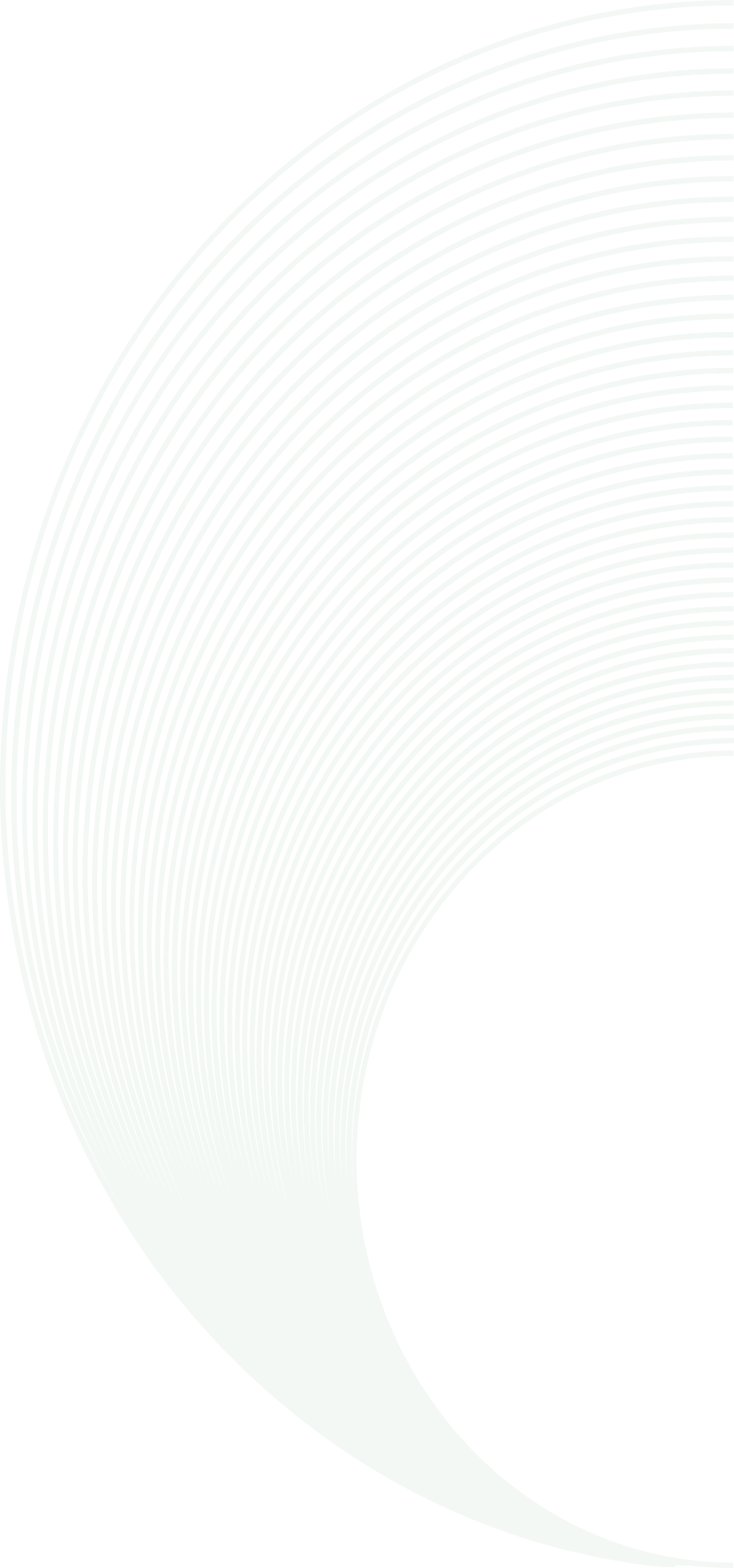
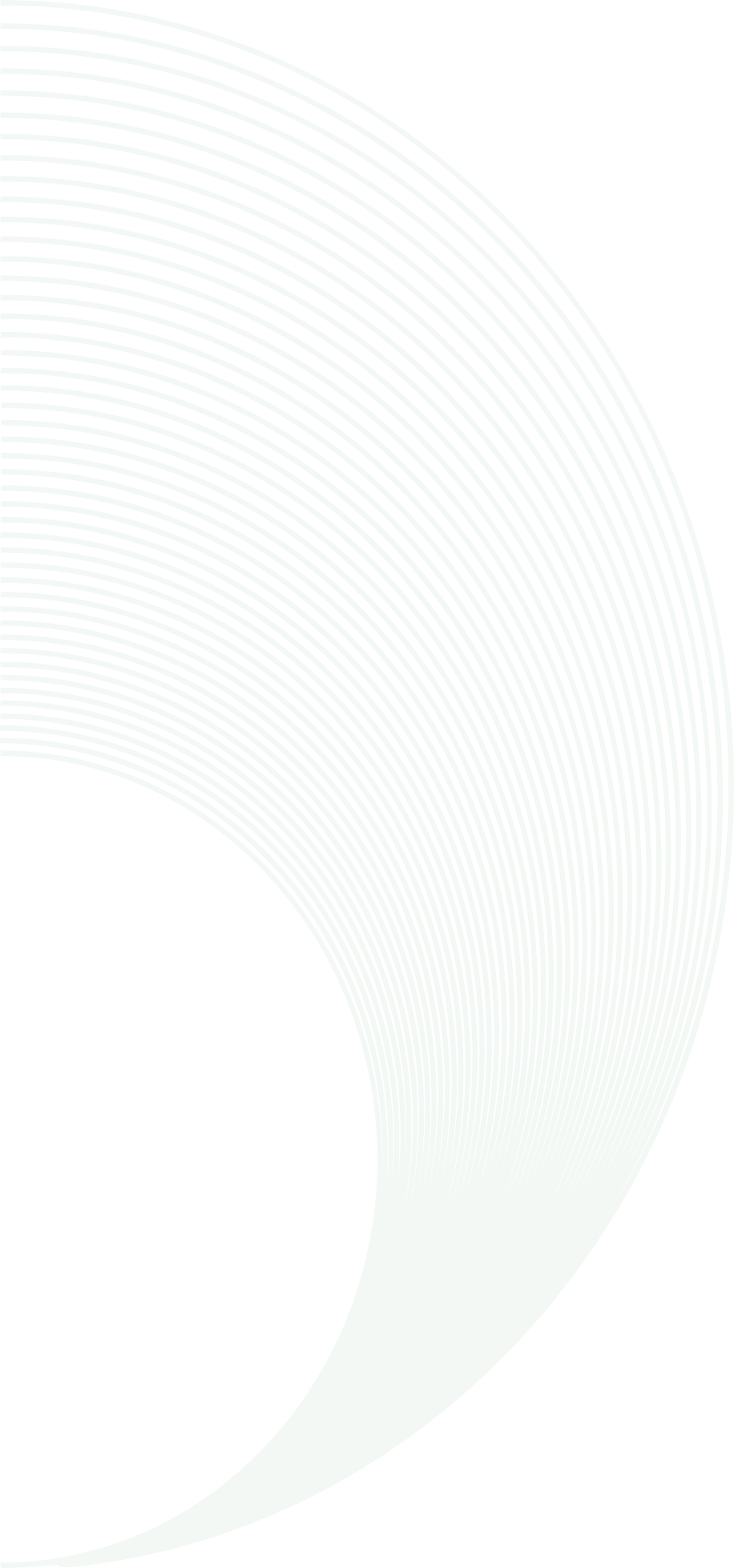
Industrial Vibration Analysis: Navigating the Complexities of Machinery Health
In the realm of industrial maintenance, vibration analysis stands as a sentinel against the unforeseen breakdowns that can cripple production lines and inflate operational costs. This article delves into the intricacies of industrial vibration analysis, a field that combines the precision of science with the foresight of experience to safeguard machinery health.
The Pulse of Industry: Understanding Vibration Analysis
At its core, vibration analysis is the science of monitoring and interpreting the vibration signatures emitted by industrial machinery. These vibrations, often imperceptible to the human touch, carry within them the story of a machine's condition. By meticulously analyzing these vibrations, specialists can predict failures, plan maintenance, and prevent costly downtime.
Vibration Analysis: The Diagnostic Tool
Just as a doctor uses a stethoscope to listen to a patient's heartbeat, vibration analysts use sophisticated equipment to listen to the 'heartbeat' of machines. Sensors placed on critical components detect vibrations that are then translated into data. This data is scrutinized for patterns that signify normal operation or warn of potential issues.
Decoding the Vibrations
The process of vibration analysis is a complex one, involving several steps:
• Data Collection: Using accelerometers and other sensors, vibration data is collected in real-time from machinery.
• Signal Processing: The raw data is processed to filter out noise and enhance the signals that are indicative of the machine's health.
• Analysis: Specialists analyze the processed data, looking for tell-tale signs of wear, imbalance, misalignment, or lubrication issues.
• Reporting: Detailed reports are generated, highlighting any concerns and recommending actions to prevent failure.
The Cost of Neglect: Why Vibration Analysis Matters
Ignoring the subtle signs of wear and tear can lead to catastrophic machine failures. Vibration analysis serves as a preemptive strike against such scenarios. It allows for:
• Predictive Maintenance: Scheduling maintenance based on actual machine condition rather than arbitrary timelines.
• Cost Savings: Reducing unexpected breakdowns and extending the life of equipment.
• Safety: Ensuring the safety of personnel by preventing accidents related to equipment failure.
• Efficiency: Keeping machines running at peak efficiency, thus optimizing production.
Vibration Analysis in Practice
Implementing a vibration analysis program involves:
• Training: Personnel must be trained to use analysis equipment and interpret data.
• Equipment: Investment in high-quality sensors and analysis software.
• Integration: Incorporating vibration analysis into regular maintenance routines.
Challenges and Solutions
While vibration analysis is invaluable, it is not without challenges. It requires skilled analysts, investment in equipment, and a culture that values preventive maintenance. Solutions include:
• Certification Programs: Ensuring analysts are trained and certified.
• Technology Adoption: Utilizing the latest in sensor and software technology.
• Management Buy-In: Gaining the support of management for a preventive maintenance program.
The Future of Vibration Analysis
Advancements in technology are making vibration analysis more accessible and insightful. Wireless sensors, machine learning algorithms, and predictive analytics are paving the way for smarter, more proactive maintenance strategies.
Conclusion
Industrial vibration analysis is an essential component of modern maintenance strategies. It is a cost-effective method to enhance the reliability and longevity of machinery. As industries continue to evolve, the role of vibration analysis in maintaining the health of machinery will only grow in significance, proving to be an indispensable asset in the industrial world.