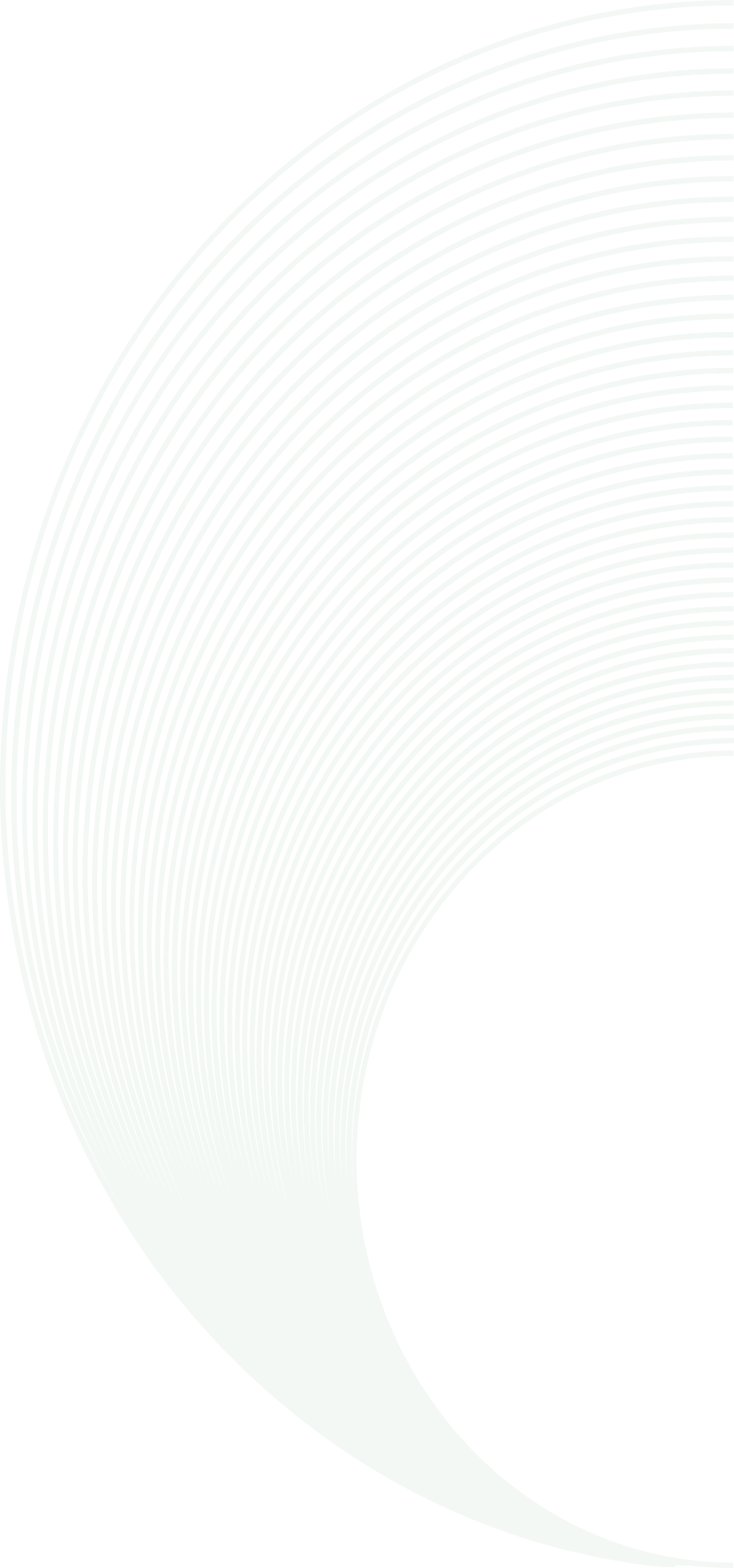
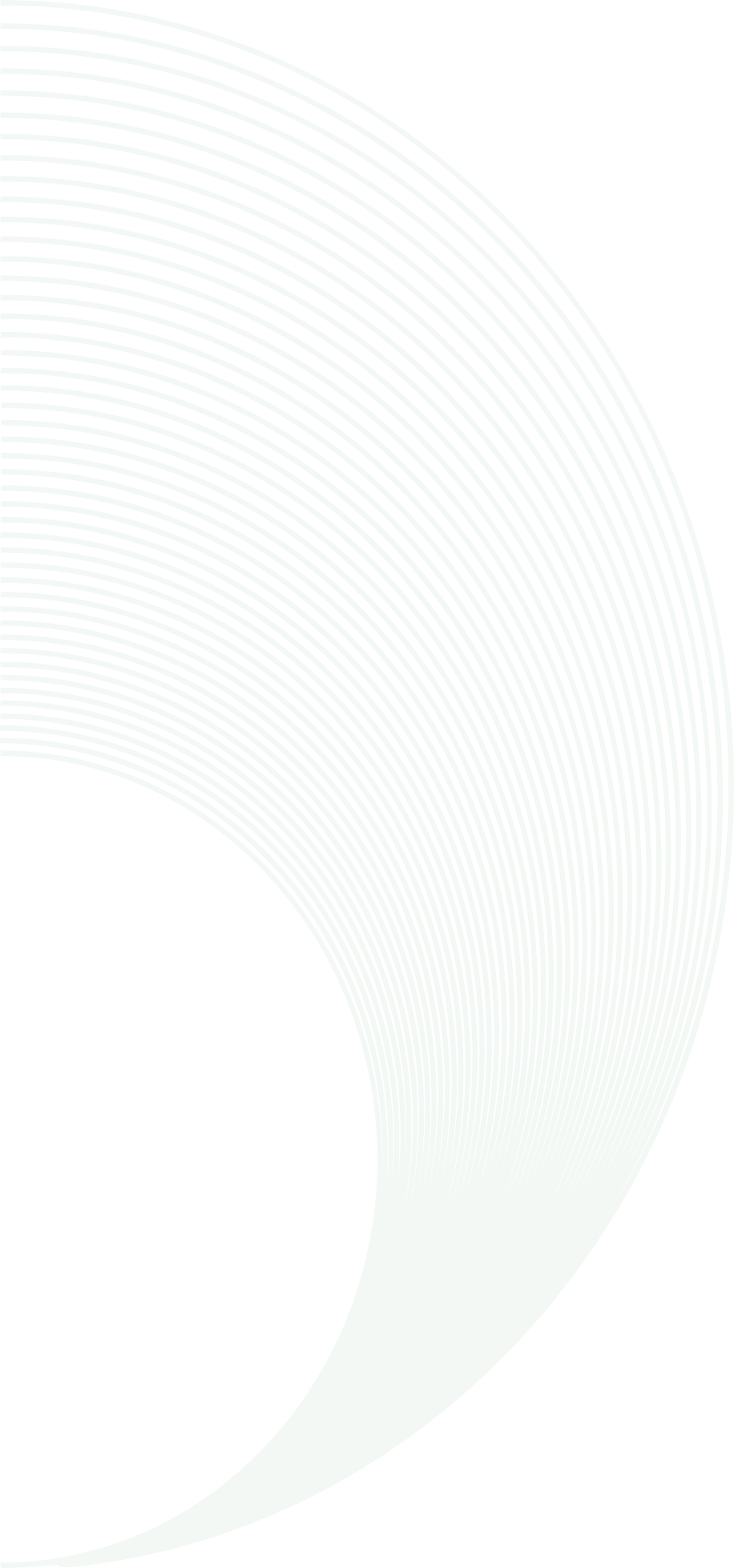
Automated System for Quality Analysis of Sugar: Enhancing Precision and Efficiency
In the sugar industry, maintaining high-quality standards is essential for both consumer satisfaction and regulatory compliance. Traditional methods of sugar quality analysis can be time-consuming, labor-intensive, and prone to human error.
What is an Automated System for Quality Analysis of Sugar?
An automated system for quality analysis in sugar production is designed to continuously monitor and assess various quality parameters of sugar, such as purity, moisture content, color, and granulation.
Using advanced sensors, automated analyzers, and real-time data processing, these systems provide quick and reliable results. The data collected is used to make immediate adjustments to production processes, ensuring that sugar meets the desired specifications and quality standards.
Key Features of an Automated Quality Analysis System
Real-Time Monitoring
One of the main advantages of automated systems is their ability to provide real-time data on sugar quality. Sensors integrated into the production line continuously monitor factors such as moisture, color, and granulation. This allows for immediate adjustments to be made, reducing waste and ensuring that the final product meets quality standards consistently.
Precision and Accuracy
Automated quality analysis systems offer higher precision and accuracy compared to manual testing methods. Sensors and analyzers are capable of detecting even minute variations in sugar quality parameters, ensuring that all products meet stringent specifications. This eliminates the potential for human error and variability, resulting in a more consistent product.
Data Logging and Reporting
Automated systems often come with built-in data logging capabilities, allowing for detailed reporting and traceability. The data collected can be stored for future reference and analysis, helping producers track quality trends over time. These reports can also be used for regulatory compliance and to identify areas for process improvement.
Integration with Production Systems
Automated quality analysis systems can be seamlessly integrated with other automated production systems. For example, the quality analysis data can be linked to production control systems that adjust parameters like temperature, humidity, or processing time based on the quality results. This ensures that the production process remains optimal and that quality deviations are quickly addressed.
Minimized Human Intervention
By reducing the need for manual sampling and testing, automated systems streamline the quality analysis process and minimize the risk of contamination or operator errors. The system's ability to perform continuous monitoring ensures that any deviations from quality standards are promptly detected and corrected, enhancing overall operational efficiency.
Benefits of Automated Sugar Quality Analysis
Improved Efficiency and Productivity
Automating the quality analysis process significantly reduces the time and labor required for testing. This leads to faster production cycles and increased throughput. With less downtime and fewer delays in the production process, companies can meet customer demand more effectively while maintaining high-quality standards.
Cost Reduction
While implementing an automated system may involve an initial investment, the long-term savings in labor costs, testing equipment, and waste reduction are significant. Automated systems reduce the frequency of manual inspections, increase process reliability, and reduce the amount of sugar that fails to meet quality standards, ultimately lowering production costs.
Consistent Product Quality
Consistency is key in the food industry, and automated quality analysis systems ensure that each batch of sugar is produced to the same high standard. With real-time data and continuous monitoring, any issues that arise can be addressed immediately, reducing the chances of subpar products reaching the market.
Regulatory Compliance
The sugar industry is subject to stringent regulations and quality control standards. Automated systems provide accurate, real-time data that helps sugar producers stay in compliance with local and international quality standards. This ensures that the products are safe for consumption and meet the required regulatory benchmarks.
Enhanced Traceability
Automated systems offer advanced traceability features, allowing producers to track the quality of each batch throughout the production process. This is particularly important in the event of product recalls or quality concerns, as it allows for quick identification of affected products and ensures transparency in quality assurance practices.
Applications of Automated Quality Analysis in the Sugar Industry
Moisture Content Analysis
Moisture content is a critical parameter in sugar quality, affecting its texture, preservation, and sweetness. An automated system can measure moisture levels continuously during the production process, ensuring that the sugar is neither too wet nor too dry, which could impact product quality or storage.
Color Measurement
Color is an important quality attribute, especially in refined sugar. Automated systems can measure color with high precision, detecting any variations that may indicate inconsistencies in the refining process. This ensures that the sugar meets the desired appearance and is consistent from batch to batch.
Granulation and Particle Size Analysis
Granulation refers to the size and distribution of sugar crystals, which is vital for both the appearance and performance of the sugar in various applications. Automated systems can continuously monitor the granulation of sugar, making adjustments as necessary to ensure that the sugar meets the required particle size specifications.
Purity Analysis
Sugar purity, or the percentage of sucrose in the product, is one of the most important quality parameters. Automated systems can perform high-precision purity analysis through sensors and spectroscopy, allowing for real-time adjustments to improve sugar refinement and ensure the highest level of purity.
Challenges and Considerations
Initial Investment and Setup
While the benefits of automated quality analysis systems are clear, the initial investment in technology, installation, and training can be significant. Companies must weigh the cost against the long-term benefits, including improved efficiency, cost savings, and product quality.
System Calibration and Maintenance
Like any automated system, continuous calibration and maintenance are crucial to ensure accurate and reliable results. Regular servicing and recalibration of sensors are necessary to maintain the system's precision and avoid issues related to sensor drift or malfunctions.
Integration with Existing Systems
For businesses that already have established production lines, integrating an automated quality analysis system with existing systems may pose technical challenges. However, modern systems are designed to be flexible and adaptable, offering seamless integration with most production control systems.
Conclusion
Automated systems for quality analysis of sugar are transforming the sugar industry by offering a more efficient, accurate, and consistent approach to quality control. By providing real-time monitoring, reducing human error, and improving efficiency, these systems help manufacturers ensure that their products meet the highest standards. Whether it's measuring moisture content, granulation, color, or purity, automated systems play a crucial role in enhancing the overall quality of sugar and streamlining production processes. While the initial investment can be high, the long-term benefits of automation—such as cost savings, increased productivity, and improved product consistency—make it a worthwhile investment for any sugar producer.