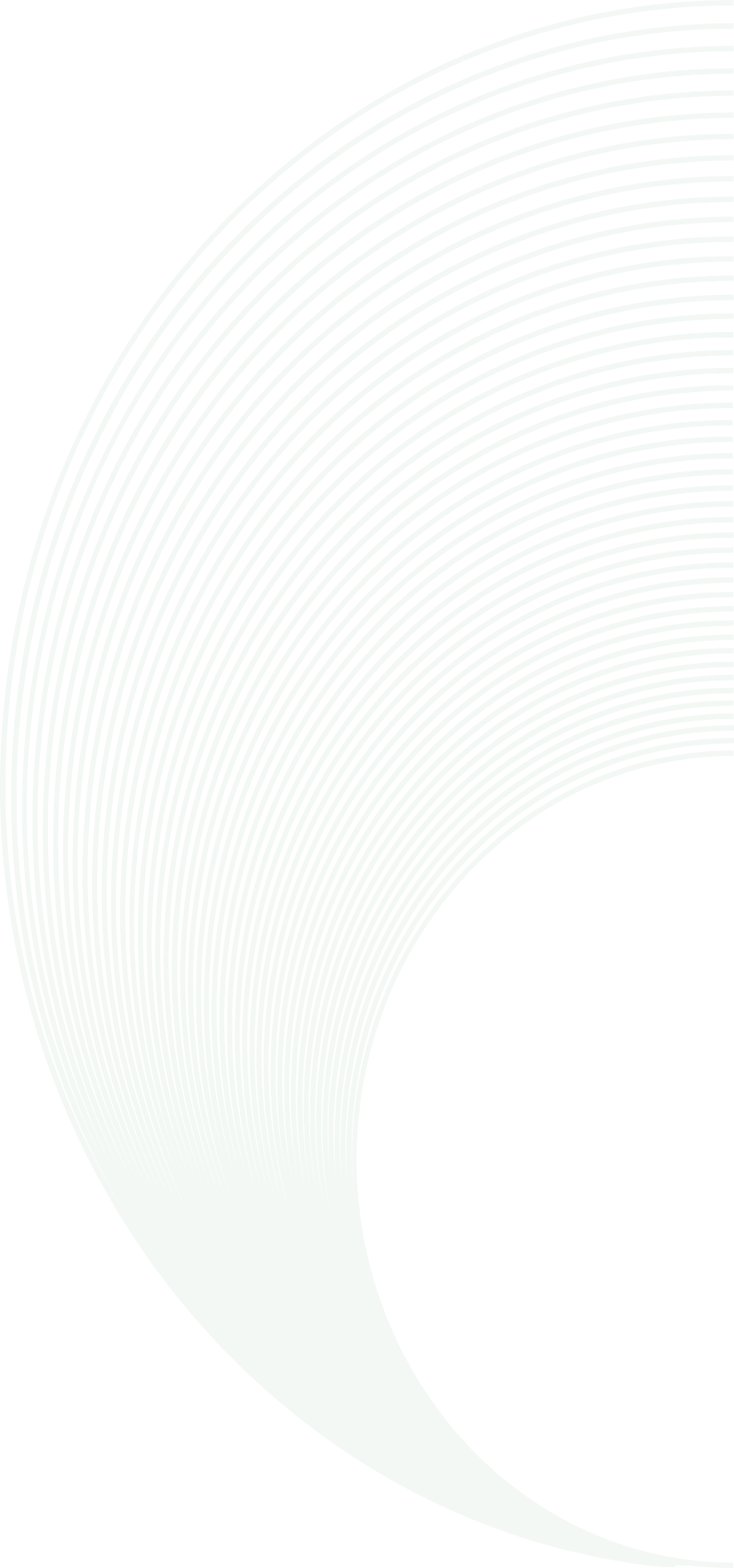
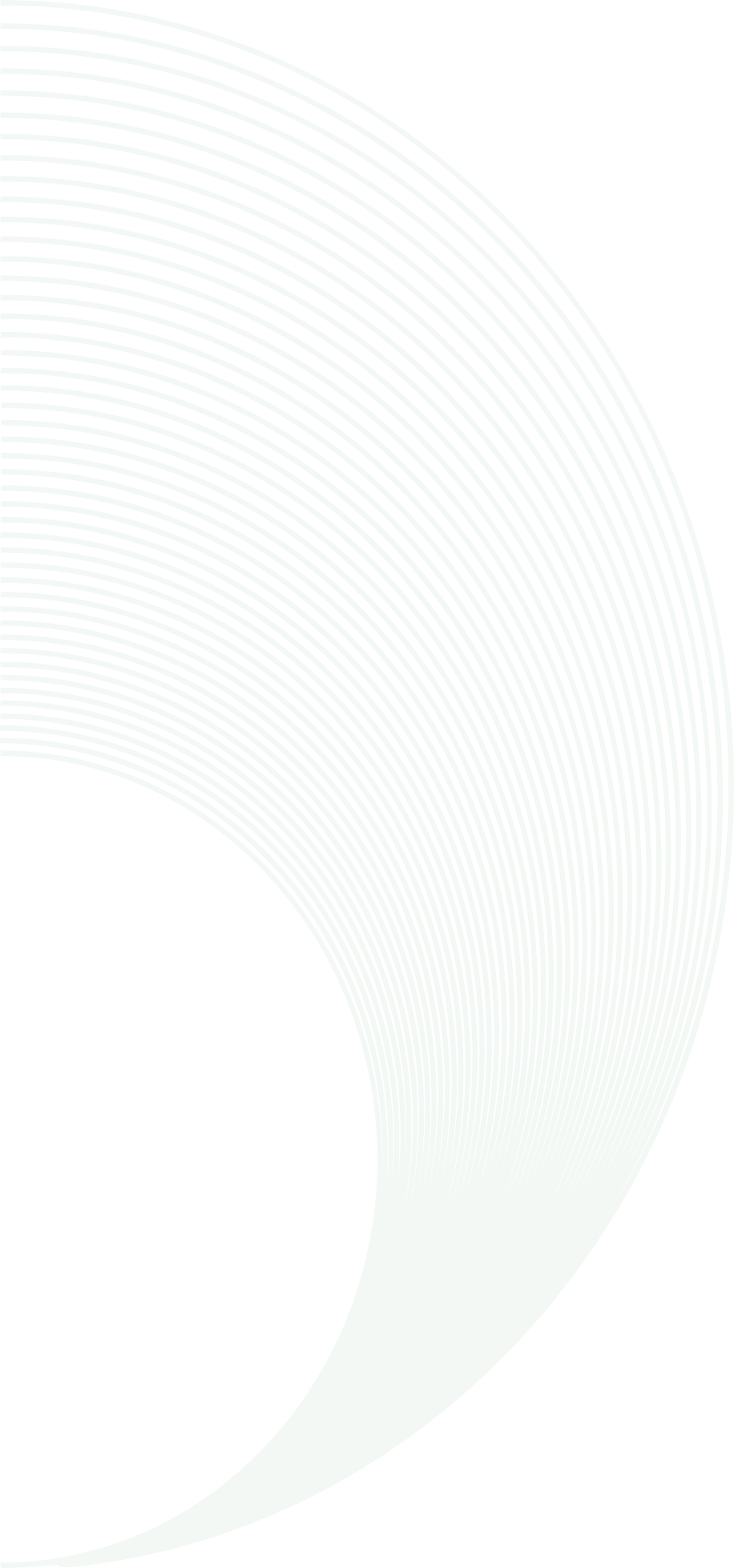
Air Slip Casting Machine: Precision Molding for High-Quality Ceramic Production
Ceramic manufacturing requires precision and efficiency, and an air slip casting machine plays a crucial role in achieving both. This advanced technology enhances the slip casting process, ensuring uniform mold filling, reduced defects, and improved production speed. Whether used for tableware, sanitary ceramics, or industrial applications, these machines optimize manufacturing for superior product quality.
How an Air Slip Casting Machine Works
Air slip casting machines automate the process of shaping ceramics using liquid clay (slip) poured into porous molds. The key features include:
Compressed Air Pressure System: Ensures consistent slip distribution for even mold filling.
Vacuum-Assisted Drainage: Speeds up water removal for faster solidification.
Automatic Mold Release: Reduces handling time and minimizes defects.
Programmable Controls: Allows precise adjustments for different ceramic compositions.
Advantages of Using an Air Slip Casting Machine
Enhanced Production Efficiency: Reduces casting time while increasing output capacity.
Consistent Product Quality: Minimizes variations and defects in ceramic shapes.
Lower Material Waste: Precise slip control reduces excess usage and improves yield.
Labor Cost Savings: Automation minimizes manual intervention, improving workforce efficiency.
Versatility: Suitable for a wide range of ceramic products, from fine porcelain to industrial components.
Industries That Benefit from Air Slip Casting Machines
Various industries rely on slip casting technology for their manufacturing processes, including:
Tableware Production: Creates uniform ceramic plates, cups, and bowls.
Sanitary Ware Manufacturing: Forms bathtubs, sinks, and toilet bowls with precision.
Industrial Ceramics: Produces heat-resistant and insulating components for machinery.
Decorative Ceramics: Facilitates intricate designs for artistic pottery and collectibles.
Selecting the Right Air Slip Casting Machine
When choosing a machine for your production needs, consider these factors:
Capacity & Throughput: Ensure the machine meets your required output volume.
Mold Compatibility: Check if it supports different mold sizes and materials.
Automation Features: Opt for programmable controls for process customization.
Durability & Maintenance: Look for models with long-lasting components and minimal upkeep requirements.
Energy Efficiency: Reduce operating costs with a system designed for low power consumption.
Why Now is the Best Time to Upgrade to an Air Slip Casting Machine
With increasing demand for high-quality ceramic products and the need for efficient production, investing in an air slip casting machine can enhance your manufacturing capabilities. By adopting this technology now, businesses can improve product consistency, reduce costs, and stay competitive in the growing ceramics industry.