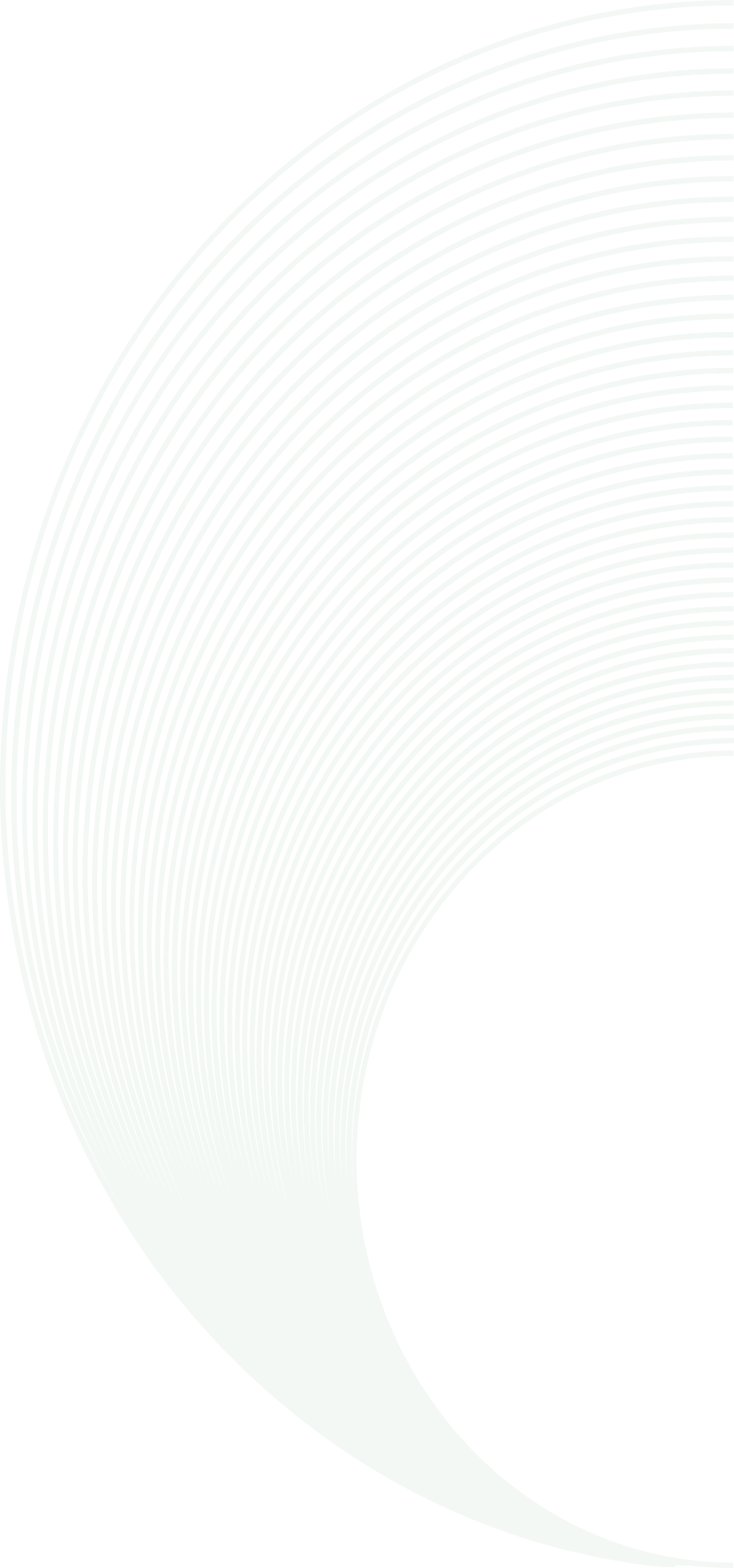
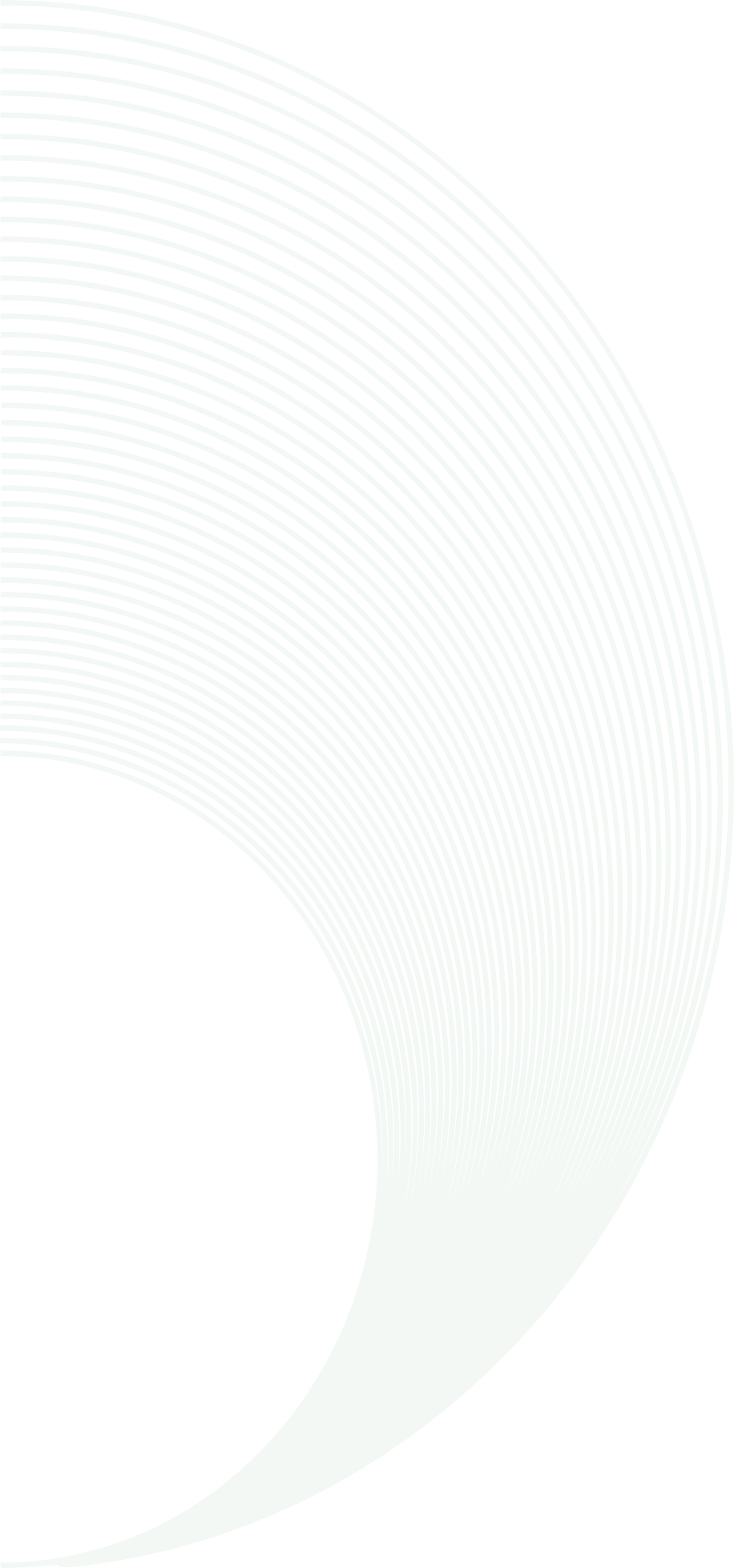
Bridge Circuit Operation for RTD in Temperature Measurement
The bridge circuit is commonly used in temperature measurement systems, particularly when working with Resistance Temperature Detectors (RTDs). The bridge circuit enables precise temperature readings by converting the small resistance changes of an RTD into measurable voltage changes.
How the Bridge Circuit Works with RTDs
An RTD is a temperature sensor that measures temperature based on the change in electrical resistance of the material (usually platinum) with temperature.
The bridge circuit, typically a Wheatstone bridge, is used to measure the small changes in resistance of the RTD as the temperature changes. The bridge circuit is designed with a known resistance, a variable resistance (the RTD), and two other resistors to balance the bridge.
Components of the Wheatstone Bridge Circuit
- RTD (R1): The primary sensing element in the circuit, whose resistance changes with temperature.
- Resistors (R2, R3, and R4): These resistors are chosen to balance the bridge. R2 and R3 are typically fixed resistors, while R4 may be a variable resistor for fine adjustments.
- Voltage Source (V): A constant voltage is applied across the bridge circuit.
- Output Voltage (Vout): The voltage measured between two opposite points of the bridge circuit, which indicates the imbalance caused by the change in the RTD’s resistance.
Bridge Circuit Operation
Initial Balance: In the absence of a temperature change, the resistors in the bridge circuit are balanced. This means that the voltage drop across the circuit’s diagonal (Vout) is zero. The resistances of the RTD (R1) and the other resistors (R2, R3, R4) are selected such that the voltage is evenly distributed across the bridge.
Temperature Change: When the temperature of the RTD changes, its resistance also changes. For instance, as the temperature increases, the resistance of the RTD typically increases (this behavior is dependent on the material of the RTD).
Bridge Imbalance: As the resistance of the RTD changes, the bridge circuit becomes imbalanced, creating a non-zero output voltage (Vout). This voltage is proportional to the change in resistance of the RTD, and consequently, to the temperature change.
Measurement of Vout: The output voltage is small, so it is amplified using an instrumentation amplifier or operational amplifier to provide a readable voltage signal. This amplified signal is then converted into a temperature value using a pre-determined calibration curve or equation specific to the RTD’s characteristics.
Temperature Calculation: The relationship between resistance and temperature for the RTD is typically linear, allowing for an accurate calculation of the temperature based on the change in resistance. However, in some cases, a more complex equation (such as the Callendar-Van Dusen equation) is used for more precise temperature measurements.
Types of RTDs in Bridge Circuits
There are several types of RTDs used in bridge circuits, including:
- PT100: The most common type, where the RTD has a resistance of 100 ohms at 0°C.
- PT1000: Similar to the PT100, but with a resistance of 1000 ohms at 0°C, offering higher sensitivity.
- Other Materials: RTDs can also be made from materials other than platinum, though platinum RTDs are the most widely used due to their stability and wide temperature range.
Advantages of Using a Bridge Circuit for RTDs
- High Accuracy: The bridge circuit allows for high precision in temperature measurements due to its ability to detect small changes in resistance.
- Reduced Errors: By balancing the resistors in the bridge, errors due to lead resistance or other environmental factors can be minimized.
- Linearity: The response of RTDs in a bridge circuit is highly linear, which makes temperature calculations straightforward and accurate.
- Stable Readings: RTDs used in bridge circuits offer stable, repeatable measurements over a wide range of temperatures.
Practical Considerations
- Temperature Compensation: It is important to ensure proper compensation for environmental factors such as ambient temperature, especially if the bridge circuit is used in varying environmental conditions.
- Accuracy of Resistors: The accuracy of the resistors used in the bridge circuit is crucial, as any discrepancy can affect the measurement accuracy. Precision resistors should be used to maintain accurate readings.
- Calibration: RTDs and bridge circuits should be calibrated regularly to ensure consistent performance and accuracy. Calibration involves applying known temperatures and comparing the measured temperature to the actual value to adjust the system.
Conclusion
The bridge circuit, especially the Wheatstone bridge, plays a critical role in the operation of RTDs for temperature measurement. By accurately measuring the small resistance changes in the RTD, the bridge circuit enables precise temperature readings that are essential in industrial, scientific, and medical applications. Proper calibration and consideration of environmental factors are key to maximizing the accuracy and reliability of this temperature measurement system.