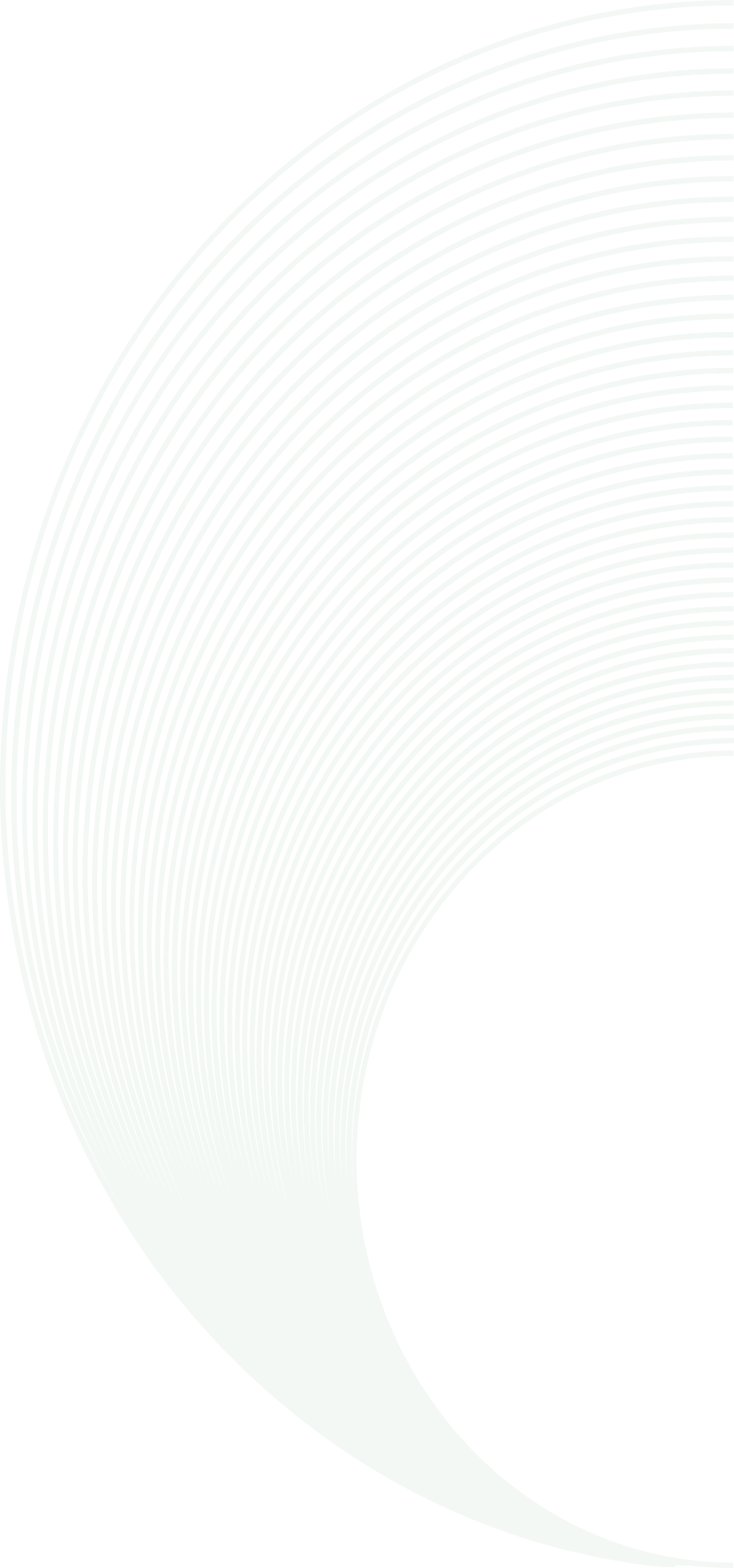
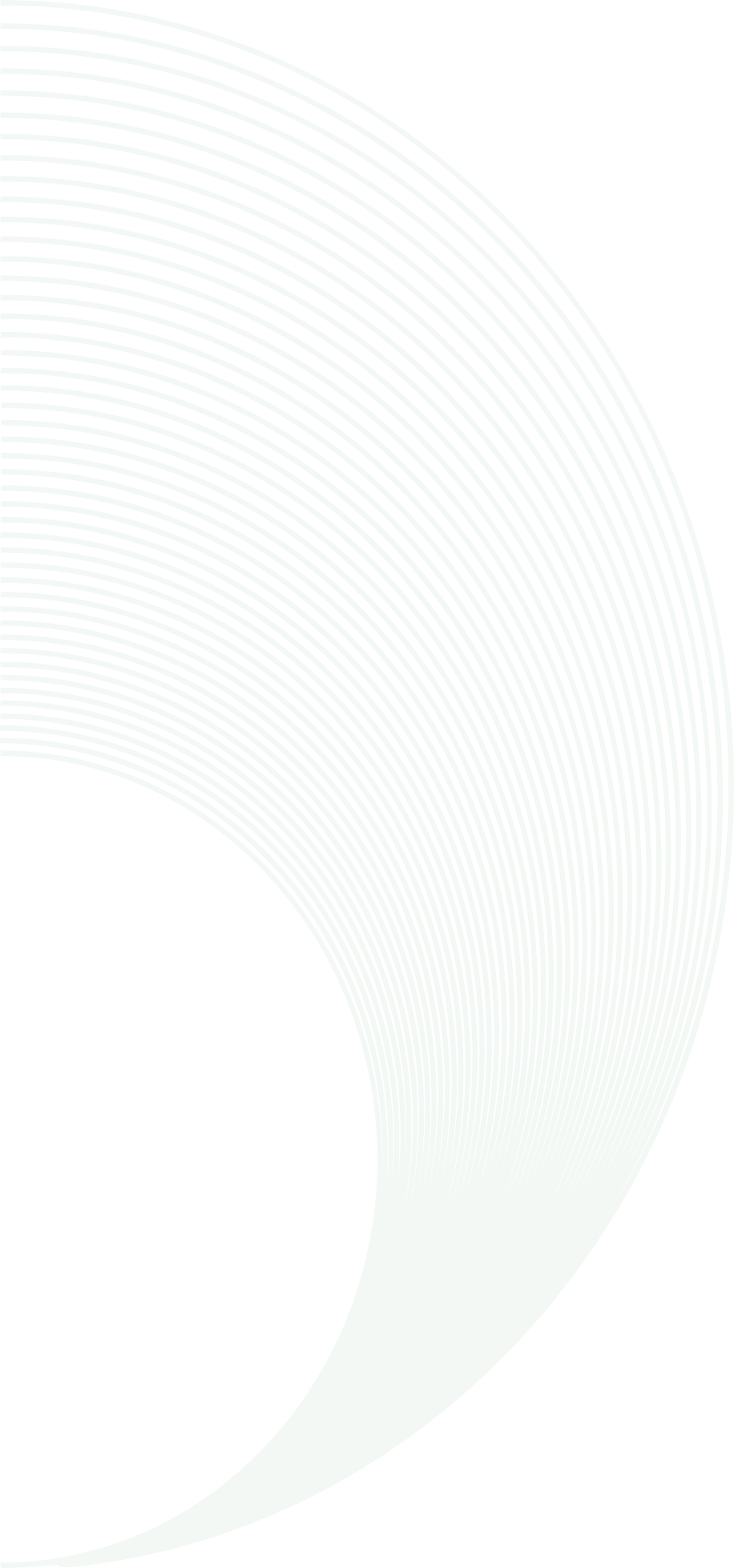
Pneumatic Diaphragm Pump: A Versatile and Reliable Solution for Fluid Transfer
A pneumatic diaphragm pump is a type of positive displacement pump used in various industries for transferring fluids, including liquids and slurries. Known for their versatility and reliability, these pumps are ideal for applications where conventional pumps might not perform effectively, such as with highly viscous, abrasive, or corrosive substances.
What is a Pneumatic Diaphragm Pump?
A pneumatic diaphragm pump operates using compressed air to drive the pump mechanism.
The core of the pump is a diaphragm, a flexible membrane that moves back and forth to displace fluid through the pump. When air pressure is applied to one side of the diaphragm, it moves, forcing the fluid to the discharge side of the pump. As the diaphragm returns to its original position, it creates suction on the inlet side, drawing in more fluid.
These pumps are highly efficient and capable of handling a wide variety of fluids, from clean water to abrasive slurries, making them ideal for industrial and chemical processing applications. Pneumatic diaphragm pumps are often preferred in environments where electrical equipment cannot be used due to potential hazards, such as in explosive atmospheres or in areas with a risk of fire.
Key Features of Pneumatic Diaphragm Pumps
- Air-Operated: Pneumatic diaphragm pumps are powered by compressed air, which allows them to operate in hazardous environments where electric pumps might pose a risk.
- Self-Priming: These pumps are capable of self-priming, which means they can start pumping fluid without the need for external assistance, even if the pump is initially dry.
- Adjustable Flow Rates: The flow rate of a pneumatic diaphragm pump can be adjusted by controlling the air supply. This makes them versatile for different applications that require varying flow rates.
- Dry Running Capability: Pneumatic diaphragm pumps can run dry without causing damage, unlike some other pumps that may require lubrication or a constant fluid supply to prevent overheating and wear.
- Durability: They are built to handle demanding applications, including transferring abrasive or corrosive materials. The diaphragms and pump components are made from durable materials like PTFE, rubber, or other chemically resistant substances.
Applications of Pneumatic Diaphragm Pumps
Pneumatic diaphragm pumps are widely used across many industries due to their ability to handle a variety of fluids under different conditions. Some of the most common applications include:
Chemical Processing: These pumps are ideal for transferring corrosive, toxic, or viscous chemicals. The chemical industry relies on pneumatic diaphragm pumps for applications like dosing, mixing, and transferring hazardous liquids.
Water and Wastewater Treatment: Pneumatic diaphragm pumps are commonly used for transferring sludge, wastewater, and other fluids in treatment plants. Their ability to handle high-viscosity fluids and solids makes them perfect for this application.
Food and Beverage: The food and beverage industry uses these pumps to handle delicate liquids like milk, sauces, or juices, where maintaining the integrity of the fluid is important. Pneumatic diaphragm pumps are also used to transfer other non-food-related liquids, such as cleaning solutions.
Pharmaceuticals: In pharmaceutical production, hygiene and safety are critical. Pneumatic diaphragm pumps are used for transferring pharmaceutical ingredients and fluids in a sanitary and contamination-free manner, ensuring compliance with industry standards.
Mining and Slurry Handling: Pneumatic diaphragm pumps are ideal for handling slurries, muds, and other abrasive fluids common in the mining industry. Their ability to handle high-density materials without clogging makes them an excellent choice for such demanding applications.
Advantages of Pneumatic Diaphragm Pumps
No Electricity Required: Because they are powered by air, pneumatic diaphragm pumps are an excellent choice for environments where electrical equipment cannot be used due to safety concerns. This includes locations with flammable gases or explosive atmospheres.
Versatility: These pumps can handle a wide range of fluids, including slurries, viscous fluids, and abrasive substances. Their ability to pump everything from water to chemicals makes them incredibly versatile.
Low Maintenance: Pneumatic diaphragm pumps are relatively easy to maintain due to their simple construction. With fewer moving parts compared to other pump types, they are less likely to fail and require fewer repairs.
Increased Safety: The lack of electrical components reduces the risk of sparks or electrical hazards, which is especially important when working with volatile substances.
Ease of Installation: Pneumatic diaphragm pumps are typically compact and can be installed in a variety of positions, including vertically or horizontally, depending on the needs of the system.
Disadvantages of Pneumatic Diaphragm Pumps
Noise: Pneumatic diaphragm pumps can be noisy due to the operation of the air compressor. This can be a consideration in applications where noise levels need to be minimized.
Air Consumption: These pumps require a constant supply of compressed air, which can be a limitation in terms of operating cost and energy consumption, especially in large-scale operations.
Pulsation: Due to their positive displacement nature, pneumatic diaphragm pumps can create pulsations in the flow. This can sometimes be mitigated by using pulse dampeners or specialized systems.
Conclusion
Pneumatic diaphragm pumps are a reliable and versatile option for a wide range of industries that need to transfer fluids under challenging conditions. Their ability to handle corrosive, abrasive, and viscous substances, combined with their safety and durability, makes them an essential tool in sectors like chemical processing, wastewater treatment, food and beverage, and more. While they may have some limitations, the benefits of pneumatic diaphragm pumps, such as ease of maintenance, self-priming capability, and air-driven operation, often outweigh the drawbacks. These pumps provide an efficient solution for fluid transfer needs, ensuring consistent and reliable performance in even the most demanding environments.