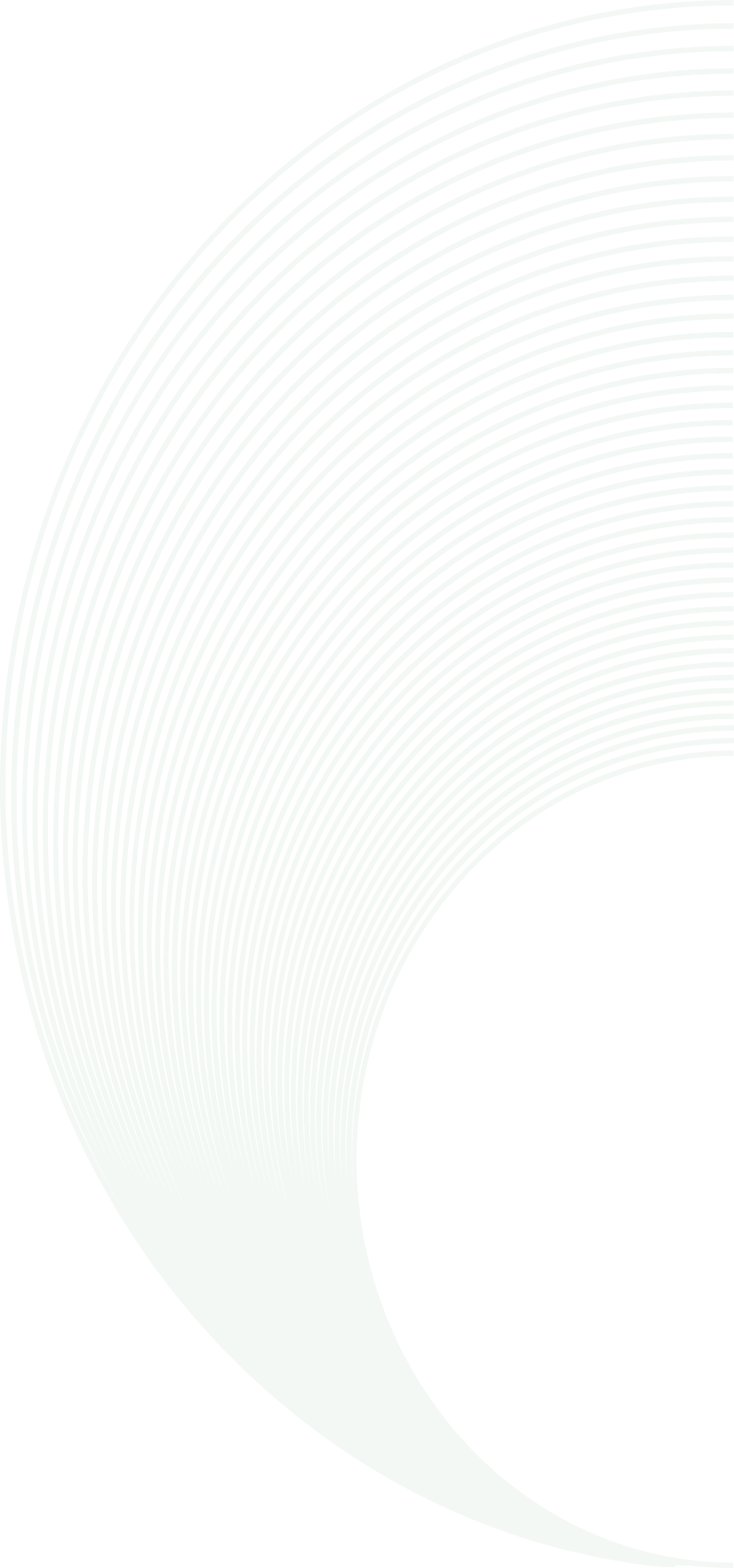
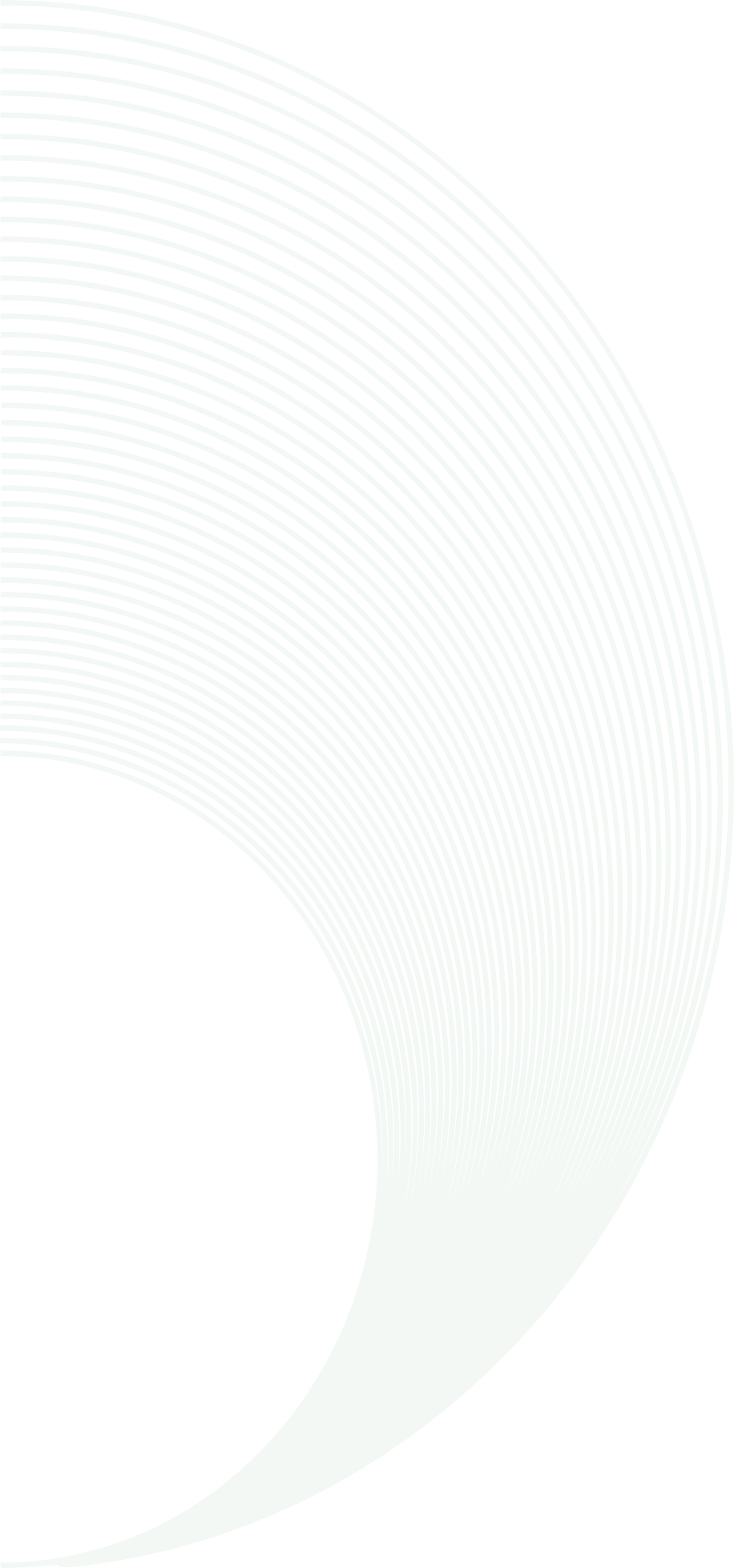
Industrial Robotic Arm Solutions Providers: Enhancing Efficiency in Manufacturing
The rise of automation and smart manufacturing has led to increased demand for industrial robotic arm solutions, which play a critical role in improving productivity, precision, and safety in various industries. Industrial robotic arms are used in applications ranging from assembly and material handling to welding and packaging. As businesses strive to optimize their production processes, finding the right provider for industrial robotic arm solutions is essential.
Key Benefits of Industrial Robotic Arms
Increased Productivity: Robotic arms can work 24/7, significantly increasing output and reducing the need for human labor in repetitive tasks. This constant operation translates to faster production cycles, allowing companies to meet demand more effectively.
Enhanced Precision and Quality: Equipped with sophisticated sensors and programmable controllers, robotic arms execute tasks with high accuracy, reducing errors and ensuring consistency in production quality.
Improved Safety: Industrial robotic arms can handle hazardous tasks, reducing human exposure to dangerous environments or materials. This benefit is particularly valuable in industries like metalworking, chemical production, and manufacturing.
Flexibility: Modern robotic arms can be reprogrammed and reconfigured to handle multiple tasks, making them ideal for industries that require adaptability. Their ability to perform diverse functions provides flexibility to adjust production lines according to changing needs.
Cost-Effectiveness: While robotic arm solutions require upfront investment, they often deliver a high ROI by reducing labor costs, minimizing waste, and enhancing operational efficiency over time.
Top Industrial Robotic Arm Solution Providers
Several companies are at the forefront of providing advanced industrial robotic arm solutions. These providers offer a range of options tailored to different industries and applications:
Fanuc Corporation: Fanuc is one of the world’s largest robotics companies, specializing in automation products and robotic arms used in manufacturing, automotive, and electronics industries. Fanuc offers a range of robotic arms with customizable options for payload, reach, and precision.
ABB Robotics: Known for its innovation in automation and robotics, ABB provides robotic arm solutions that serve applications like assembly, packaging, welding, and material handling. ABB’s robots are compatible with advanced software solutions, enabling high flexibility and integration into existing systems.
KUKA Robotics: Based in Germany, KUKA is renowned for its robotic solutions in industries like automotive, healthcare, and electronics. KUKA’s robotic arms come with easy-to-use control interfaces and are available in various payload capacities, making them adaptable for different manufacturing tasks.
Yaskawa Motoman: Yaskawa offers a wide range of robotic arms, from compact models for precise tasks to heavy-duty arms for material handling. Their solutions are popular in industries like pharmaceuticals, food and beverage, and metalworking.
Universal Robots: Universal Robots focuses on collaborative robotic arms, also known as cobots, which work safely alongside human workers. These cobots are user-friendly, compact, and adaptable, making them ideal for small to medium-sized enterprises seeking affordable automation.
Factors to Consider When Choosing an Industrial Robotic Arm Solution Provider
Selecting the right provider is crucial to achieving a seamless integration of robotic arms into your operations. Here are some key considerations:
Customization Options: Look for providers who offer flexible configurations that match your specific production requirements. Customization options include payload capacity, speed, precision, and reach.
Software Integration: Modern industrial robotic arms are compatible with software solutions that allow remote monitoring, programming, and performance tracking. Providers offering robust software compatibility can enhance your system’s functionality and flexibility.
Customer Support and Training: Industrial robotic arms require installation, programming, and maintenance. Providers that offer comprehensive training, technical support, and maintenance services are valuable partners for long-term productivity.
Safety Features: If your operation involves human-robot collaboration, prioritize providers that focus on safety features, such as collision detection and emergency stop functions.
Cost and ROI: Budget constraints are always a factor. Compare providers not only on price but also on expected ROI, factoring in aspects like productivity gains, maintenance requirements, and ease of reprogramming for different tasks.
Applications of Industrial Robotic Arms Across Industries
Automotive Manufacturing: Robotic arms are widely used in automotive manufacturing for tasks like welding, painting, assembly, and quality inspection. High precision and the ability to handle repetitive tasks make them indispensable for large-scale production.
Electronics and Semiconductor: Due to the need for precision, robotic arms are used in electronics manufacturing to assemble and test products such as circuit boards and microchips. They enable quick, precise handling of delicate components, reducing human error.
Food and Beverage: Robotic arms in the food industry perform tasks such as sorting, packing, and palletizing. Providers like ABB and Yaskawa have solutions tailored to meet hygiene and safety standards specific to food handling.
Healthcare and Pharmaceuticals: Robotic arms assist in laboratory automation, medication dispensing, and surgical applications, offering accuracy and reliability. Companies like Universal Robots provide collaborative solutions suitable for lab environments.
Metalworking and Machining: Heavy-duty robotic arms are used for machining, welding, and handling metal parts. Providers like Fanuc and KUKA specialize in robotic arms designed to handle heavy materials and operate in challenging environments.
Future Trends in Industrial Robotic Arms
The field of industrial robotics is rapidly evolving with advancements in artificial intelligence, machine learning, and IoT integration. These trends enable robotic arms to perform complex tasks autonomously and adapt to changing production needs:
AI-Driven Automation: With AI, robotic arms can be programmed to learn and improve over time, enhancing efficiency and reducing the need for reprogramming.
Collaborative Robotics (Cobots): Collaborative robots, or cobots, are expected to grow as more industries adopt human-robot collaboration, allowing companies of all sizes to benefit from automation.
Predictive Maintenance: Integrating IoT sensors enables real-time monitoring, which can help in predictive maintenance, preventing downtime and optimizing productivity.
In conclusion, industrial robotic arm solutions are revolutionizing modern manufacturing by enhancing precision, productivity, and safety. By choosing the right provider and considering your unique operational needs, you can effectively integrate these robotic solutions into your business to achieve a competitive edge in today’s industrial landscape.