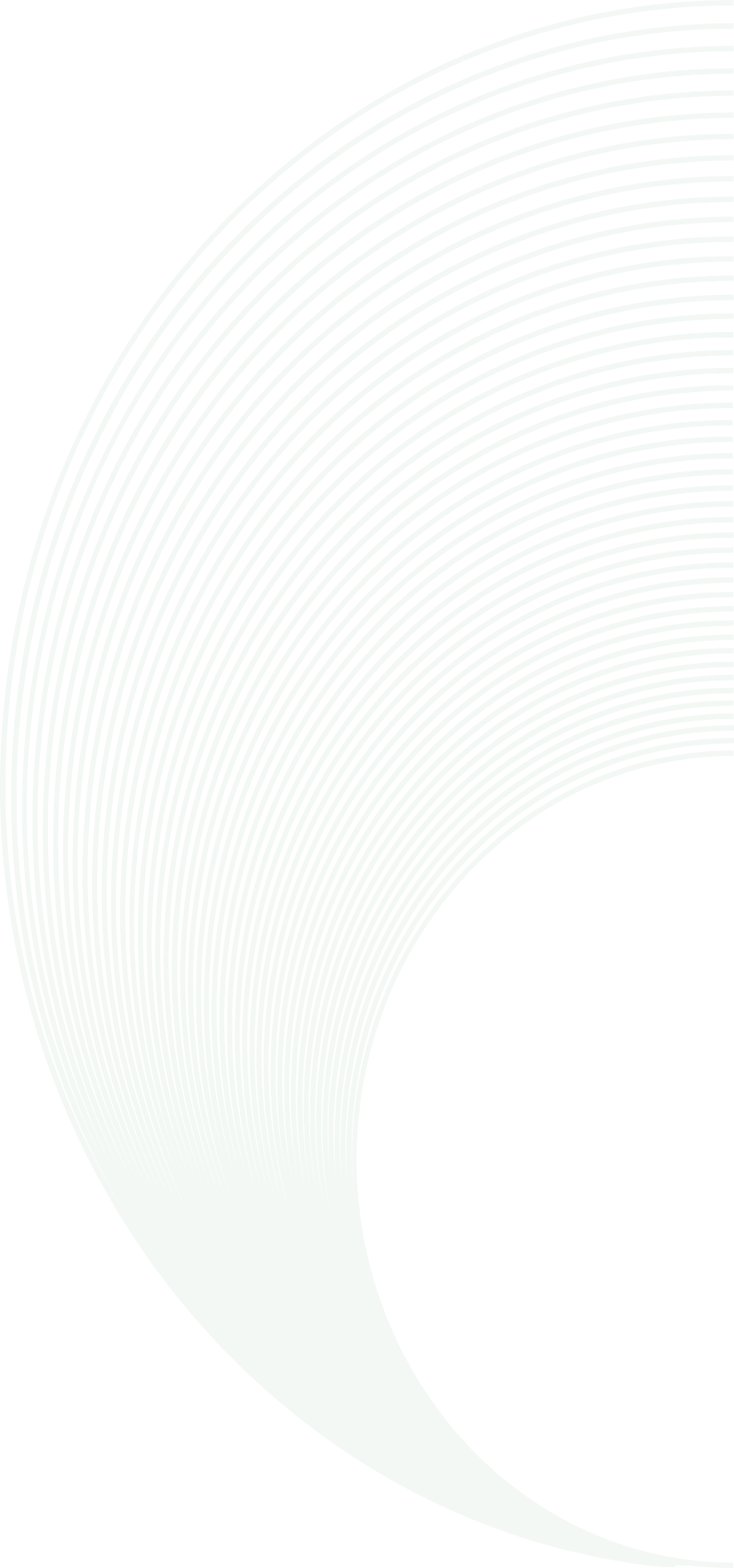
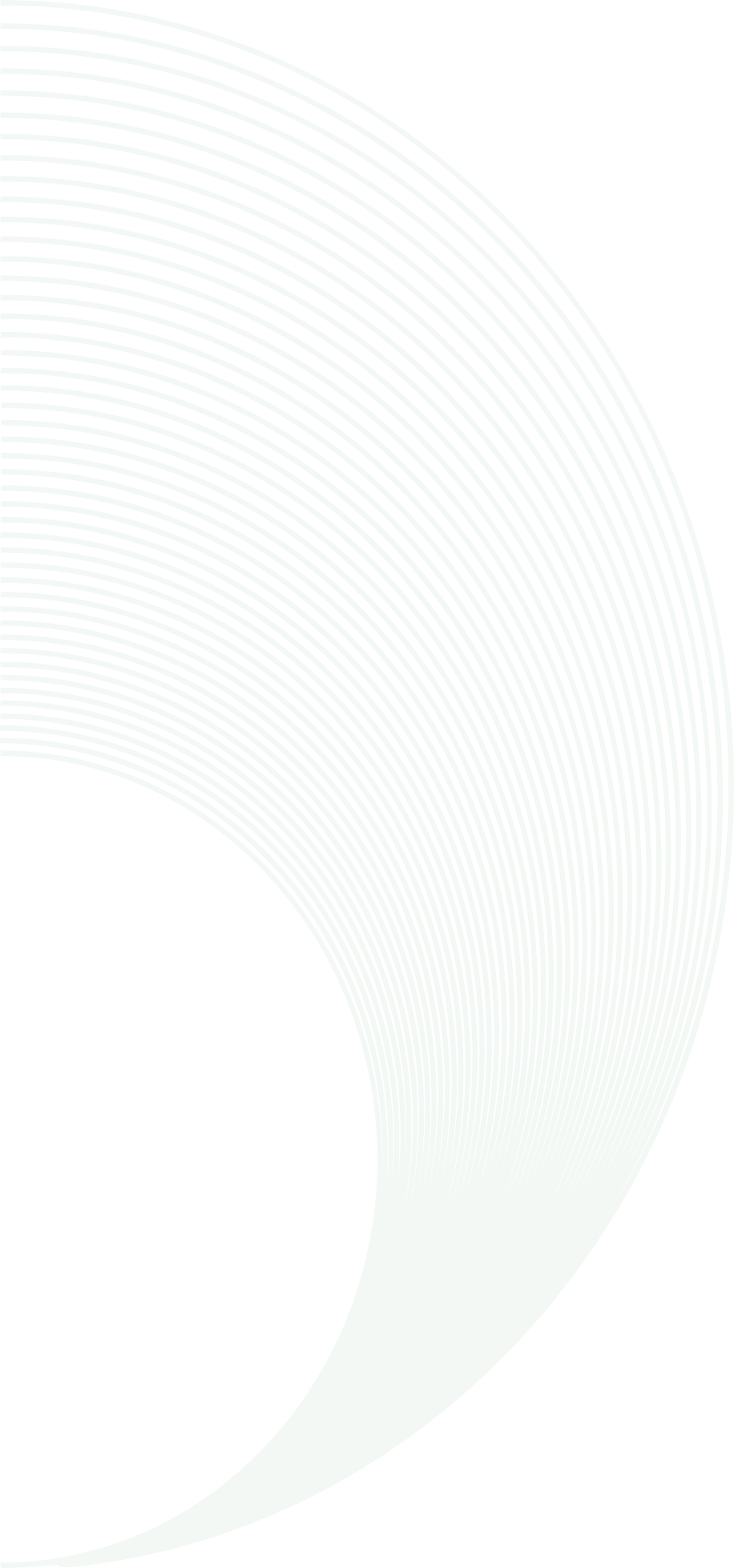
Lithography Techniques for Semiconductor Production in Belgium: Paving the Way for Advanced Electronics
Lithography plays a crucial role in the semiconductor manufacturing process, shaping the technology that powers everything from smartphones to complex industrial systems. In Belgium, a country known for its contributions to technological innovation, lithography techniques are pivotal in the production of high-performance semiconductors.
Understanding Lithography in Semiconductor Production
In semiconductor manufacturing, lithography is the process used to transfer intricate circuit patterns onto the surface of a semiconductor wafer.
This process begins with coating the wafer with a light-sensitive material known as a photoresist. A pattern is then projected onto the photoresist using light or other forms of radiation, which reacts with the resist to form the desired pattern. After exposure, the wafer undergoes a series of chemical treatments to develop the pattern, followed by etching to create the actual circuit design.
Lithography techniques are crucial because they define the size and density of the features on a semiconductor chip. As the demand for smaller, faster, and more efficient semiconductors increases, the lithography process must evolve to accommodate ever-decreasing feature sizes. In Belgium, advanced research institutions and semiconductor manufacturers focus on refining these techniques to meet global demands for high-performance microelectronics.
Photolithography: The Foundation of Semiconductor Fabrication
Photolithography is the most widely used lithographic technique in semiconductor production and serves as the foundation for creating the intricate patterns that make up the microchips. This technique involves using ultraviolet (UV) light to project a pattern onto the photoresist-coated wafer. The pattern, which is usually generated by a mask or reticle, is exposed to light, causing a chemical reaction in the resist.
In Belgium, photolithography is employed by several semiconductor foundries and research facilities, such as Imec, a leading nanoelectronics and digital technologies research center based in Leuven. Imec focuses on advancing photolithography for the production of integrated circuits, developing cutting-edge technologies such as extreme ultraviolet (EUV) lithography for next-generation semiconductors.
Photolithography continues to be the dominant method for semiconductor production due to its ability to create precise patterns at sub-micron resolutions. As semiconductor feature sizes shrink, photolithography techniques must evolve to maintain high throughput and accuracy, which is a key area of innovation in Belgium.
Extreme Ultraviolet Lithography
One of the most advanced photolithography techniques being developed for next-generation semiconductor production is extreme ultraviolet (EUV) lithography. EUV uses extremely short wavelengths of light, around 13.5 nm, to create even smaller and more detailed patterns on semiconductor wafers. This technique allows for the production of chips with features well below the wavelength limits of traditional photolithography.
EUV lithography is considered a breakthrough in semiconductor manufacturing, as it enables the creation of devices with higher transistor densities, leading to more powerful and energy-efficient microchips. In Belgium, research institutions like Imec are at the forefront of EUV development, working with leading semiconductor companies to refine the technology and integrate it into commercial production.
The implementation of EUV lithography requires advanced equipment, including state-of-the-art light sources, masks, and optics. As the semiconductor industry moves towards smaller nodes (such as 7 nm, 5 nm, and beyond), EUV lithography is expected to become more widely used to meet the demands of cutting-edge technology.
Electron Beam Lithography
Electron beam lithography (e-beam lithography) is another advanced technique used in semiconductor production, particularly for applications that require extremely high resolution or custom patterning. Unlike photolithography, which uses light, e-beam lithography uses a focused beam of electrons to write patterns directly onto the photoresist-coated wafer. This direct writing process offers high resolution and precision, making it ideal for research, development, and the production of low-volume, highly specialized semiconductor devices.
E-beam lithography is commonly used for the prototyping of new semiconductor devices, especially in the research and development stages. In Belgium, e-beam lithography is employed by companies and academic institutions for the development of cutting-edge semiconductor technologies, such as quantum computing and advanced memory devices.
One of the advantages of e-beam lithography is its ability to produce custom patterns without the need for masks, making it a versatile tool for innovation. However, the process is slower and less cost-effective for large-scale production compared to photolithography. As a result, e-beam lithography is typically used for niche applications rather than mass production.
Nanoimprint Lithography
Nanoimprint lithography (NIL) is an emerging technique in semiconductor manufacturing that involves pressing a mold with nanoscale features onto a wafer to transfer the pattern. This method offers several advantages over traditional photolithography, including higher resolution, lower cost, and the ability to create more complex patterns with fewer steps.
In Belgium, nanoimprint lithography is being explored by both research institutions and semiconductor companies to improve the production of small, high-performance devices. NIL can be particularly useful for manufacturing components such as sensors, integrated optics, and microelectromechanical systems (MEMS), where traditional photolithography might struggle to achieve the desired precision.
NIL is still in the development phase for large-scale semiconductor manufacturing but shows great potential due to its ability to produce extremely small and complex features. Researchers in Belgium are continuing to push the boundaries of NIL technology, seeking to integrate it into mainstream semiconductor production as the demand for miniaturization continues.
Challenges and Future Directions of Lithography in Belgium
As semiconductor devices continue to shrink, lithography faces several challenges. One of the primary obstacles is patterning at smaller nodes—as the industry moves towards the 3 nm and 2 nm nodes, it becomes increasingly difficult to achieve the precision required using current lithographic techniques. Additionally, the cost of advanced lithography equipment, such as EUV machines, is a significant barrier to widespread adoption.
In Belgium, institutions like Imec are addressing these challenges through continuous research and development in collaboration with global semiconductor companies. The focus is on advancing lithography technology to meet the growing demands for smaller, faster, and more powerful semiconductor devices. Innovations such as multi-patterning techniques, new materials, and hybrid lithographic approaches are expected to play a key role in overcoming these hurdles.
Moreover, the integration of artificial intelligence (AI) and machine learning into semiconductor manufacturing is poised to revolutionize lithography. AI can help optimize the lithographic process, improving accuracy and yield while reducing defects and costs.
Conclusion
Lithography techniques are at the heart of semiconductor production, and Belgium remains a leader in advancing these technologies. From traditional photolithography to cutting-edge EUV and nanoimprint lithography, the country’s research and development efforts continue to drive innovation in the semiconductor industry. As the demand for smaller, faster, and more energy-efficient devices grows, Belgium’s semiconductor sector is poised to play a critical role in shaping the future of technology. By pushing the boundaries of lithography, Belgium is ensuring that it remains at the forefront of semiconductor manufacturing, supporting industries worldwide with the essential components for the next generation of electronics.