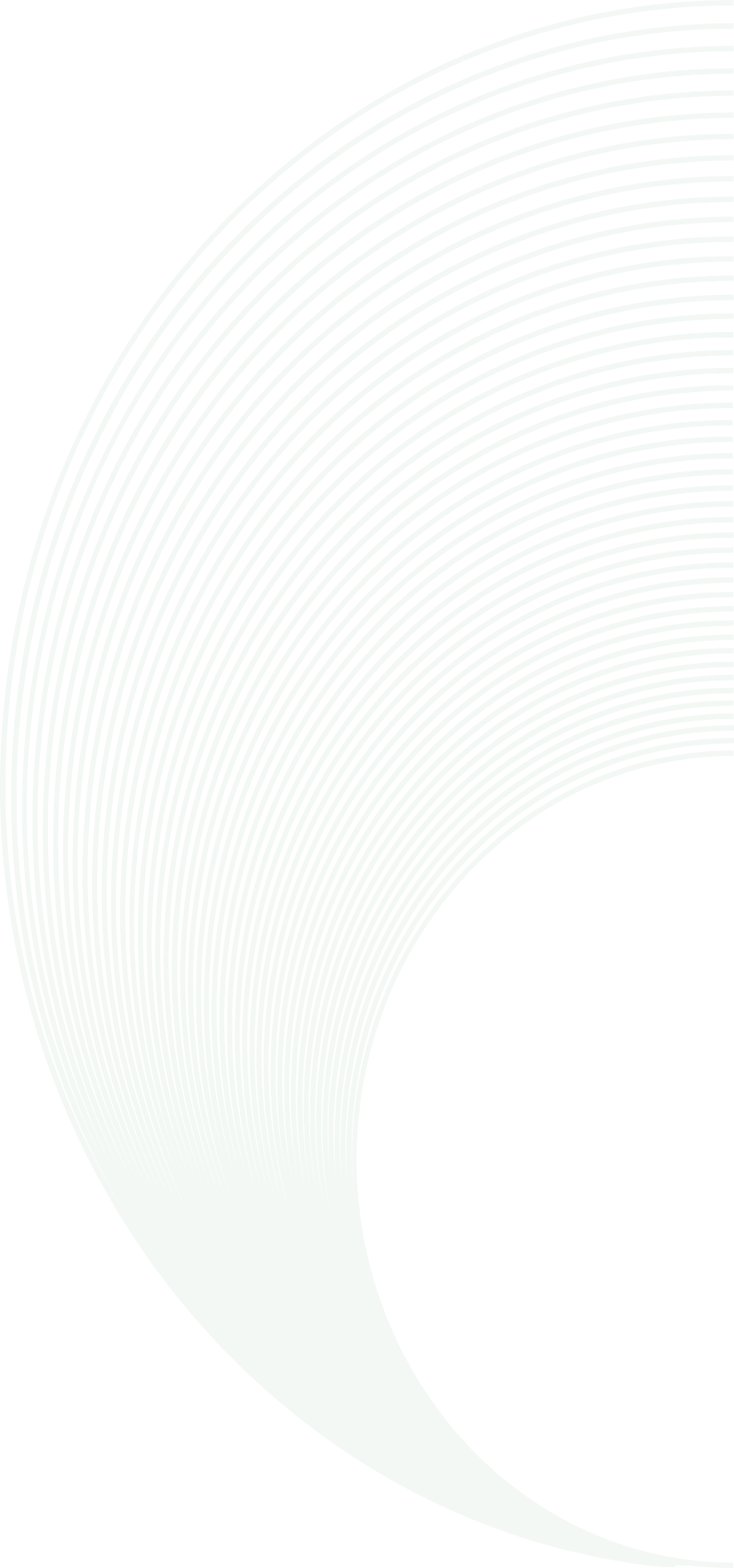
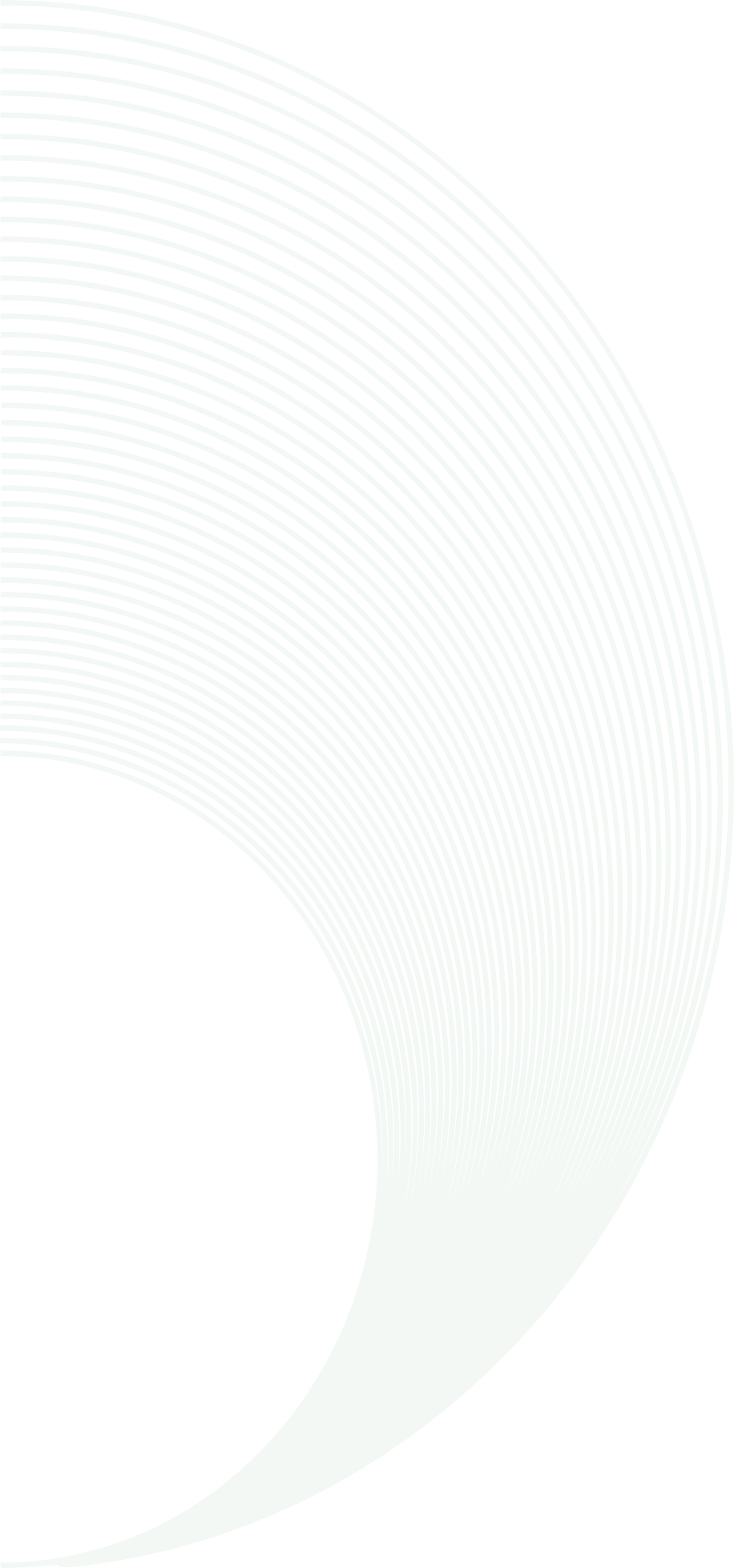
Types of Hydraulic Directional Control Valves
A hydraulic directional control valve is a crucial component in hydraulic systems, responsible for directing the flow of hydraulic fluid to various actuators, such as cylinders or motors, enabling them to perform specific tasks. The valve controls the direction of fluid flow within the hydraulic circuit, which, in turn, determines the movement and function of the system’s mechanical components. Understanding the different types of hydraulic directional control valves can help in choosing the right one for specific applications.
Main Types of Hydraulic Directional Control Valves
1. Spool Valves
Spool valves are the most common type of directional control valve. They use a cylindrical spool inside the valve body that moves to different positions to control the flow of hydraulic fluid. These valves come in various configurations, such as 2-way, 3-way, and 4-way valves, depending on the number of flow paths they control.
- 2-Way Spool Valve: Controls the flow between two ports (input and output). Typically used for simple on/off control.
- 3-Way Spool Valve: Allows fluid to flow between three ports, commonly used to control single-acting cylinders.
- 4-Way Spool Valve: Provides control over four ports, often used for double-acting cylinders, enabling extension and retraction of hydraulic actuators.
2. Poppet Valves
Poppet valves use a poppet (a conical or cylindrical element) to block or open fluid flow. They are known for their fast response time and leak-tight sealing, making them ideal for applications that require precise on/off control. Poppet valves are typically used in high-pressure systems and have fewer moving parts compared to spool valves, which can result in longer service life.
3. Solenoid-Operated Valves
Solenoid-operated valves use an electrical solenoid to move the spool or poppet and control the direction of fluid flow. The solenoid is an electromagnet that, when energized, moves the spool to different positions. These valves are commonly used in automation and remote control applications due to their quick response and ability to be controlled electronically.
4. Manual Valves
Manual directional control valves require human intervention to change the flow direction. Operators move a lever, handle, or knob to shift the spool, allowing or blocking the flow of fluid. These valves are often used in situations where simple control is required, or where automation is unnecessary.
5. Pilot-Operated Valves
Pilot-operated directional control valves are controlled by another, smaller valve known as a pilot valve. This smaller valve directs fluid to move the main valve’s spool, allowing control over higher flows and pressures. These valves are commonly used in large or complex hydraulic systems where direct solenoid control would be insufficient.
6. Hydraulic Motor Control Valves
These are specialized valves designed for use with hydraulic motors, controlling the flow direction to the motor and regulating its speed and torque. Motor control valves often include features like flow control and pressure compensation to optimize motor performance.
Key Features to Consider When Selecting a Hydraulic Directional Control Valve
Flow Rate: Different valves are designed to handle varying flow rates. It’s important to choose a valve that can manage the required flow rate for your hydraulic system.
Pressure Rating: The valve must be able to withstand the hydraulic system’s operating pressure without failing or leaking.
Valve Actuation: Determine whether manual, solenoid, or pilot-operated actuation is best suited to your system’s needs, based on how the valve will be operated.
Port Configuration: The number of ports and flow paths (2-way, 3-way, or 4-way) should match the complexity of the hydraulic system.
Mounting Style: Hydraulic directional control valves come in various mounting configurations, such as subplate, flange, or inline, which can affect how they are integrated into the system.
Applications of Hydraulic Directional Control Valves
Hydraulic directional control valves are used in a wide range of industries and applications, including:
- Construction Machinery: Controlling hydraulic cylinders in excavators, bulldozers, and cranes.
- Agricultural Equipment: Operating hydraulic systems in tractors, harvesters, and other farming machinery.
- Industrial Automation: Managing the movement of hydraulic presses, lifts, and conveyor systems.
- Aerospace and Marine: Controlling hydraulic actuators in aircraft and ships.
- Automotive Manufacturing: Operating hydraulic presses and robotic systems in car production lines.
Conclusion
Hydraulic directional control valves are critical components in any hydraulic system, with different types suited for various applications. Understanding the differences between spool valves, poppet valves, solenoid-operated valves, and others will help ensure the right choice is made for optimal system performance. Whether for industrial machinery, construction equipment, or agricultural use, selecting the appropriate valve type based on flow rate, pressure requirements, and operational needs is key to efficient hydraulic control.