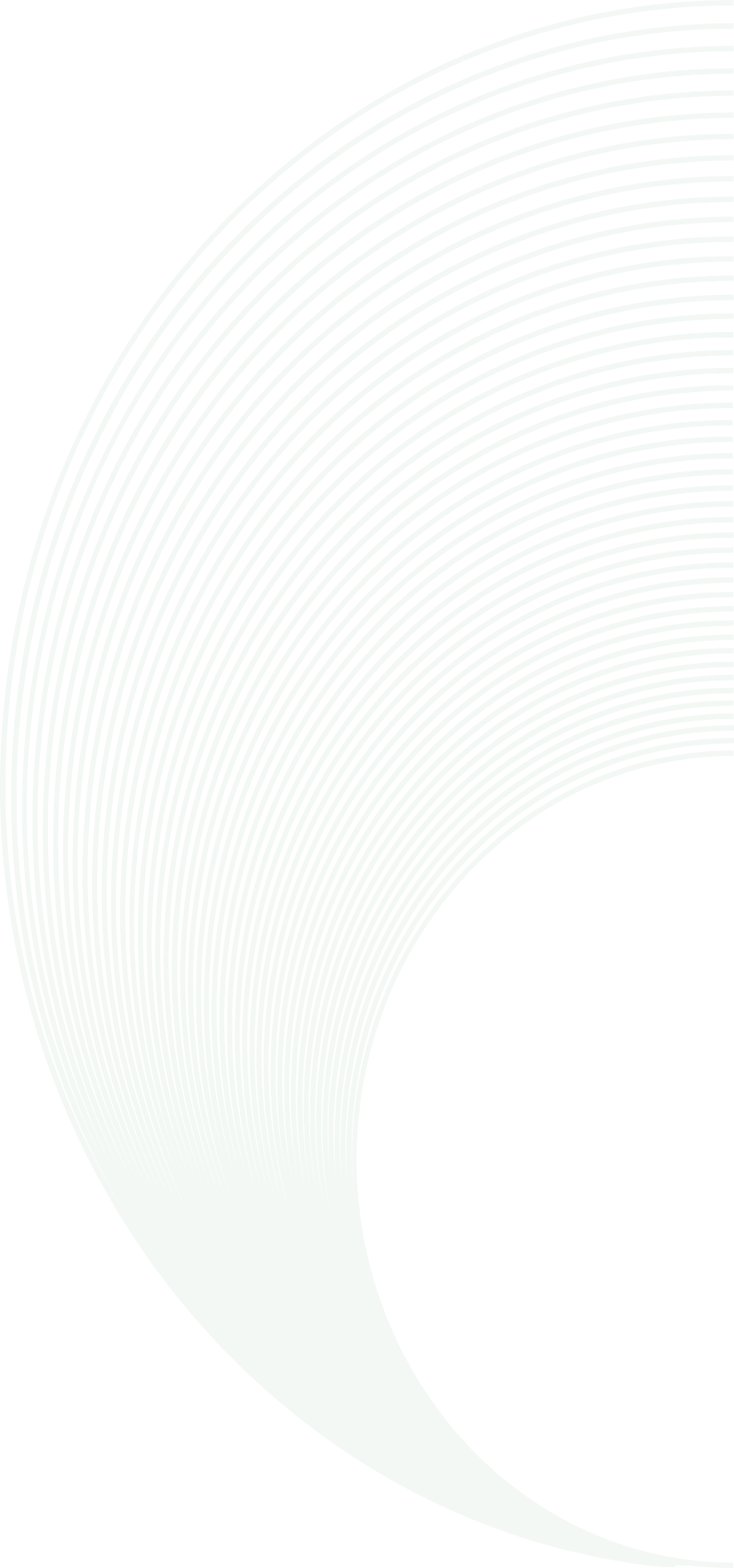
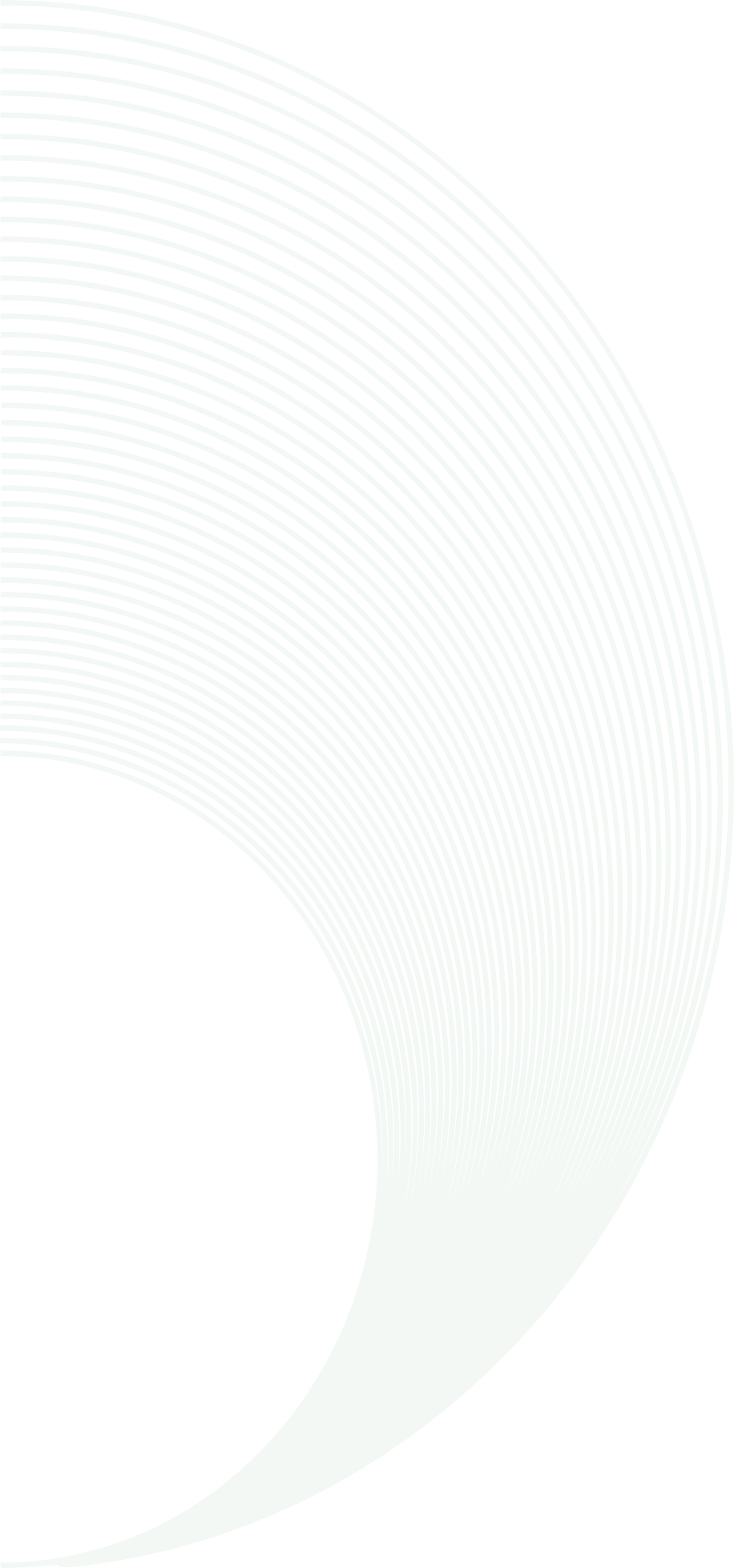
Double Acting Hydraulic Pump: How It Works and Its Applications
A double-acting hydraulic pump is a vital component in hydraulic systems, designed to provide fluid power to actuators, such as cylinders, by supplying pressurized hydraulic fluid. Unlike single-acting pumps, which only push or pull hydraulic fluid in one direction, a double-acting pump can deliver fluid in both directions. This makes it ideal for applications requiring back-and-forth motion, typically with double-acting hydraulic cylinders.
How a Double-Acting Hydraulic Pump Works
In a double-acting system, hydraulic fluid is delivered to both sides of a cylinder’s piston, allowing it to extend and retract based on the fluid pressure. The pump generates the necessary pressure to move fluid into one side of the cylinder, pushing the piston. At the same time, it extracts fluid from the opposite side, creating a continuous cycle of motion.
Key characteristics of how the pump works include:
- Two-Way Flow: The pump is capable of sending fluid into both the extend and retract chambers of a double-acting cylinder.
- Dual-Pressure Control: Fluid is pressurized in both directions, which allows for consistent movement of the piston in and out.
- More Control and Precision: With pressure applied in both directions, the system offers better control over force and speed during operations.
Components of a Double-Acting Hydraulic Pump
- Pump Body: Houses the internal mechanisms, usually a piston or gear system, that create the pressurized fluid flow.
- Inlet and Outlet Ports: These are the connections through which hydraulic fluid enters and exits the pump. Since it’s double-acting, the pump will have dual ports for both directions of flow.
- Pressure Relief Valve: Protects the system from over-pressurization by allowing excess fluid to bypass or return to the reservoir.
- Reservoir: A storage area for the hydraulic fluid when it is not being pumped.
- Control Valves: Direct the flow of fluid from the pump to the appropriate side of the hydraulic cylinder.
Advantages of Double-Acting Hydraulic Pumps
1. Bidirectional Control
A double-acting pump allows for both pushing and pulling forces, which makes it more versatile and efficient in applications requiring motion in two directions. This is especially useful in lifting, pressing, or moving applications where the hydraulic cylinder needs to extend and retract.
2. Increased Power
Because the pump can pressurize both sides of the piston, it provides greater force and control over the operation. This makes double-acting systems ideal for heavy-duty tasks.
3. Improved Efficiency
Double-acting pumps provide continuous power during both the extension and retraction phases, reducing downtime between movements and increasing operational efficiency.
4. Enhanced Precision
By controlling both directions of motion, double-acting hydraulic pumps allow for more precise and fine-tuned adjustments. This is crucial in applications requiring exact movements, such as in machinery or robotics.
Common Applications
1. Lifting Equipment
Double-acting hydraulic pumps are commonly used in hydraulic lifts and jacks, where precise, bidirectional control is needed to lift and lower heavy objects.
2. Industrial Machinery
In manufacturing and construction industries, double-acting pumps are used in presses, punching machines, and molding systems. These machines require controlled movements to push, press, and release materials.
3. Agricultural Equipment
Many agricultural machines, like plows and tractors, rely on double-acting hydraulic systems to control attachments and tools that require back-and-forth movement.
4. Automotive Applications
Double-acting hydraulic pumps are used in hydraulic brakes, suspension systems, and hoists in automotive garages. They offer the necessary control to raise and lower vehicles with precision.
5. Aerospace and Marine
The aerospace and marine industries also use double-acting hydraulic pumps for controlling landing gear, steering systems, and other mechanical components that require precise hydraulic actuation.
Factors to Consider When Choosing a Double-Acting Hydraulic Pump
1. Pressure Rating
The pump must be rated to handle the maximum pressure of the hydraulic system. Overloading a pump with too much pressure can lead to mechanical failure or system damage.
2. Flow Rate
The pump's flow rate determines how fast hydraulic fluid is delivered to the actuators. Higher flow rates generally mean quicker operation but may require larger systems to handle the fluid volume.
3. Size and Port Configuration
The physical size of the pump and the configuration of its ports must match the requirements of the system it's being used in. Always ensure that the pump’s dimensions fit the space and that its ports align with the hydraulic connections.
4. Power Source
Double-acting hydraulic pumps can be powered by electricity, gasoline, or manually (hand-operated pumps). The choice of power source depends on the application and operational environment.
Conclusion
A double-acting hydraulic pump is essential for systems that require movement in two directions, providing more control, power, and precision than single-acting pumps. From lifting equipment to industrial machinery, these pumps are used across a variety of industries for their efficiency and ability to deliver consistent hydraulic power in both extension and retraction phases. When choosing a double-acting pump, consider the pressure rating, flow rate, size, and power source to ensure it meets the specific requirements of your hydraulic system.