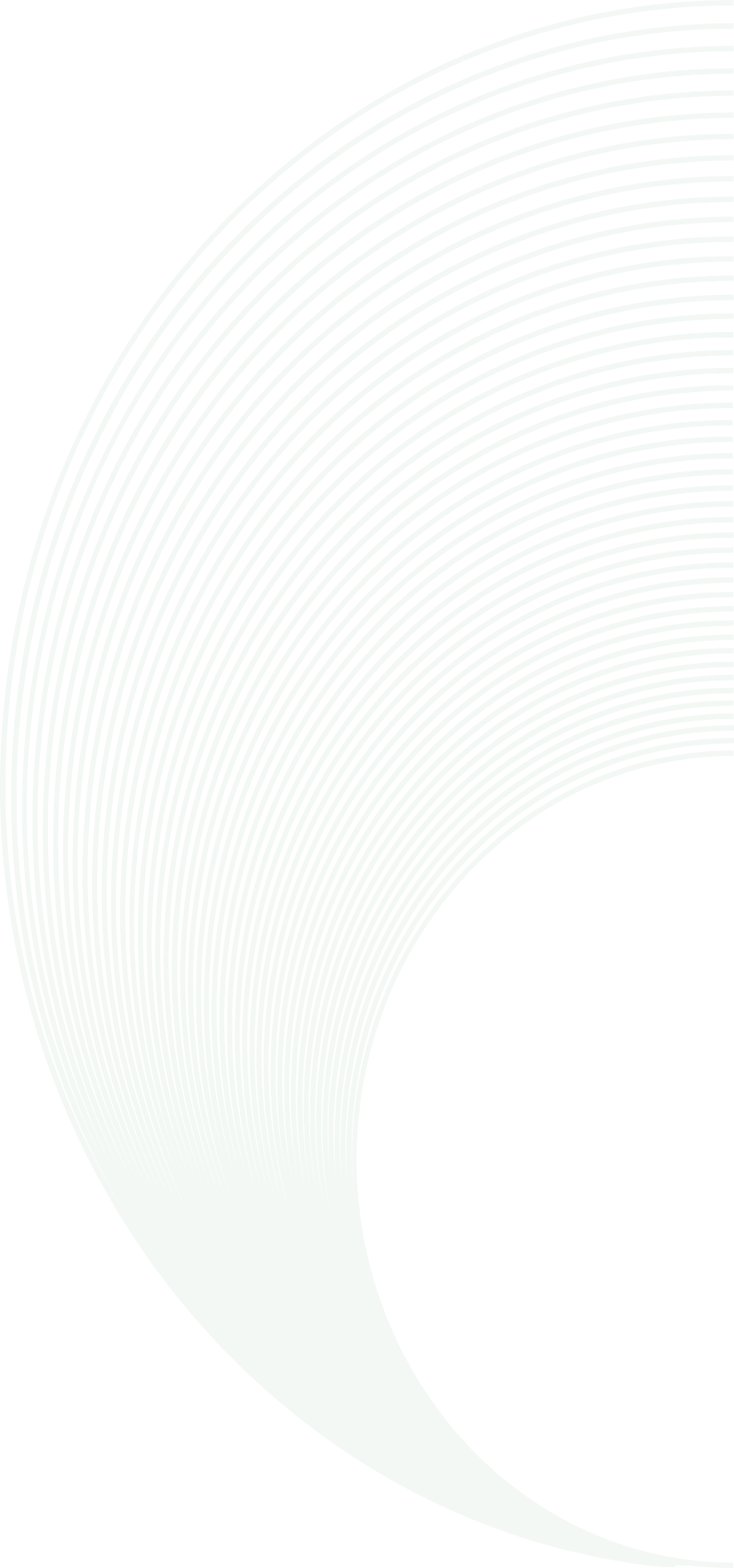
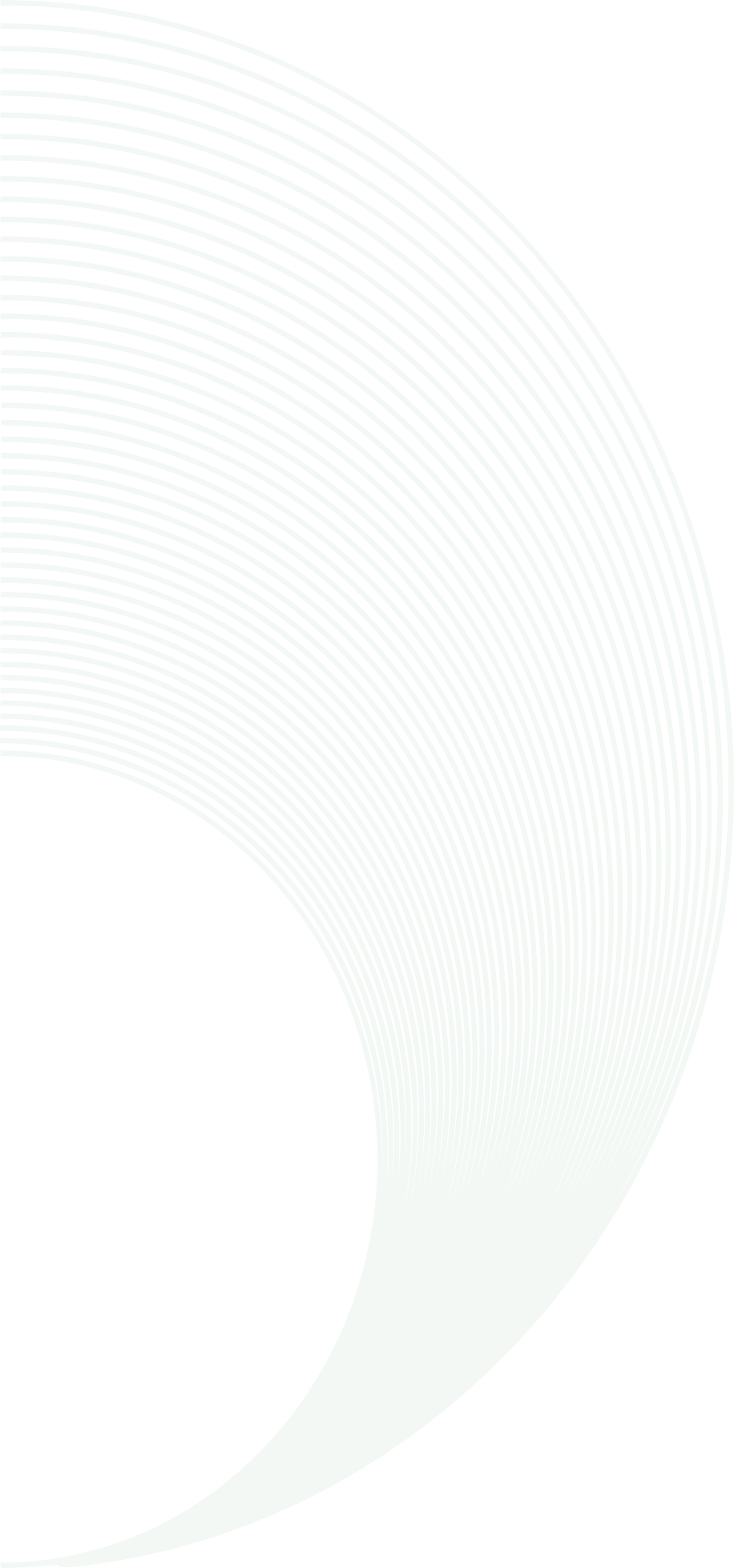
Human Machine Interfaces for Process Industries: Enhancing Control and Efficiency
In process industries, the need for seamless interaction between operators and complex machinery is crucial for ensuring safety, efficiency, and productivity. Human Machine Interfaces (HMIs) serve as the bridge between human operators and automated systems, allowing for effective control, monitoring, and management of industrial processes.
What is a Human Machine Interface (HMI)?
A Human Machine Interface (HMI) is a system that allows human operators to interact with machines, equipment, or processes.
In the context of process industries, HMIs provide visual representations of processes, systems, and data, enabling operators to monitor and control operations in real time. HMIs typically display data, status indicators, alarms, and controls that help operators make informed decisions and take corrective actions when needed.
Key Features of HMIs in Process Industries
Real-Time Data Visualization
One of the core functions of an HMI is to provide real-time visualization of the process or system it is monitoring. Whether it’s the temperature, pressure, flow rate, or other critical parameters, the HMI allows operators to view current data and trends at a glance. Interactive graphical displays, charts, and gauges make complex data easier to interpret.
Alarm Management
HMIs are equipped with alarm management features that notify operators of process anomalies, such as exceeding preset thresholds or equipment failures. The alarm system provides visual, auditory, and sometimes even remote notifications, ensuring that operators can respond promptly to prevent accidents or system malfunctions.
Control and Automation
HMIs offer control functionality, allowing operators to start, stop, or adjust equipment settings. In more advanced systems, HMIs can integrate with automated control systems (e.g., Distributed Control Systems (DCS) or Programmable Logic Controllers (PLC)), enabling autonomous operations based on pre-defined parameters.
Data Logging and Reporting
HMIs can log data for later analysis, providing historical records of system performance, alarms, and events. This data can be used for troubleshooting, performance evaluation, regulatory compliance, and long-term process optimization. Reports can be automatically generated and exported to a centralized system for further analysis.
Touchscreen Interface
Modern HMIs often utilize touchscreen interfaces, which allow operators to quickly interact with systems using gestures such as tapping, swiping, or dragging. This provides a more intuitive and user-friendly way of managing complex industrial processes compared to traditional physical buttons or switches.
Remote Access and Control
Many HMIs today are equipped with remote access capabilities, allowing operators and engineers to monitor and control systems from distant locations. This is particularly useful for systems that span large geographical areas or require offsite monitoring for 24/7 operations.
Types of HMIs in Process Industries
Desktop HMIs
These are typically used in control rooms and offices. They offer a large display screen, allowing operators to monitor and control several parameters at once. Desktop HMIs are ideal for systems that require a more detailed, multi-window view of the data.
Panel-Mount HMIs
Panel-mount HMIs are installed directly onto equipment panels or control stations. These are commonly used in industrial settings where a more compact form factor is necessary. They provide essential control and monitoring functions in a rugged, space-saving design.
Portable HMIs
Portable HMIs are handheld devices that allow operators to monitor and control systems while moving around the plant floor. These HMIs are useful for maintenance teams or operations staff who need to make adjustments or check system status at various points in a facility.
Mobile HMIs
With the growing trend of mobile devices, some HMIs now offer mobile versions that can run on smartphones or tablets. These devices offer flexibility and portability, enabling remote monitoring and control of systems while away from the control room.
Applications of HMIs in Process Industries
Oil and Gas Industry
In the oil and gas industry, HMIs are used to monitor drilling operations, pipeline pressures, and refinery processes. Operators rely on real-time data visualization to ensure the safe and efficient extraction, transportation, and refining of oil and gas products.
Chemical Manufacturing
HMIs play a critical role in controlling chemical reactions, monitoring hazardous material levels, and ensuring compliance with safety standards. By providing real-time monitoring of temperature, pressure, and flow rates, HMIs help prevent accidents and optimize chemical production.
Pharmaceutical Industry
In the pharmaceutical industry, HMIs are used to manage production lines, monitor environmental conditions in cleanrooms, and ensure adherence to stringent regulations. HMIs allow operators to oversee equipment performance and product quality, while minimizing the risk of contamination.
Food and Beverage Processing
In food processing plants, HMIs provide control over temperature, humidity, and processing time, ensuring consistent product quality. They also help operators comply with food safety regulations by tracking critical parameters in real-time.
Power Generation
HMIs are essential for monitoring and controlling power generation systems, including turbines, boilers, and generators. They allow operators to track system efficiency, monitor fuel consumption, and ensure the safety of the plant.
Advantages of Using HMIs in Process Industries
Improved Efficiency
HMIs provide a centralized view of multiple systems, allowing operators to quickly identify issues and optimize performance. This leads to more efficient operation and reduced downtime.
Enhanced Safety
By providing real-time data and alarms, HMIs help prevent hazardous situations, allowing operators to take corrective actions before accidents occur. HMIs also offer safety interlocks and emergency shutdown features in case of critical failures.
Ease of Operation
With user-friendly graphical interfaces and touch controls, HMIs reduce the complexity of operating advanced process systems. This helps operators make faster, more accurate decisions, reducing human error.
Remote Monitoring and Control
Remote capabilities enable engineers and operators to monitor and manage systems from anywhere, reducing the need for on-site presence and ensuring continuous system oversight, even in remote locations.
Data Integration
HMIs can be integrated with other industrial systems like SCADA (Supervisory Control and Data Acquisition), DCS, and PLCs, enabling seamless data flow and analysis across the entire operation.
Challenges and Considerations
While HMIs offer many benefits, they also present challenges such as:
- Complexity in Integration: Integrating HMIs with legacy systems and equipment can sometimes be challenging and may require specialized expertise.
- Cybersecurity: With remote access and internet connectivity, securing HMIs from cyber threats is essential to protect sensitive industrial systems.
- User Training: Operators need adequate training to use HMIs effectively, especially in complex industrial environments with multiple variables to track.
Conclusion
Human Machine Interfaces are an indispensable component of modern process industries, providing operators with the tools they need to monitor, control, and optimize complex systems. The benefits of HMIs—such as improved efficiency, safety, and remote monitoring—make them critical for industries ranging from chemical manufacturing to power generation. By enhancing communication between operators and machinery, HMIs help ensure smooth and safe operations, leading to increased productivity and minimized risk.