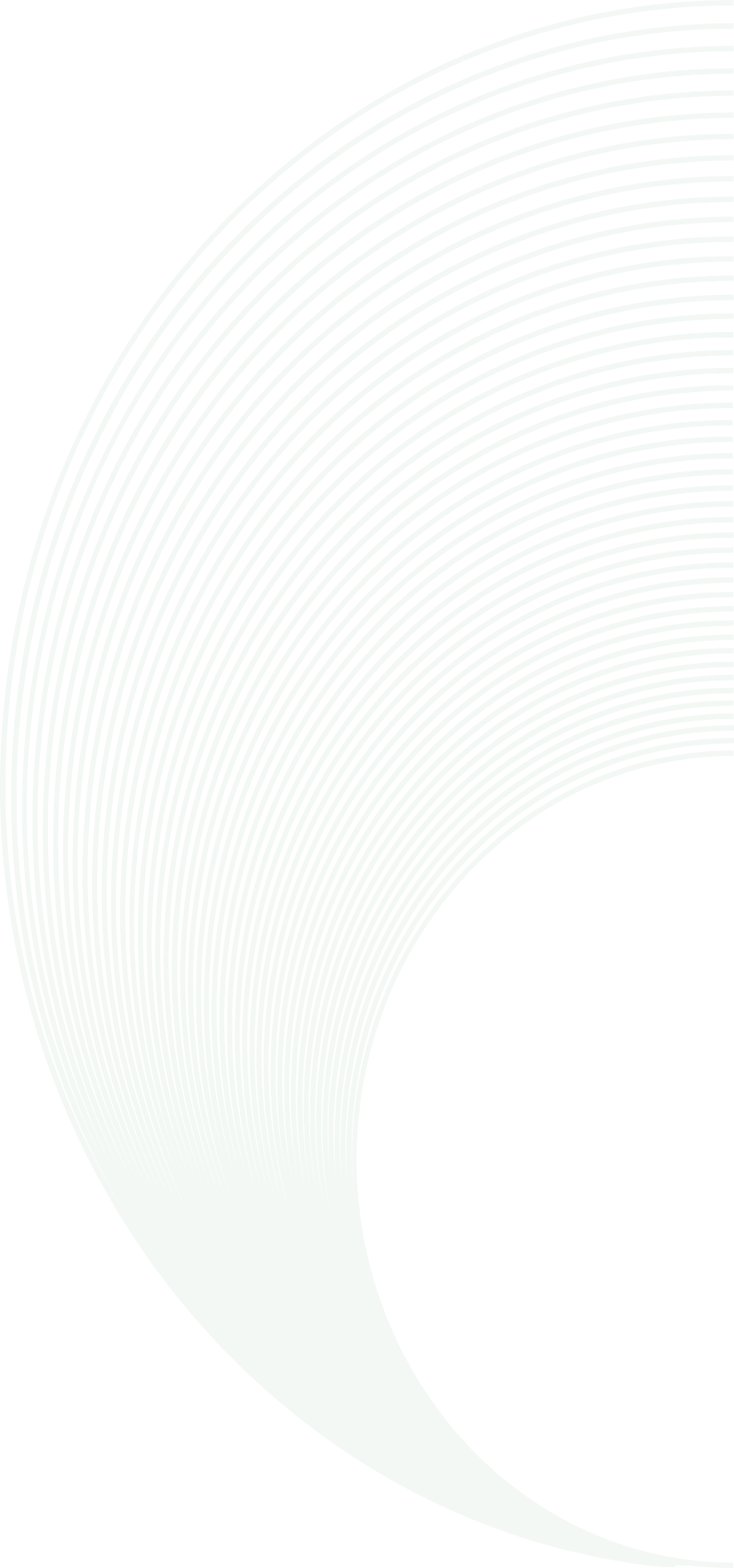
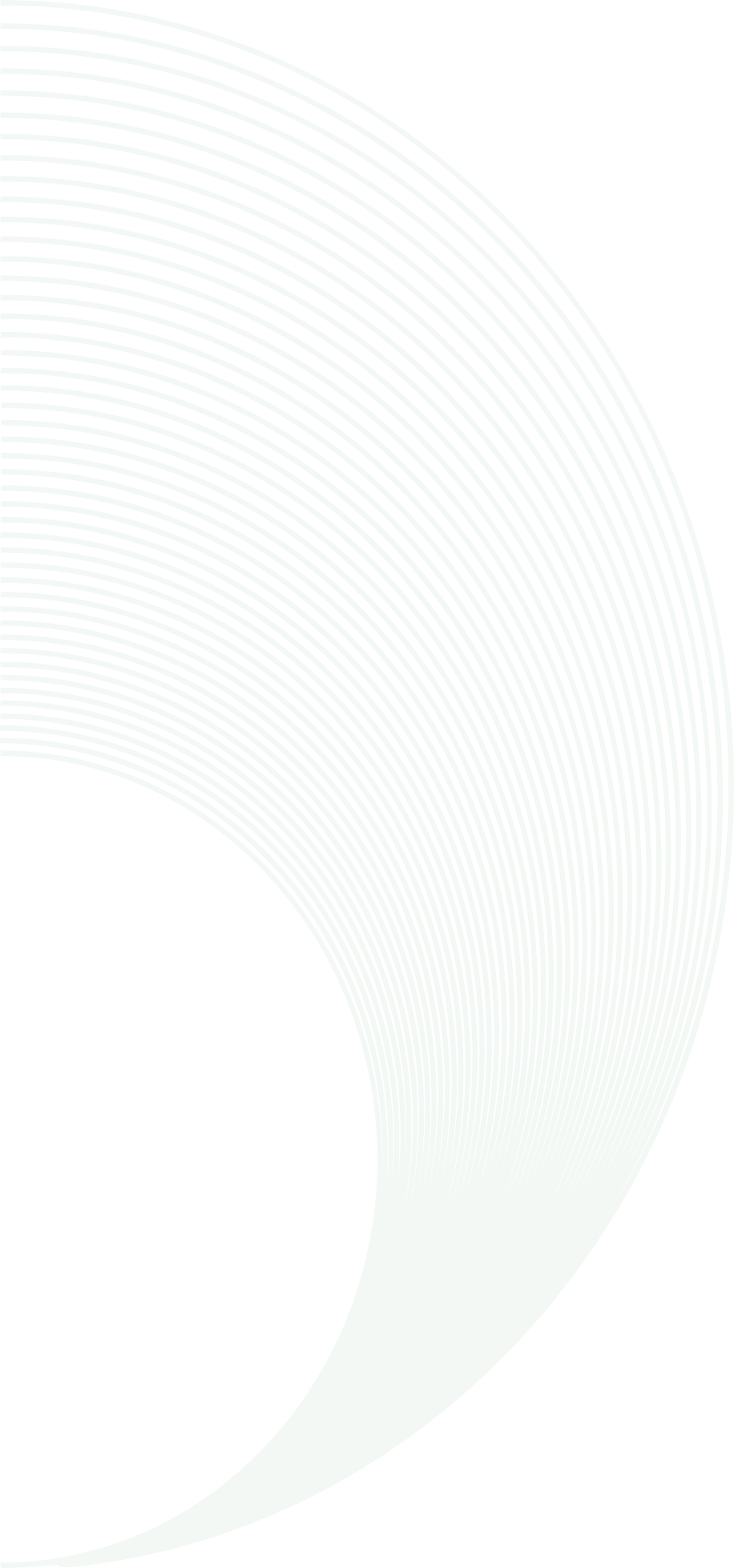
Non-Destructive Testing of Steel: Ensuring Strength and Reliability
Steel is a fundamental material in construction, manufacturing, and infrastructure, where its strength, durability, and reliability are critical. Non-destructive testing (NDT) of steel ensures structural integrity, quality control, and compliance without damaging the material.
What is Non-Destructive Testing (NDT) of Steel?
NDT refers to inspection methods that detect defects, inconsistencies, or material weaknesses in steel without causing damage. These techniques help identify cracks, voids, corrosion, and weld defects before they lead to failures.
Why NDT is Essential for Steel Inspection
- Prevents Structural Failures – Identifies potential weaknesses before they cause accidents.
- Ensures Compliance – Meets industry standards like ASME, ASTM, ISO, and API.
- Cost-Effective – Reduces the need for repairs and replacements by detecting issues early.
- Non-Intrusive & Efficient – Allows for inspections without halting operations.
Common NDT Methods for Steel Inspection
1. Ultrasonic Testing (UT)
- Uses high-frequency sound waves to detect internal defects.
- Ideal for thick steel structures, weld inspections, and pipelines.
- Provides precise depth and location of flaws.
2. Magnetic Particle Testing (MPT)
- Applies magnetic fields and iron particles to reveal surface and near-surface cracks.
- Best for ferromagnetic steel materials used in bridges, pressure vessels, and railways.
3. Radiographic Testing (RT)
- Uses X-rays or gamma rays to inspect internal defects in steel welds and components.
- Produces a detailed radiographic image for flaw detection.
- Essential for critical structures like oil & gas pipelines and aerospace components.
4. Eddy Current Testing (ECT)
- Uses electromagnetic induction to detect surface cracks, corrosion, and coating thickness.
- Common in automotive, aerospace, and tubing industries.
5. Visual Inspection (VT)
- The simplest and most widely used method.
- Inspectors check for visible defects like cracks, rust, or weld inconsistencies.
- Often combined with advanced optical tools for accuracy.
Industries that Rely on Steel NDT
- Construction & Infrastructure – Bridges, buildings, and tunnels.
- Oil & Gas – Pipelines, refineries, and offshore platforms.
- Automotive & Aerospace – Structural components, engine parts, and safety systems.
- Power Plants & Railways – Boilers, turbines, and railway tracks.
Choosing the Right NDT Method for Steel
- For internal defect detection: Ultrasonic or radiographic testing.
- For surface crack detection: Magnetic particle or eddy current testing.
- For quick, on-site inspections: Visual testing or magnetic particle testing.
- For high-precision analysis: Ultrasonic phased array (PAUT) or digital radiography (DR).
The Future of NDT in Steel Testing
Advancements in AI-driven inspections, real-time monitoring, and automated robotic testing are improving accuracy and efficiency in steel NDT. Drones, digital radiography, and machine learning-based flaw detection are making steel testing faster and more reliable.