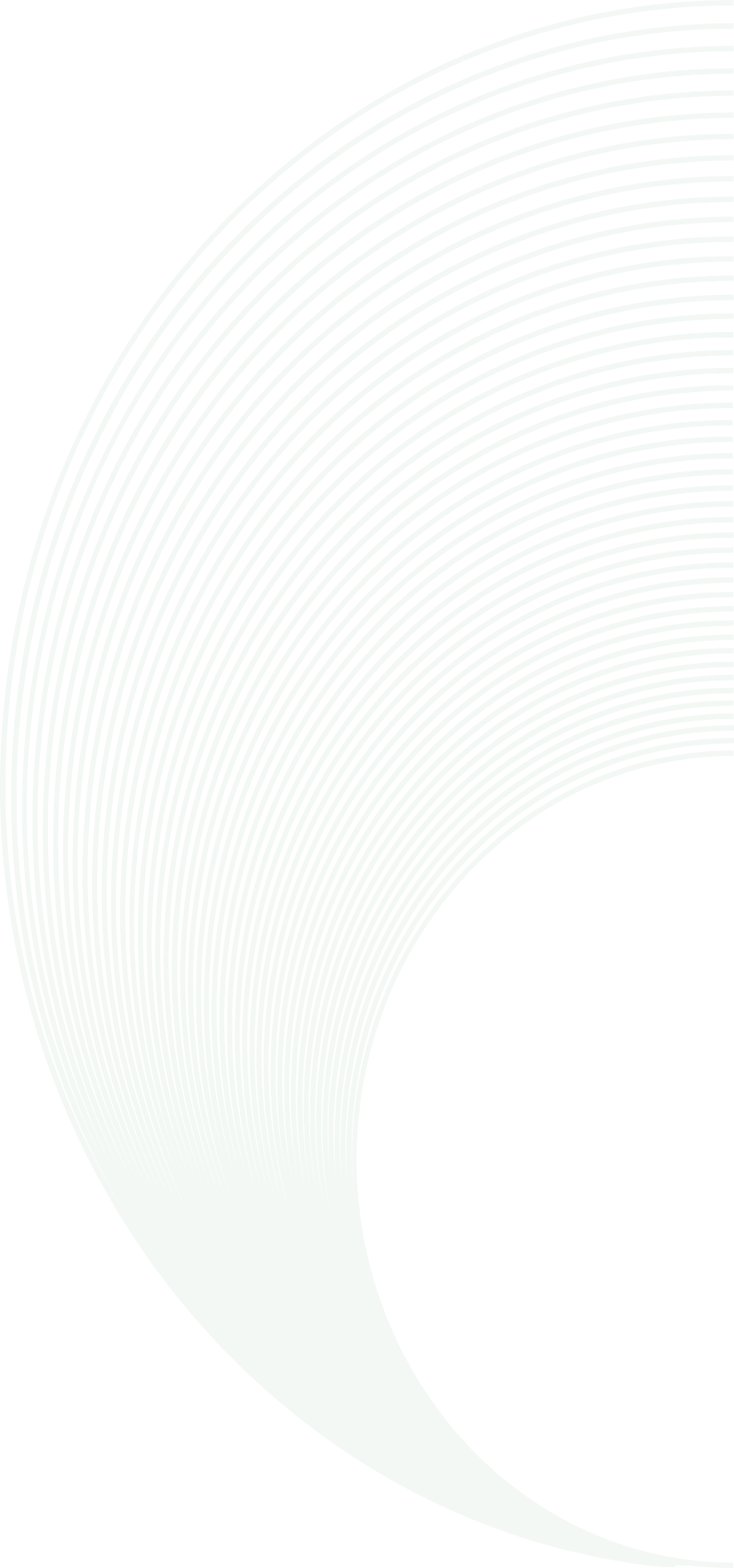
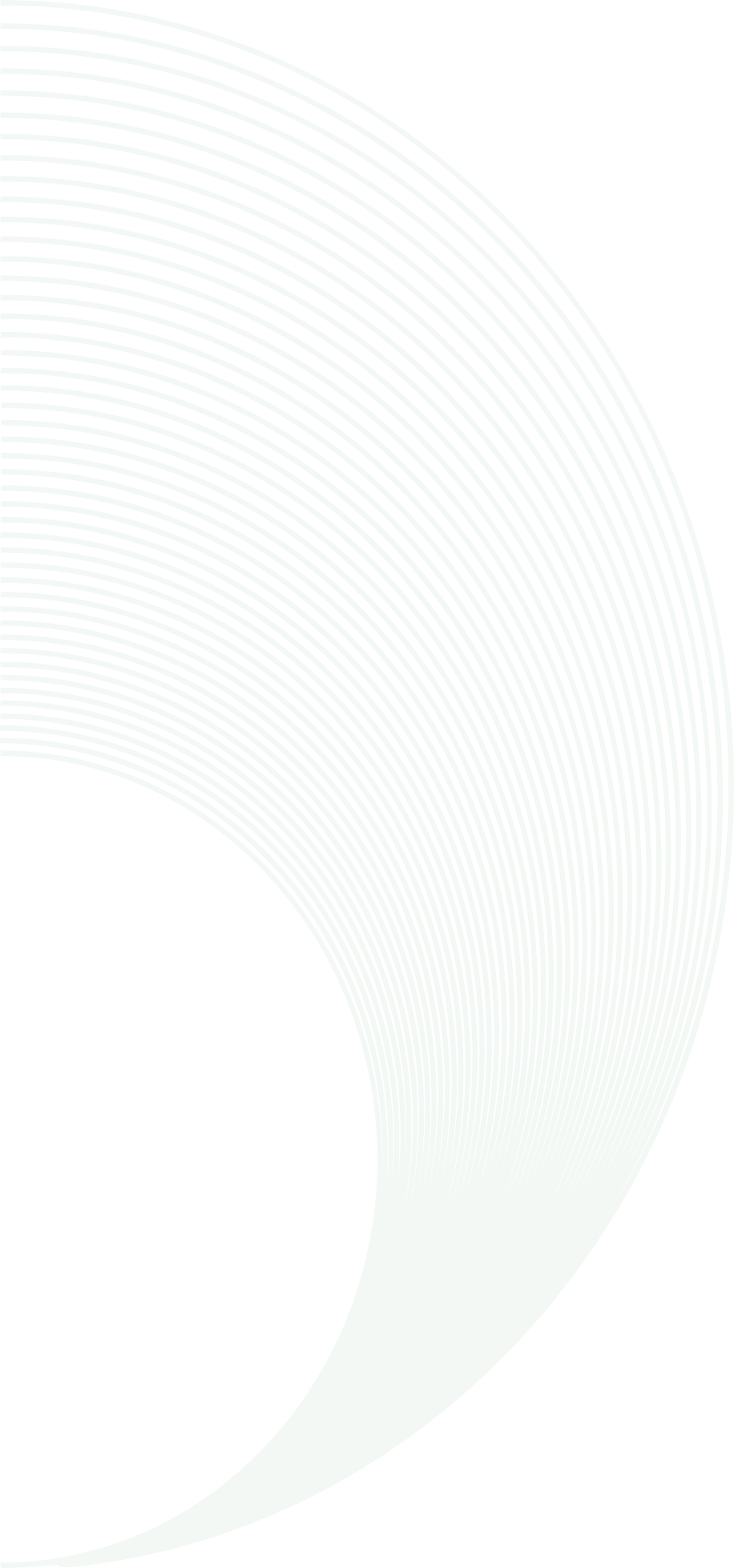
Efficiency in Motion: The Art of Warehouse Picking and Packing
In the bustling world of logistics, the efficiency of warehouse operations is a critical factor in the success of businesses across the globe. Picking and packing, two fundamental processes in warehouse management, play a pivotal role in ensuring that goods are delivered accurately and promptly to customers. This article delves into the intricacies of these essential tasks, exploring the methods, challenges, and innovations that define the art of warehouse picking and packing.
Picking: The Starting Point of Fulfillment
Picking refers to the process of selecting products from warehouse inventory to fulfill customer orders. It is the first step in the order fulfillment process and sets the tone for the efficiency of the entire supply chain. The goal is to pick the correct item in the right quantity as quickly as possible, minimizing errors and maximizing productivity.
Methods of Picking
There are several methods of picking, each suited to different types of warehouses and order profiles:
• Discrete Picking: The most straightforward method, where a picker collects items for one order at a time.
• Batch Picking: Involves picking items for multiple orders simultaneously to reduce travel time.
• Zone Picking: Pickers are assigned specific areas and pick items within their zones, passing them on to the next zone or to packing.
• Wave Picking: A combination of batch and zone picking, often coordinated with shipping schedules to optimize the flow of goods.
Challenges in Picking
Despite the variety of methods available, picking remains a challenging task due to factors such as:
• Inventory Accuracy: Discrepancies between physical stock and inventory records can lead to picking errors.
• Layout Optimization: An inefficient warehouse layout can increase travel time and reduce picking speed.
• SKU Proliferation: An increasing number of stock-keeping units (SKUs) can complicate the picking process.
Packing: The Final Checkpoint Before Dispatch
Packing is the process of placing picked items into boxes or containers for shipment. It involves verifying items against the order, securing them for transit, and labeling the package for delivery.
Best Practices in Packing
To ensure that the packing process is efficient and error-free, warehouses implement best practices such as:
• Quality Control: Checking items during packing to catch any picking errors.
• Right-Sizing: Using boxes that fit the items well to reduce material waste and shipping costs.
• Automation: Employing packing machines or robots to increase speed and consistency.
Innovations in Picking and Packing
Technological advancements have introduced innovations that are transforming picking and packing processes:
• Automated Guided Vehicles (AGVs): Robots that transport items between zones, reducing human travel time.
• Pick-to-Light Systems: Use lights to guide pickers to the correct locations, improving accuracy and speed.
• Voice Picking: Allows pickers to receive instructions via headset, keeping their hands and eyes free for the task.
• Packing Algorithms: Software that determines the most efficient way to pack items, considering dimensions and fragility.
The Human Element
Despite automation, the human element remains crucial in picking and packing. Skilled workers are needed to handle exceptions, perform quality checks, and oversee automated systems. Training and ergonomic considerations are vital to maintain a productive and healthy workforce.
Conclusion: The Heartbeat of the Warehouse
Picking and packing are more than just mundane tasks; they are the heartbeat of the warehouse, driving the rhythm of incoming and outgoing goods. As e-commerce continues to grow, the pressure on warehouses to perform these tasks quickly and accurately will only increase. Investing in the right methods, technologies, and workforce training is essential for businesses to stay competitive in the fast-paced world of logistics.
This article is intended to provide an overview of warehouse picking and packing. For those looking to implement or improve these processes, it is recommended to consult with logistics experts and consider the specific needs of your operation.