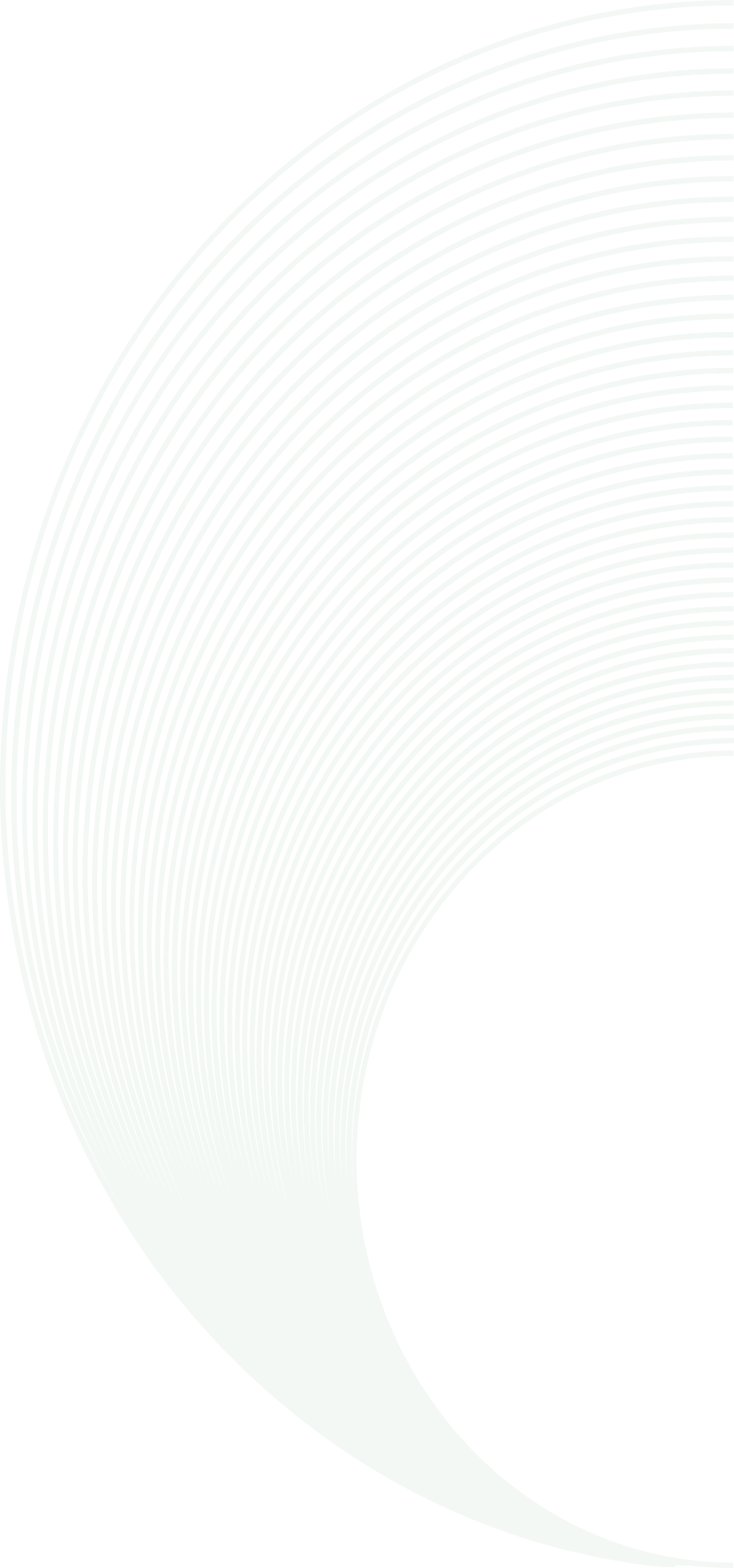
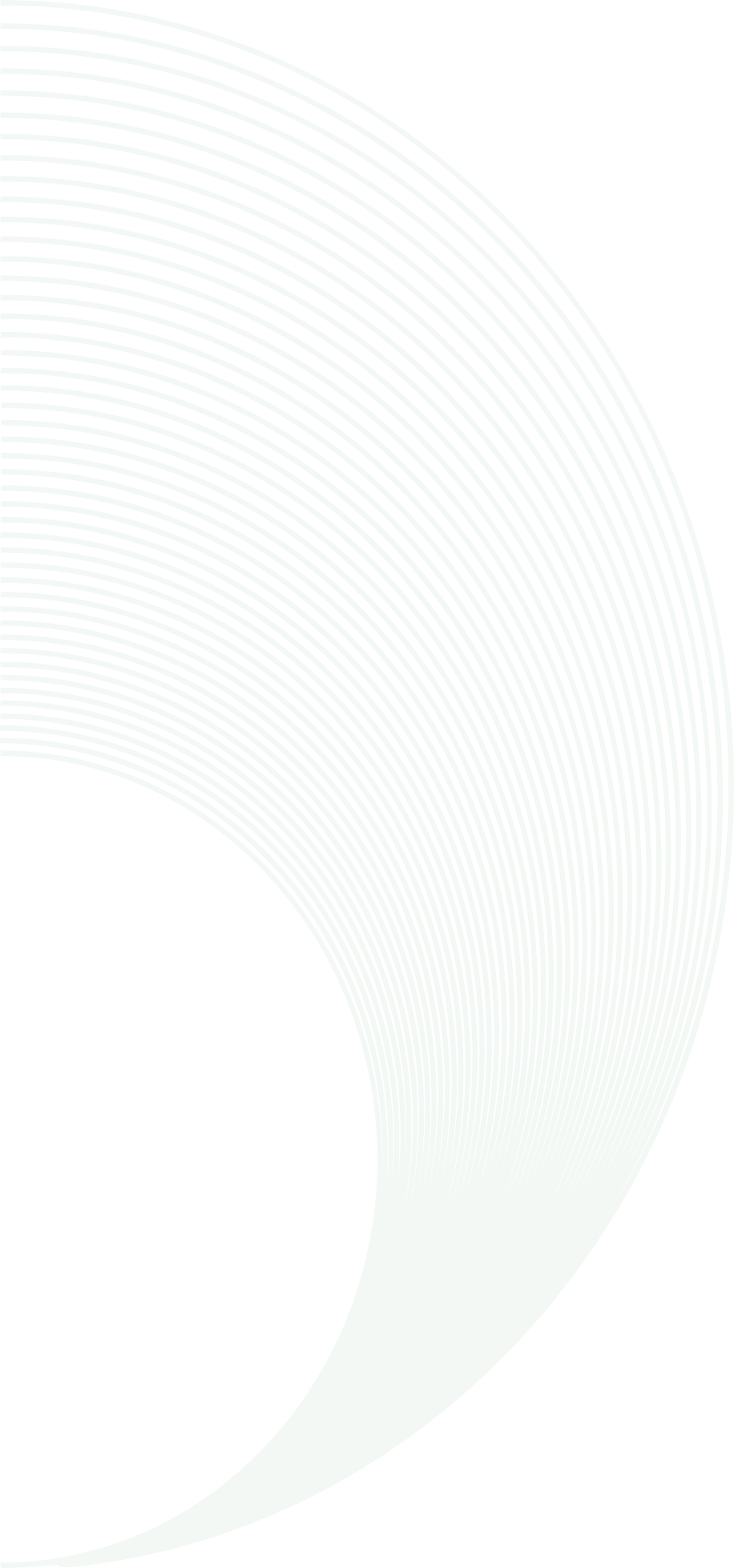
Types of Extensometers and Their Applications in Material Testing
Extensometers are vital tools in the field of material testing, allowing precise measurement of how materials deform under various forms of stress. These instruments are widely used in research laboratories, industrial quality control settings, and structural engineering applications to measure strain and elongation.
By accurately capturing how a material stretches or contracts, extensometers provide critical data about its mechanical properties such as tensile strength, yield strength, elastic modulus, and ductility. Different materials and testing conditions call for different types of extensometers, each designed with specific capabilities and technologies to match the demands of the application.
Mechanical Extensometers
Mechanical extensometers are among the earliest forms of extensometers developed and are still widely used today due to their simplicity, durability, and reliability. These devices physically attach to the specimen being tested using knife edges or clamps and rely on mechanical linkages to transfer the movement of the specimen to a dial or digital readout.
They are especially popular in testing metals and other rigid materials because they offer direct, repeatable measurements without requiring complex electronics. However, their physical contact with the specimen can be a drawback when testing delicate, high-strain, or high-temperature materials, as it may affect the behavior of the specimen or introduce measurement errors due to slippage or inertia.
Despite these limitations, mechanical extensometers remain cost-effective solutions for many standardized tensile and compression tests where non-contact methods are not necessary. Their rugged construction also makes them suitable for harsh environments and repeated use.
Strain Gauge Extensometers
Strain gauge extensometers, also known as electrical resistance extensometers, use strain-sensitive electrical elements bonded to a backing material. As the material under test stretches or compresses, the strain gauge also deforms, causing its electrical resistance to change. This change is measured and translated into a strain value.
This type of extensometer is ideal for applications requiring high-resolution measurements and continuous data acquisition. Strain gauges are often integrated into structural components or materials where permanent monitoring is necessary, such as in bridges, aircraft, and industrial machinery.
They offer a wide measurement range and are relatively unaffected by vibrations, making them ideal for dynamic or long-term testing. However, the installation process can be labor-intensive and must be performed with care to ensure accuracy. Environmental factors like temperature changes and humidity can also affect readings unless properly compensated for.
Video and Optical Extensometers
Video extensometers represent a non-contact approach to strain measurement by using high-speed cameras and digital image processing software to track changes in the position of patterns or marks placed on the specimen. As the specimen deforms, the video extensometer calculates the distance between the marks and determines the strain.
Optical extensometers operate on a similar principle, using lenses and light sources to measure displacement and strain. These systems are particularly useful when testing materials that are too fragile for contact-based devices or when high-precision data is required across a wide field of view.
Both video and optical extensometers eliminate the influence of mass or attachment pressure on the specimen, making them suitable for materials like thin films, composites, or biological tissues. Additionally, they are invaluable in high-temperature testing where physical contact would not be possible due to material degradation or equipment damage.
Their main drawbacks include higher cost and the need for clean, well-lit environments to ensure measurement accuracy. Still, their ability to collect detailed data without interfering with the specimen makes them a preferred choice in advanced research and sensitive testing applications.
Laser Extensometers
Laser extensometers are another category of non-contact instruments that use laser beams to measure the deformation of materials. These devices project a laser onto the specimen and detect the reflected beam's position using photodetectors or high-resolution sensors.
Laser extensometers are valued for their extremely high accuracy and ability to function in situations where traditional contact-based extensometers would fail. They are ideal for testing brittle or high-temperature materials and are often used in testing thin wires, ceramics, and advanced composites.
Their non-invasive nature allows them to record minute displacements with minimal interference from environmental variables. However, like video extensometers, they require controlled environments and specialized training to operate. Laser systems also tend to be more expensive and are typically reserved for high-end applications in aerospace, nuclear, and cutting-edge materials science.
Choosing the Right Extensometer
Selecting the appropriate extensometer depends on a combination of factors including the material type, the expected strain range, the required accuracy, and the testing conditions. For instance, a basic tensile test on a metal rod in a laboratory might only require a mechanical extensometer, whereas a test on a delicate composite in a thermal chamber may demand an optical or laser-based system.
Durability, ease of calibration, cost, and data output format also influence the selection process. In industrial environments where repeatability and robustness are more important than ultra-fine accuracy, mechanical or strain gauge extensometers are often preferred. In contrast, research and development settings, where precision and flexibility are paramount, tend to favor advanced video, optical, or laser technologies.
Conclusion
Extensometers play a critical role in the accurate evaluation of material behavior under load. Their ability to measure strain and deformation with high fidelity allows engineers and scientists to develop better materials, ensure structural integrity, and comply with rigorous quality standards. From simple mechanical devices to sophisticated laser and optical systems, the range of extensometer types available today ensures that every testing scenario has a suitable tool.
Understanding the differences between each type—and the contexts in which they excel—is essential for accurate material testing. By matching the right extensometer to the right application, one can achieve reliable results, minimize errors, and advance both practical engineering and scientific discovery.