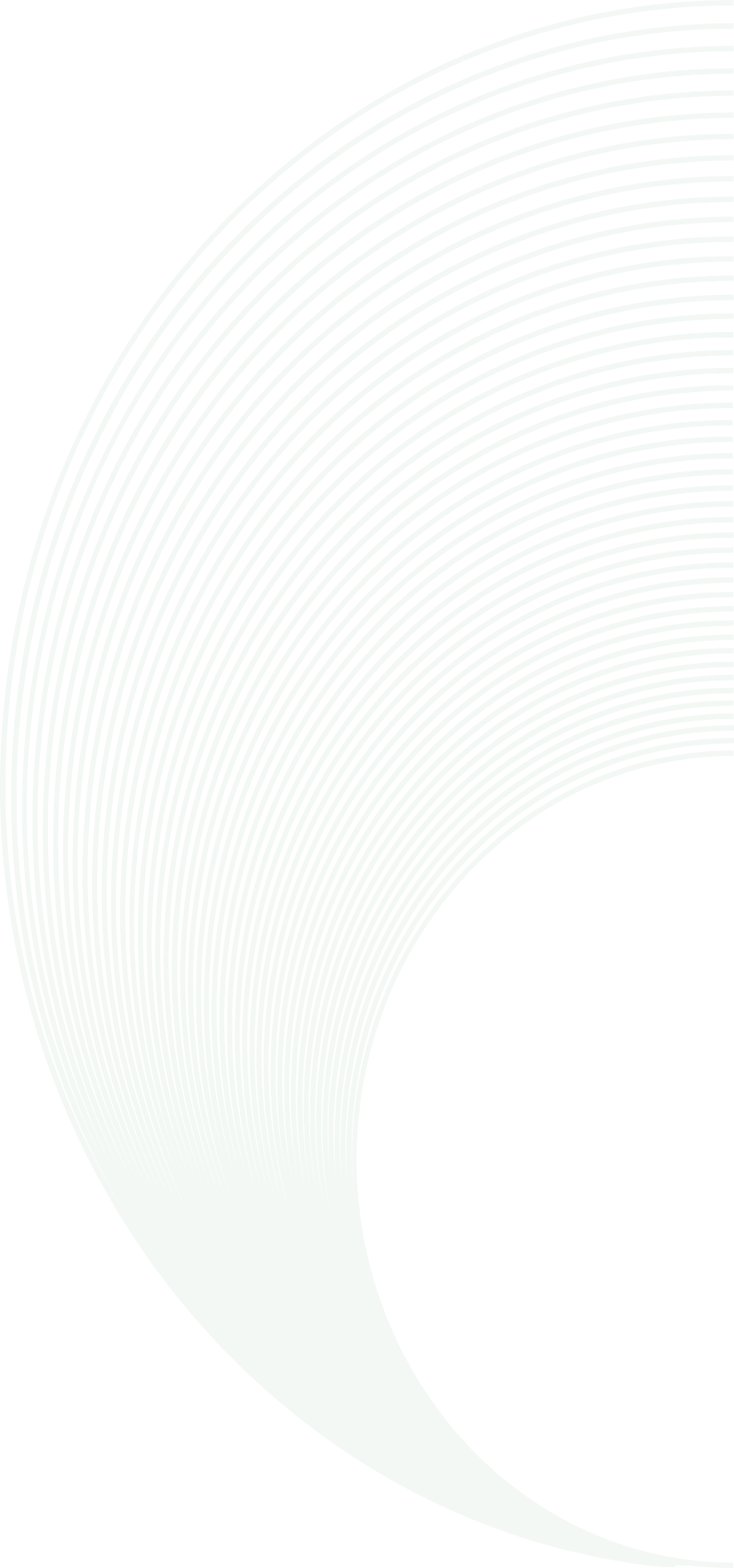
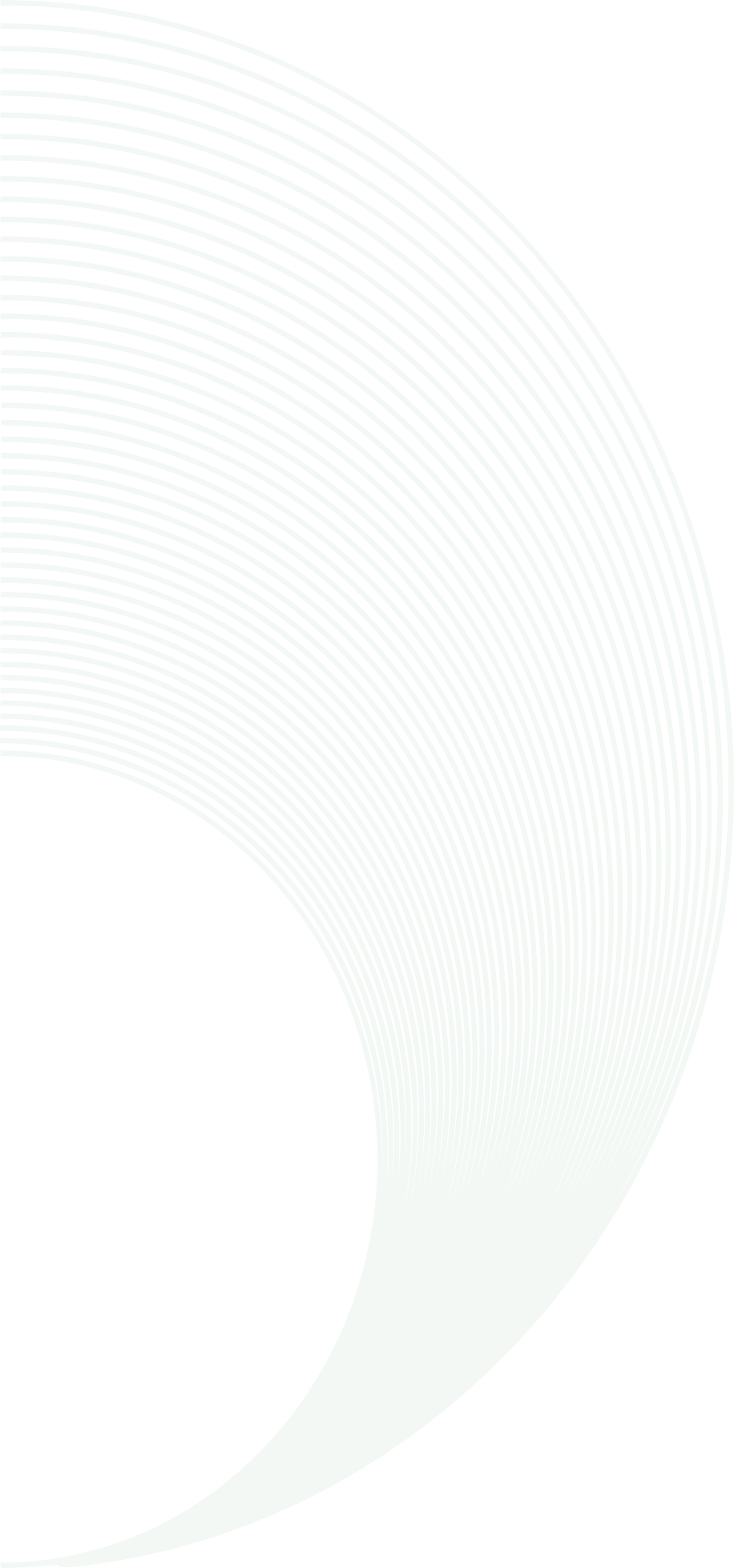
EDM Wire Cut Machine: Precision Cutting for High-Accuracy Manufacturing
Manufacturing industries require extreme precision, especially when working with hard metals and intricate designs. An EDM wire cut machine delivers superior accuracy using electrical discharge machining (EDM) technology, making it an essential tool for industries like aerospace, automotive, and tool and die manufacturing.
How an EDM Wire Cut Machine Works
EDM wire cut machines use a thin, electrically charged wire to cut through metal with high precision. The process involves:
Electrically Charged Wire: Generates controlled sparks to erode material without direct contact.
Deionized Water Bath: Cools the workpiece and removes debris for a smooth finish.
CNC-Controlled Movements: Ensures exact cutting paths with minimal errors.
Non-Contact Cutting: Reduces tool wear and allows for complex, fine details.
Advantages of Using an EDM Wire Cut Machine
Unmatched Precision: Achieves tolerances as tight as ±0.001mm.
No Mechanical Stress: Cuts without applying force, preventing material distortion.
Superior Surface Finish: Produces smooth edges, eliminating the need for additional finishing.
Versatile Material Compatibility: Works with hard metals like titanium, tungsten, and hardened steel.
Cost-Effective Production: Reduces tool wear and minimizes material waste.
Industries That Benefit from EDM Wire Cut Machines
EDM wire cut technology is widely used across various sectors, including:
Aerospace & Defense: Manufactures high-precision components for jet engines and weaponry.
Automotive Industry: Produces complex parts with tight tolerances for high-performance vehicles.
Medical Device Manufacturing: Ensures precise cutting for surgical instruments and implants.
Tool & Die Industry: Creates detailed molds and dies for mass production.
Electronics & Semiconductor: Cuts micro-components with extreme accuracy.
Choosing the Right EDM Wire Cut Machine
When selecting an EDM wire cut machine, consider:
Cutting Speed & Accuracy: Ensure the machine meets your production demands.
CNC Control System: Look for advanced automation for precise programming.
Wire Diameter Compatibility: Different wire thicknesses allow for varied cutting applications.
Maintenance & Operational Costs: Opt for models with low maintenance requirements.
Energy Efficiency: Reduces power consumption while maintaining performance.
Why Now is the Best Time to Invest in an EDM Wire Cut Machine
With the growing demand for high-precision components in industries such as aerospace and medical technology, upgrading to an EDM wire cut machine can give manufacturers a competitive edge. Investing in this technology now enhances production efficiency, ensures superior quality, and meets the increasing need for precision engineering.