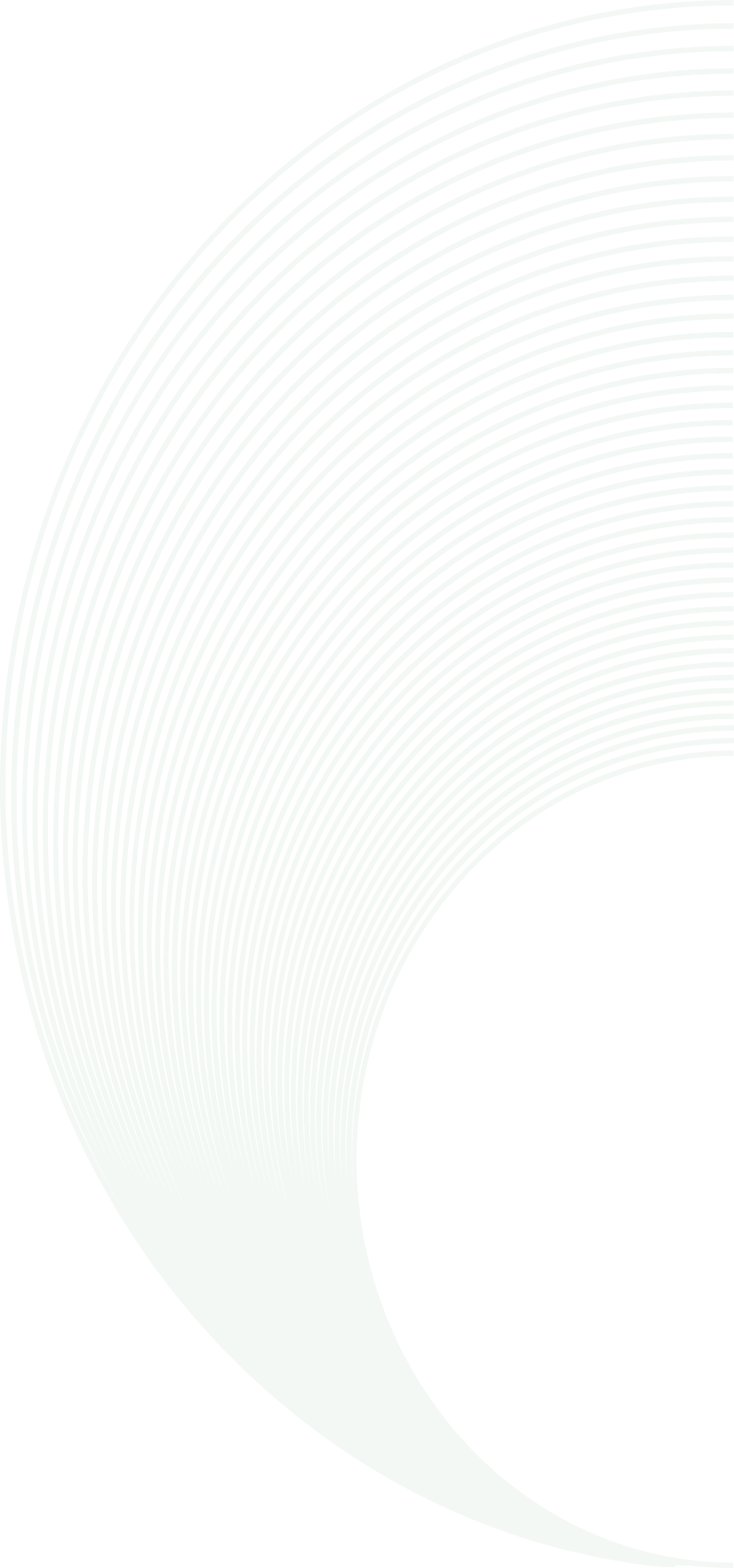
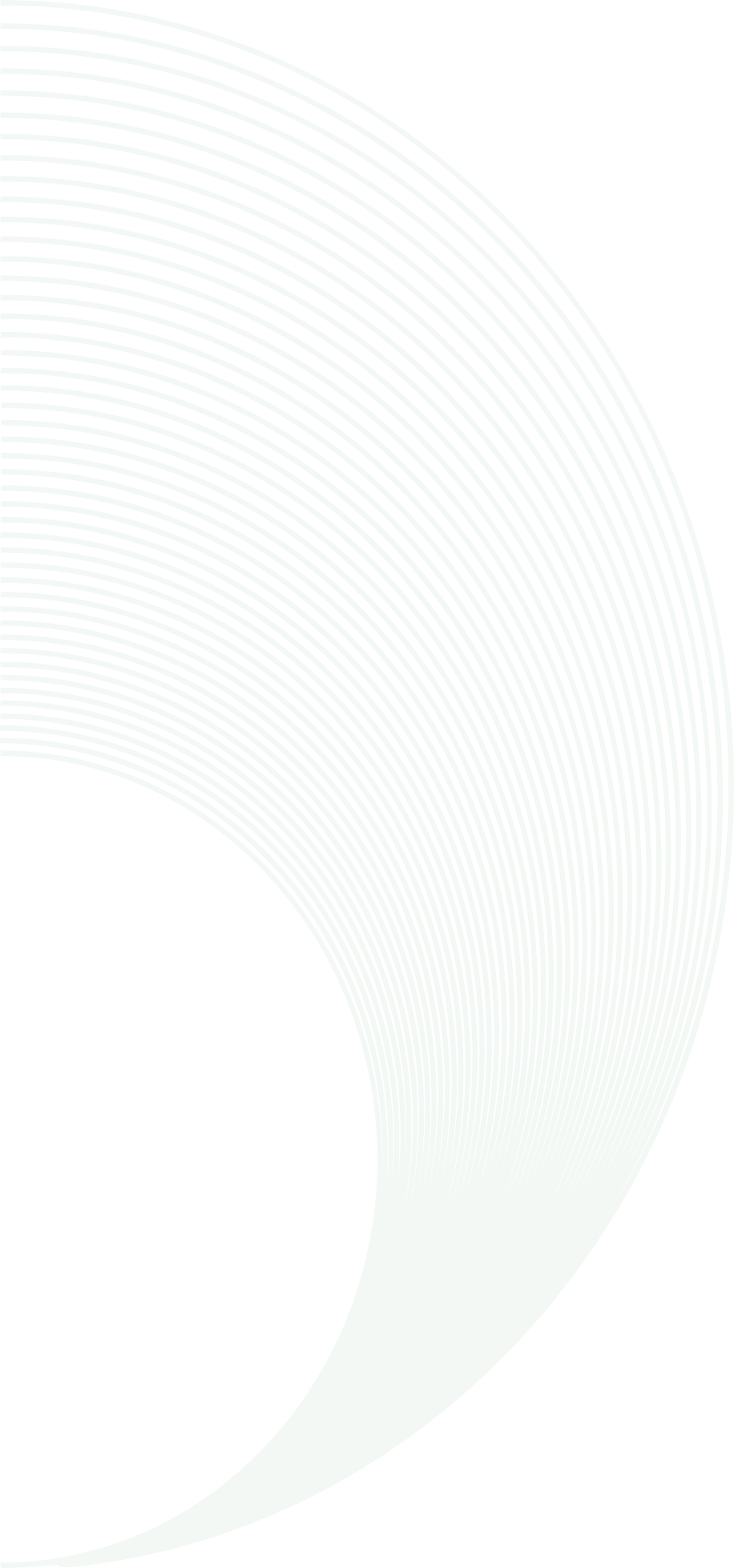
Glass Fibre Reinforced Plastic (GFRP) Rebars for Concrete Structures: A Sustainable Alternative in Construction
Concrete has been a foundational material in construction for centuries, but as the world moves toward sustainability, innovation within the industry is crucial. One of the most promising advancements in concrete reinforcement is the use of Glass Fibre Reinforced Plastic (GFRP) rebar. This material, which integrates glass fibers with a plastic resin, offers a durable and corrosion-resistant alternative to traditional steel rebar.
What is GFRP Rebar?
GFRP rebar is a composite material consisting of glass fibers embedded in a polymer resin, typically epoxy or vinyl ester.
The glass fibers provide the necessary tensile strength, while the resin acts as a binder, giving the rebar its shape and integrity. This type of rebar is non-corrosive, lightweight, and offers superior mechanical properties when compared to traditional steel reinforcement, making it ideal for a wide range of concrete structures.
The main appeal of GFRP rebar lies in its resistance to corrosion. Unlike steel, which is vulnerable to rust and degradation over time, especially in moist or saline environments, GFRP rebar is impervious to the corrosive effects of water, chemicals, and salts. This makes it an excellent choice for infrastructure projects exposed to extreme conditions, such as bridges, marine structures, and underground utilities.
Key Benefits of GFRP Rebars in Concrete Structures
Corrosion Resistance
One of the most significant advantages of GFRP rebar over traditional steel reinforcement is its corrosion resistance. Steel rebar can corrode when exposed to moisture, salt, and other environmental factors, leading to the deterioration of concrete structures over time. This corrosion can result in cracks, reduced load-bearing capacity, and ultimately, structural failure. GFRP rebar, on the other hand, is highly resistant to rust and chemical corrosion, ensuring a longer lifespan for concrete structures. This makes it particularly beneficial for applications in coastal regions, industrial plants, and bridges, where steel rebar might fail prematurely.
Lightweight and Easy to Handle
GFRP rebar is significantly lighter than steel, which makes handling, transportation, and installation easier and more cost-effective. A reduction in weight can lead to lower labor costs and faster installation times, contributing to overall project efficiency. The reduced weight also makes GFRP rebar a more accessible option for projects with weight restrictions or in locations where lifting equipment is not readily available.
Durability in Harsh Environments
Due to its non-corrosive nature, GFRP rebar outperforms steel in applications exposed to extreme weather, moisture, and chemicals. For example, in marine construction such as piers, docks, and seawalls, GFRP rebar helps mitigate the damaging effects of saltwater, which would normally accelerate the corrosion of steel reinforcement. Additionally, it’s highly resistant to other harsh chemicals such as chlorides and sulfates, which are commonly found in wastewater treatment plants, tunnels, and industrial facilities.
Non-Magnetic and Non-Conductive Properties
Another key benefit of GFRP rebar is its non-magnetic and non-conductive properties. This makes it an ideal choice for applications in sensitive environments such as hospitals, electronic manufacturing plants, and high-tech facilities, where electromagnetic interference (EMI) must be minimized. In these settings, GFRP rebar prevents the disruption of sensitive equipment and systems, which could be an issue with traditional steel rebar.
Sustainability and Environmental Impact
As the construction industry embraces green building practices, GFRP rebar offers a more sustainable solution. It is made from non-toxic materials, and its manufacturing process tends to have a lower environmental impact compared to steel production, which involves energy-intensive processes. Additionally, GFRP rebar can be recycled, contributing to a circular economy and reducing waste. The longevity of GFRP also means fewer repairs and replacements are needed, further reducing the environmental footprint of infrastructure projects.
Applications of GFRP Rebar in Concrete Structures
GFRP rebar is being increasingly utilized in a variety of concrete structures, thanks to its many benefits. Some of the key applications include:
Bridges and Overpasses
In bridge construction, GFRP rebar offers a durable, long-lasting solution for reinforcing the concrete deck and supporting structures. Its corrosion resistance ensures the integrity of the bridge over time, reducing maintenance costs and extending the lifespan of the structure.
Marine and Coastal Infrastructure
The marine environment is highly corrosive, especially when saltwater is involved. GFRP rebar is ideal for reinforcing piers, docks, and seawalls, where steel rebar would rapidly degrade. The corrosion resistance of GFRP rebar helps preserve the structure's durability even in the harshest coastal environments.
Parking Structures and Roads
Parking garages, which are often exposed to de-icing salts and water, benefit from the corrosion-resistant nature of GFRP rebar. Similarly, road construction in areas where corrosion from de-icing salts is a concern can see a significant improvement in the longevity of the infrastructure by using GFRP.
Wastewater Treatment Plants
Wastewater treatment plants are typically exposed to chemicals and moist conditions, making them prime candidates for GFRP rebar. The non-corrosive properties of GFRP help ensure that the structural integrity of concrete tanks and treatment basins is maintained, even in harsh chemical environments.
Tunnels and Underground Structures
The use of GFRP rebar in tunnels and underground structures helps to avoid the costly maintenance and repair issues that typically arise from corrosion in steel reinforcement. GFRP's ability to withstand moisture and chemical exposure makes it a highly effective solution for subterranean environments.
Challenges and Considerations
While GFRP rebar offers numerous advantages, it is important to consider a few potential challenges before making the switch from steel reinforcement:
Higher Initial Cost
GFRP rebar tends to have a higher initial cost compared to traditional steel rebar. However, its longer lifespan and reduced maintenance needs can result in overall cost savings in the long run, especially for structures exposed to harsh environments.
Limited Availability
Although GFRP rebar is gaining popularity, it may not yet be as widely available as steel rebar in some regions, including certain parts of Mexico. It is important for construction companies to ensure a reliable supply chain for GFRP materials when planning large-scale projects.
Bending and Handling
While GFRP rebar is lightweight, it is also more brittle than steel and may require more careful handling during installation to prevent breakage. Special equipment or additional care may be needed to bend or shape the rebar according to the design specifications.
Conclusion
Glass Fibre Reinforced Plastic (GFRP) rebar is rapidly becoming a preferred choice for concrete reinforcement, offering numerous benefits such as corrosion resistance, durability, and sustainability. As infrastructure projects continue to evolve and demand more efficient, long-lasting solutions, GFRP rebar presents an innovative alternative to traditional steel reinforcement. Its versatility makes it suitable for a wide range of applications, from marine structures to underground facilities, providing a reliable and cost-effective solution for the challenges of modern construction.
As the construction industry in Mexico and around the world moves toward more sustainable practices, GFRP rebar is poised to play a significant role in the future of concrete structures, offering enhanced performance, longer lifespans, and reduced maintenance costs.