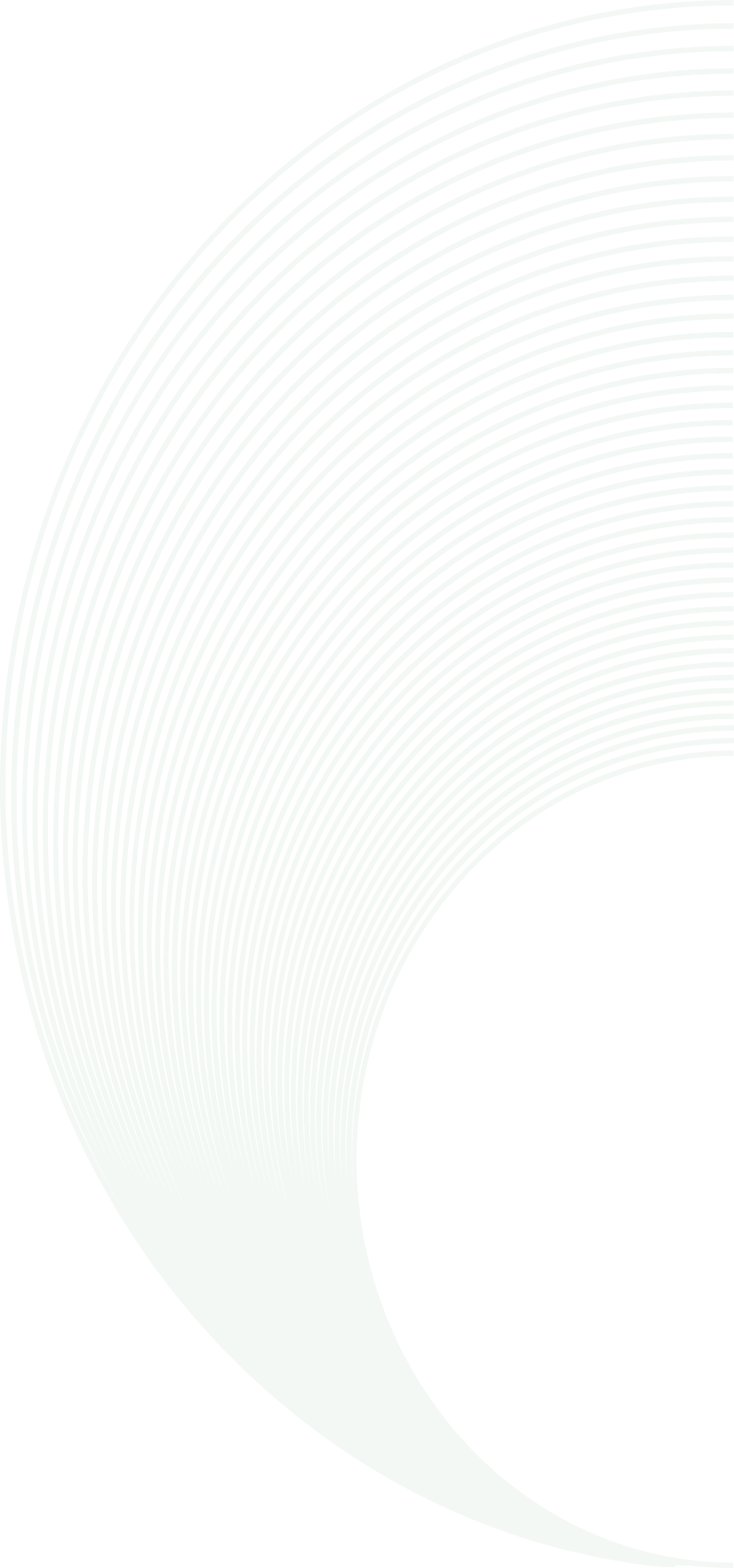
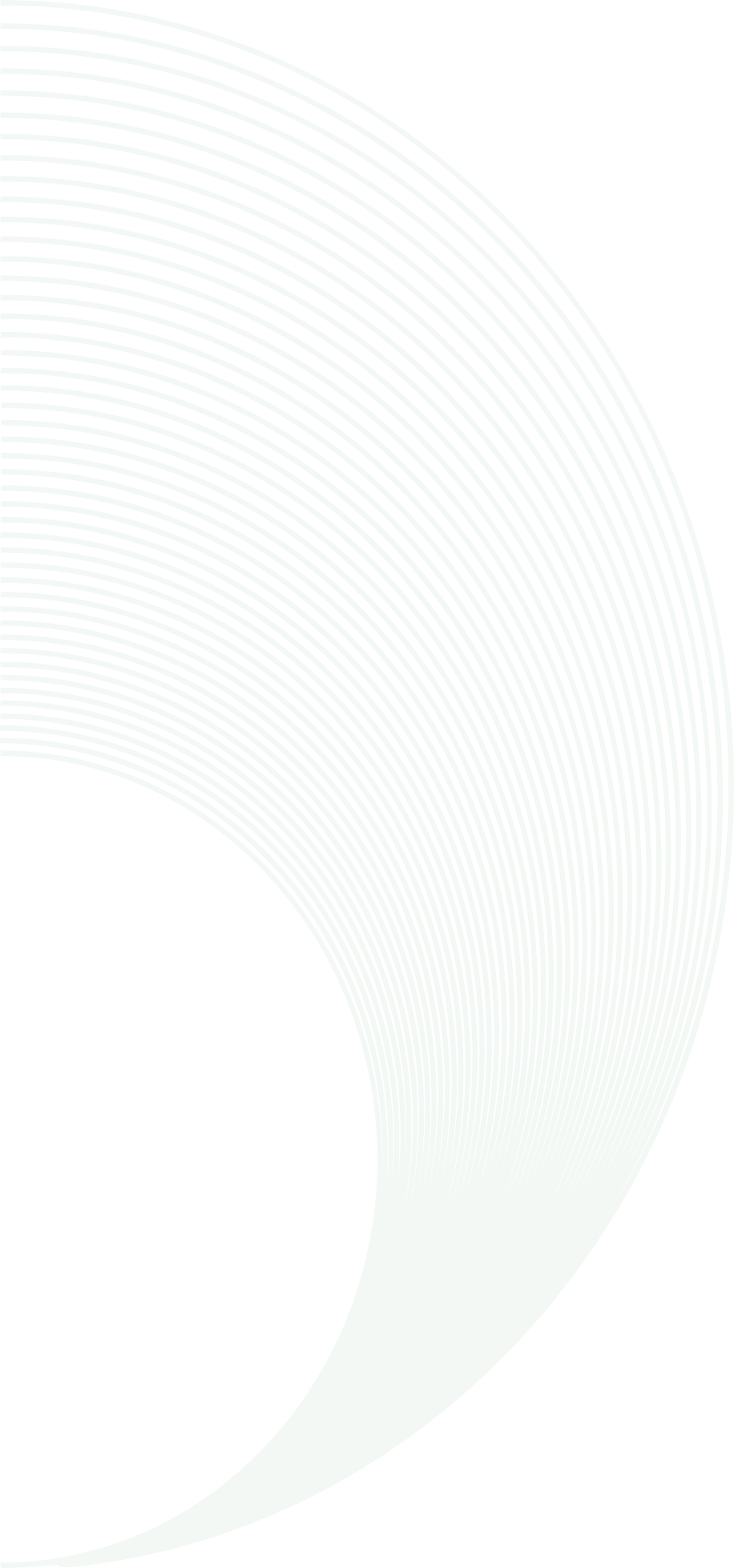
Image Dimension Measurement System: Revolutionizing Precision and Accuracy
Image dimension measurement systems play a crucial role in a wide range of industries, from manufacturing and quality control to medical imaging and scientific research. These systems use advanced image processing technologies to measure the physical dimensions of objects accurately, based on digital images or video streams. Whether in automated production lines or in precision engineering applications, image dimension measurement systems are designed to enhance accuracy, efficiency, and productivity.
What is an Image Dimension Measurement System?
An image dimension measurement system uses high-resolution cameras and advanced software to capture and analyze digital images of an object.
The system then processes the captured data to measure specific dimensions such as length, width, height, angles, and other geometrical features of the object. These systems are used for quality inspection, process control, and various research applications that require precise measurements without physical contact with the object.
Key Components of Image Dimension Measurement Systems
High-Resolution Cameras
At the core of the measurement system is the camera or cameras that capture high-resolution images of the object. These cameras are often coupled with optical systems such as lenses or microscopes to achieve the required level of detail. High-resolution cameras allow for the accurate detection of edges, contours, and surface features necessary for precise measurements.
Lighting Systems
Proper lighting is critical in image dimension measurement. The lighting system illuminates the object in a way that enhances its visible features and contrasts, making edges and boundaries more defined. Different lighting techniques such as diffuse, ring, or backlighting are used depending on the application and the nature of the object being measured.
Software Algorithms
The image captured by the camera is processed using sophisticated image processing software. These algorithms analyze the pixel data and extract meaningful information such as the dimensions, surface area, or other geometric properties of the object. Machine learning algorithms and edge detection methods are often applied to improve accuracy, even in challenging conditions such as low-contrast images or irregular object shapes.
Calibration Tools
To ensure the measurements are accurate, the system requires calibration. Calibration tools, which include reference objects with known dimensions, allow the system to adjust and correct any distortions or errors in the captured images. This step ensures that the measurements reflect the true physical dimensions of the object.
Display and User Interface
The measured data is displayed on a user interface that allows operators to easily interpret the results. The interface may also include visual aids, such as graphical representations of the object’s measurements, comparison charts, and historical data for tracking changes over time. The user interface is typically customizable to suit the specific needs of the application.
Types of Image Dimension Measurement Systems
2D Image Dimension Measurement Systems
These systems use a single camera or multiple cameras arranged to capture a flat, two-dimensional image of an object. The system analyzes the image for lengths, widths, and other 2D features. 2D systems are often used for simpler applications where depth is not a critical factor, such as measuring printed circuit boards (PCBs) or flat objects like film or sheets.
3D Image Dimension Measurement Systems
In contrast, 3D systems use stereo vision or laser triangulation to capture three-dimensional data of an object. These systems are more advanced and can measure the volume, height, depth, and contours of an object. 3D systems are used in industries such as automotive manufacturing, aerospace, and biomedical applications, where more complex measurements are required.
Inline and Offline Measurement Systems
Inline measurement systems are integrated directly into production lines and perform real-time measurement as objects pass through. These systems are often used in automated quality control and process monitoring. Offline measurement systems, on the other hand, are used for post-production analysis and typically involve more detailed measurements of sampled objects or batches.
Applications of Image Dimension Measurement Systems
Quality Control and Inspection
Image dimension measurement systems are widely used in quality control in manufacturing. For instance, in the automotive industry, these systems can measure the dimensions of parts such as engine components or car body panels to ensure they meet design specifications. In electronics, PCB assembly lines use these systems to inspect the size and alignment of components.
Medical Imaging
In medical imaging, image dimension measurement systems are essential for analyzing images such as CT scans, MRIs, and X-rays. They can measure the dimensions of organs, tumors, or bones, aiding in diagnosis, treatment planning, and post-treatment evaluation.
Precision Engineering
In industries like aerospace and defense, where precision is critical, image dimension measurement systems are used to measure the fine details of intricate parts. These measurements ensure that components meet strict tolerances and perform as required in high-performance environments.
Research and Development
In scientific research, accurate measurement of specimens and experimental setups is often required. Image dimension measurement systems are used to analyze biological samples, materials, and components in various research fields, including biology, physics, and chemistry.
Textile and Fabric Industry
In textile production, these systems measure the dimensions of fabrics, ensuring uniformity in textile manufacturing processes. They help in checking fabric length, width, and surface quality, improving overall production quality.
Advantages of Image Dimension Measurement Systems
Non-Contact Measurement
Image dimension measurement systems provide non-contact measurements, eliminating the risk of damaging delicate or sensitive materials during measurement. This is especially important in industries like electronics and medical devices.
High Speed and Efficiency
These systems can perform measurements in real-time, making them ideal for use in automated production lines where speed is crucial. Their ability to process large volumes of data quickly improves production efficiency and reduces human errors in manual measurements.
Enhanced Accuracy
With high-resolution imaging and advanced software algorithms, these systems offer high levels of accuracy, often down to micrometers or smaller. This makes them ideal for precision applications where even minor discrepancies can lead to major problems.
Flexibility and Adaptability
Image dimension measurement systems are highly adaptable, able to measure a wide range of object shapes, sizes, and materials. Whether dealing with flat, round, or complex 3D objects, these systems can be configured to handle different measurement tasks.
Challenges and Considerations
- Lighting and Environmental Factors: The effectiveness of an image dimension measurement system can be influenced by environmental factors, such as lighting conditions, dust, or vibration. Proper environmental control is essential for accurate results.
- Calibration and Maintenance: Regular calibration is required to ensure that measurements remain accurate over time. This adds an additional layer of complexity to the system's operation.
- Software Complexity: Advanced image processing software can be complex, requiring skilled personnel to operate and maintain the system properly.
Conclusion
Image dimension measurement systems are a cornerstone of modern industrial measurement and inspection processes. They provide high accuracy, speed, and non-contact functionality that are essential in a wide variety of applications, from quality control in manufacturing to precision measurements in research. With advancements in imaging technology and software algorithms, these systems are becoming increasingly versatile and capable of meeting the demands of industries that require the highest levels of precision.