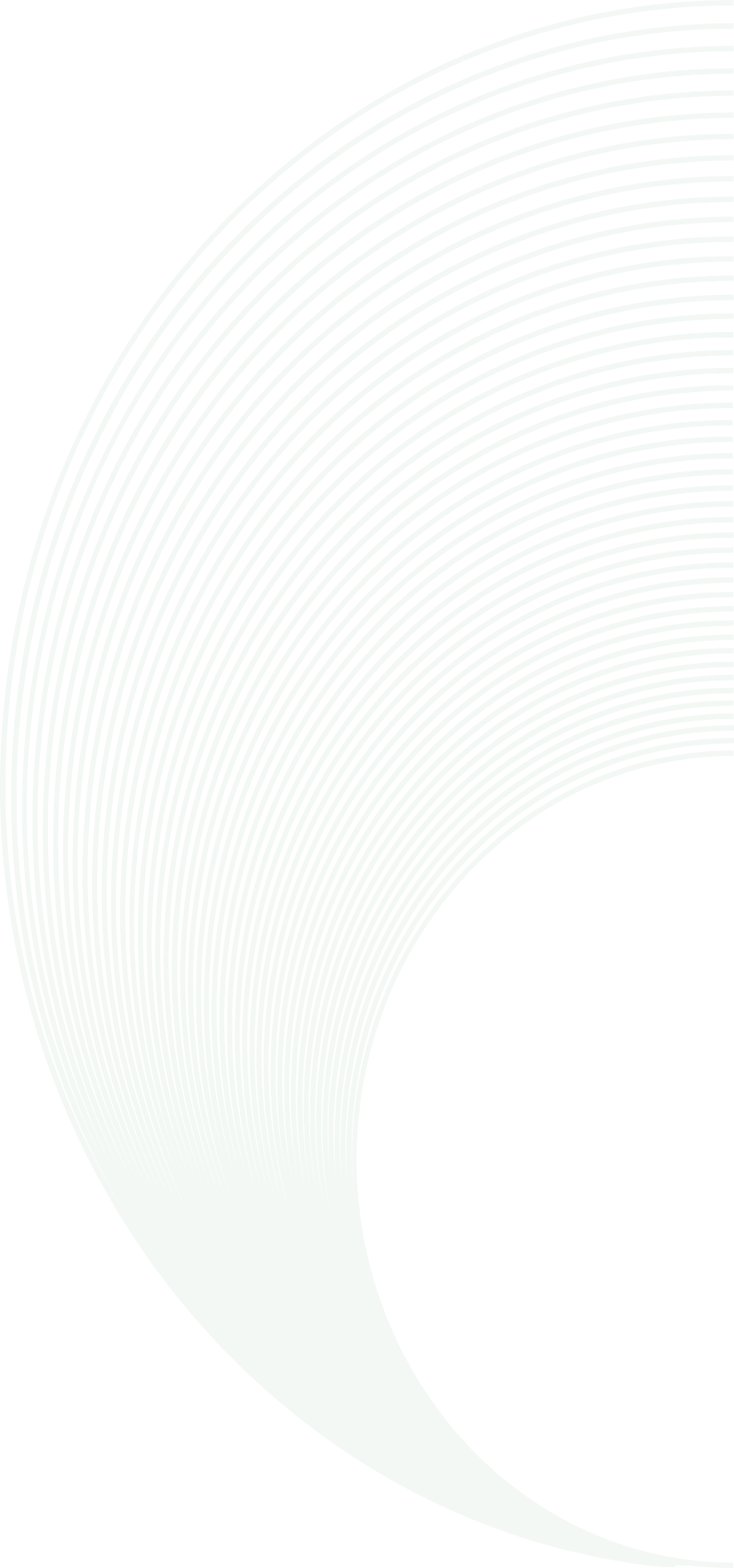
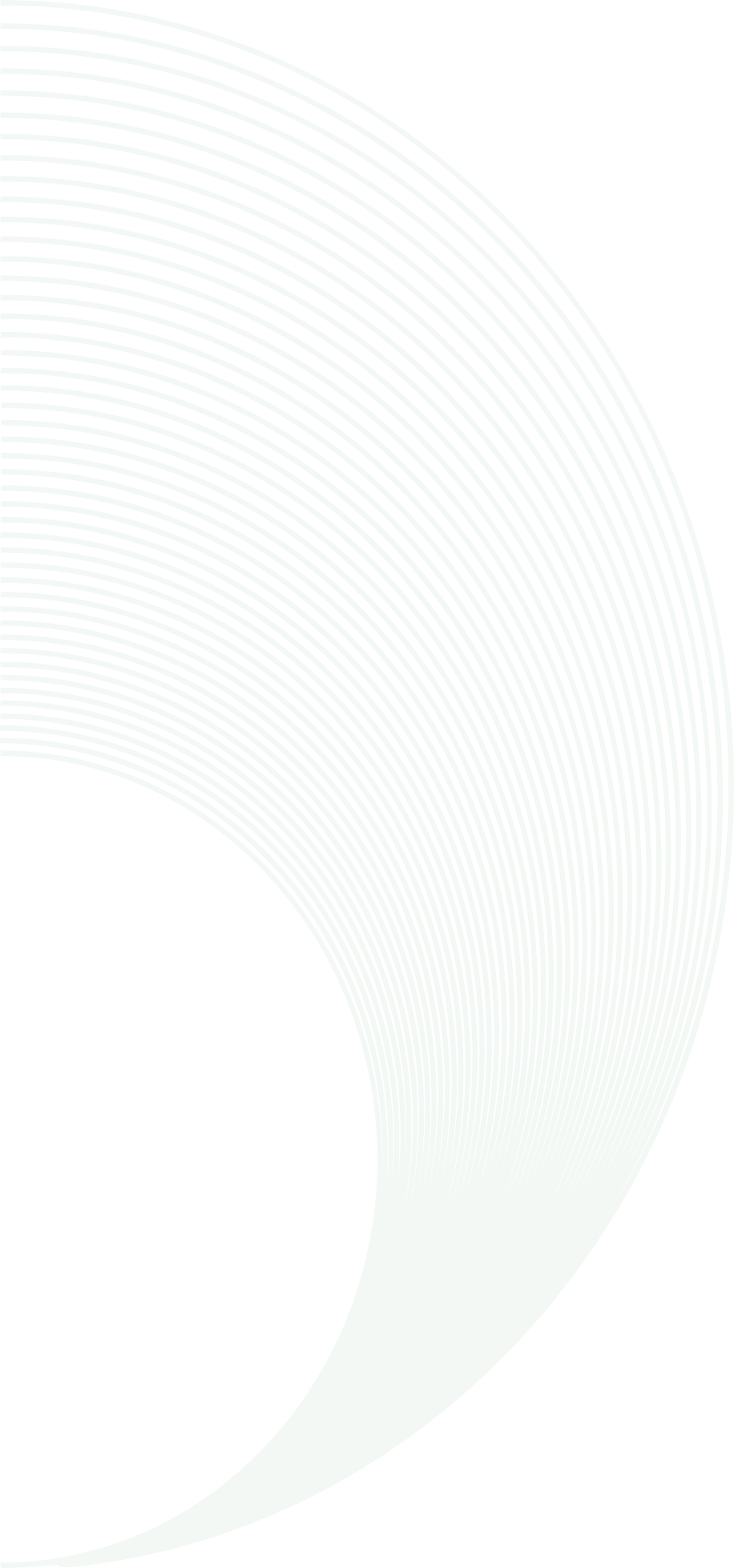
Automation Weight Indicator Systems: Revolutionizing Industrial Weighing
In industries where accurate measurements are critical, such as manufacturing, logistics, and food processing, automation weight indicator systems play a key role in ensuring precision and efficiency. These systems provide real-time weight data, integrate seamlessly with other equipment, and enhance the overall functionality of automated production lines.
What Are Automation Weight Indicator Systems?
Automation weight indicator systems are advanced electronic devices designed to measure and display the weight of materials or products in real-time.
These systems are often integrated into automated processes, helping industries streamline production lines, improve accuracy, and reduce human error. The weight indicators can communicate with load cells or other weighing components to provide instant feedback, making them an integral part of automated weighing processes.
The key components of these systems typically include a load cell (which measures weight), a signal amplifier (which processes the data), and the weight indicator unit (which displays the measurements). The weight indicators are equipped with digital screens and can be connected to other systems for enhanced automation and data logging. Some models even offer features such as alarms for weight deviations, automatic tare functions, and customizable settings for various types of materials and production processes.
Key Functions of Automation Weight Indicator Systems
Real-Time Weight Monitoring
One of the main functions of automation weight indicator systems is real-time monitoring of material weights. Whether it’s monitoring ingredients in a food processing plant or checking product weights in a manufacturing facility, the weight indicator provides accurate, up-to-the-minute data. This helps prevent overloading or underloading, which could lead to quality issues or inefficiencies in production.
Integration with Automated Systems
Automation weight indicators are designed to integrate with other automated systems, such as conveyor belts, robotic arms, and batch processing equipment. This integration ensures seamless flow through production lines, reducing the need for manual data entry or adjustments. For example, when a weight deviation is detected, the system can automatically stop the process, preventing errors and ensuring consistency.
Data Logging and Reporting
Advanced automation weight indicator systems come with data logging features, allowing industries to track and store weight data for future analysis. These records are crucial for quality control, regulatory compliance, and performance tracking. Reports can be generated for batch monitoring, inventory management, and even customer documentation, ensuring traceability and transparency in the production process.
Multiple Units Integration
Many industries require multiple weight indicator systems operating simultaneously in different parts of their production process. Modern automation weight indicator systems allow for the integration of multiple units, with centralized monitoring and control. This feature ensures that all parts of the production line are synchronized, and any weight-related discrepancies can be detected and addressed promptly.
Accuracy and Calibration
Precision is a critical factor in industrial operations, and automation weight indicator systems are built for high accuracy. With frequent calibration and real-time monitoring, these systems maintain tight tolerances and deliver consistent, reliable measurements. This ensures that the correct weight is always maintained, reducing material waste, improving product quality, and minimizing errors.
Advantages of Automation Weight Indicator Systems
Increased Efficiency and Productivity
By automating the weighing process, these systems eliminate the need for manual checks and adjustments, saving both time and labor costs. Integration with automated production lines means that the weighing process happens simultaneously with other tasks, reducing bottlenecks and improving overall throughput.
Enhanced Accuracy
Human error can lead to significant inaccuracies in weight measurement, which can negatively impact production. Automation weight indicator systems are highly accurate and provide precise measurements with minimal error. This leads to better consistency in the final product and minimizes waste, both of which contribute to higher profits.
Reduced Downtime
The ability to integrate weight indicator systems with automated machinery helps reduce unplanned downtime. With continuous monitoring and instant alerts for any discrepancies, production lines can be stopped or adjusted immediately to address weight imbalances, preventing the need for costly repairs or material loss.
Cost-Effective Solution
While the initial investment in automation weight indicator systems might seem significant, the long-term savings are substantial. Reduced labor costs, increased production efficiency, and minimized material waste contribute to a more cost-effective operation. Additionally, automated systems reduce the likelihood of errors that could lead to expensive product recalls or regulatory fines.
Compliance and Quality Control
Many industries, especially food processing and pharmaceuticals, are required to meet stringent regulatory standards. Automation weight indicator systems help maintain compliance by providing accurate and traceable records of product weights. These systems also support quality control measures, ensuring that products meet the required specifications for weight and consistency.
Applications of Automation Weight Indicator Systems
Manufacturing
In manufacturing, automation weight indicator systems are used to ensure that materials are weighed accurately for production. Whether it's batching raw materials or verifying the weight of finished products, these systems help maintain the correct balance, preventing costly errors and product defects.
Food Processing
Food processing plants use automation weight indicator systems to measure ingredients, ensure correct packaging weights, and check finished product weight consistency. These systems ensure that the correct amount of ingredients is used, maintaining the quality and taste of food products while complying with regulatory standards.
Chemical and Pharmaceutical Industries
In the chemical and pharmaceutical industries, accuracy is crucial for ensuring product quality and safety. Automation weight indicators help measure ingredients and maintain strict adherence to formulas. By providing real-time feedback, these systems contribute to precise formulations and batch consistency.
Logistics and Shipping
Weight indicators are also used in logistics and shipping, where accurate weight measurements are crucial for load balancing, packaging, and transportation. Automation weight indicator systems ensure that shipping containers are filled to capacity without exceeding weight limits, helping to optimize freight costs and reduce the risk of fines for overweight shipments.
Agriculture and Bulk Material Handling
In agriculture, bulk material handling requires accurate weighing for products like grains, fertilizers, and animal feed. Automation weight indicators assist with batching and weighing products, ensuring consistency and reducing waste. These systems improve the efficiency of inventory management and ensure that products are sold at the correct weight.
Challenges and Considerations
Initial Setup and Calibration
While automation weight indicator systems offer numerous advantages, setting them up and calibrating them for specific applications can be challenging. It’s important to ensure that the system is compatible with existing equipment and that the weight sensors are correctly calibrated to avoid inaccuracies.
Maintenance and Durability
Like any industrial system, weight indicator systems require regular maintenance to ensure continued accuracy and functionality. Wear and tear from constant use can affect the performance of load cells and sensors. Therefore, routine checks and calibration are essential to maintain system reliability.
Cost of High-End Models
Although automation weight indicator systems are cost-effective in the long run, high-end models with advanced features can be expensive. Small businesses or operations with lower volume requirements may need to assess their specific needs before investing in a more sophisticated system.
Conclusion
Automation weight indicator systems have become indispensable in industries where accurate measurements are crucial. With their ability to integrate seamlessly with automated processes, these systems ensure consistent, real-time weighing that helps increase productivity, reduce errors, and maintain quality control. Whether in manufacturing, food processing, pharmaceuticals, or logistics, automation weight indicator systems contribute to operational efficiency and cost savings. As industries continue to adopt advanced automation, the role of these systems in maintaining precise weight measurements will only grow more important.