each machine plays a vital role in ensuring that raw soybeans are efficiently transformed into high-quality biodiesel fuel.
Advances in processing machinery continue to improve the sustainability and economics of soybean-based biodiesel, helping meet growing energy demands with renewable resources. Understanding these machines offers a glimpse into the technology behind one of the world’s most promising biofuels.