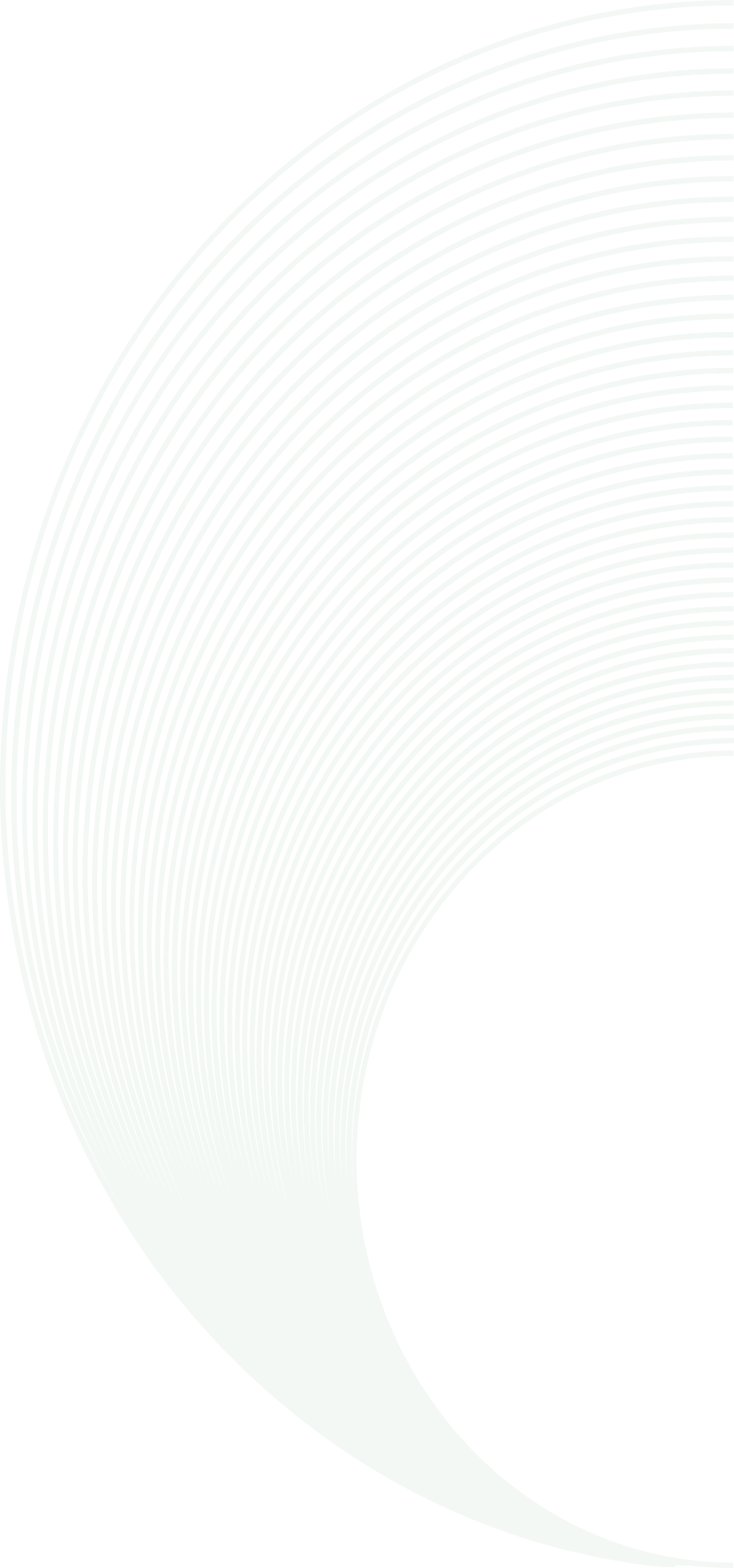
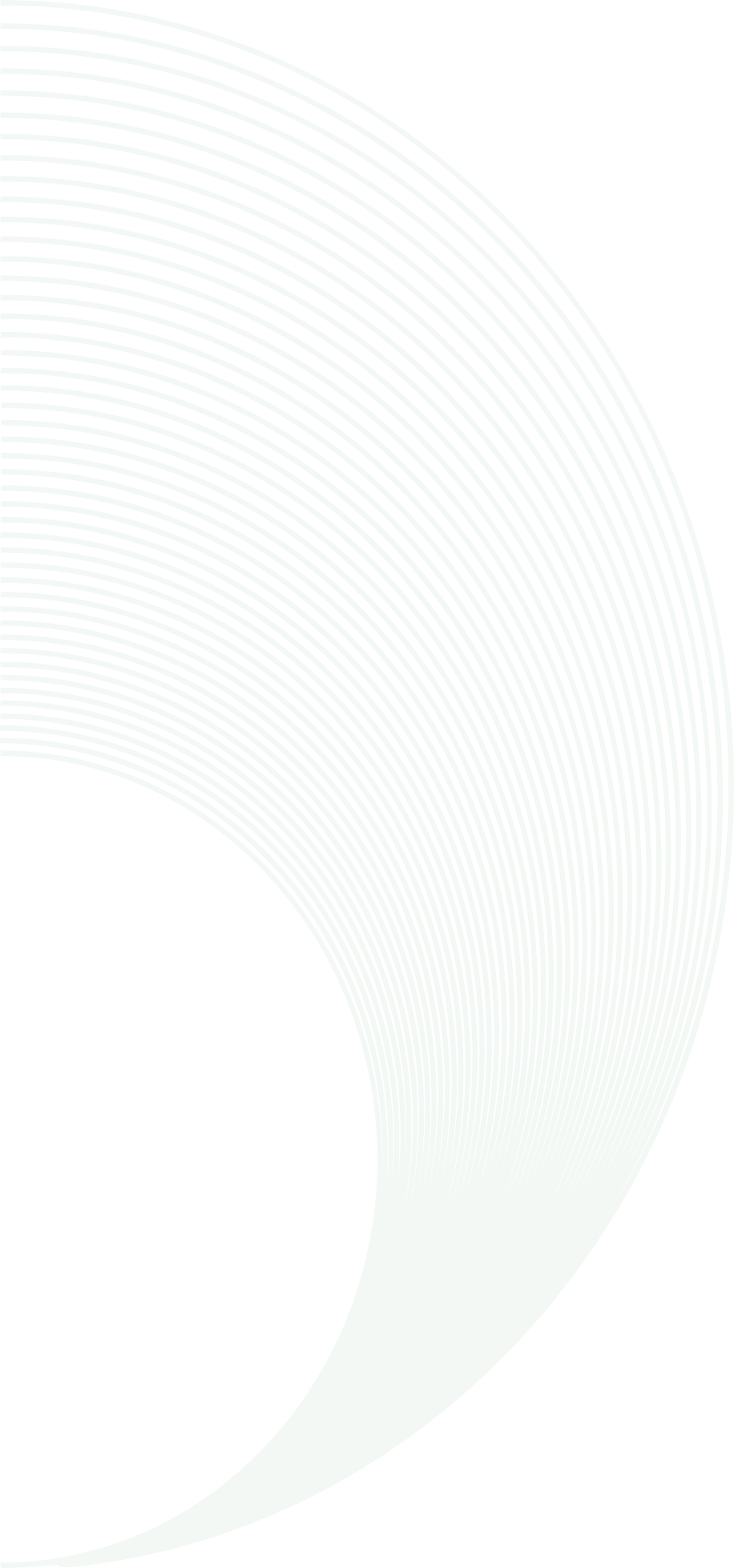
Ultrasonic and Magnetic Particle Testing: Key Methods for Flaw Detection
Non-destructive testing (NDT) plays a crucial role in ensuring the structural integrity and reliability of materials used in various industries. Among the most widely used techniques, Ultrasonic Testing (UT) and Magnetic Particle Testing (MPT) stand out for their ability to detect internal and surface flaws without damaging the material. These methods are essential in industries like aerospace, oil & gas, automotive, and manufacturing.
What is Ultrasonic Testing (UT)?
Ultrasonic Testing uses high-frequency sound waves to inspect materials for defects. A transducer sends ultrasonic waves into the material, and the returning echoes help identify cracks, voids, and inclusions.
Advantages of Ultrasonic Testing
- Detects internal and sub-surface flaws with high precision.
- Works on a wide range of materials, including metals, plastics, and composites.
- Portable and efficient, making it suitable for field inspections.
- Provides quantitative data on flaw size, depth, and location.
Applications of UT
- Inspecting welds, pipelines, and pressure vessels.
- Quality control in automotive and aerospace components.
- Evaluating structural integrity in bridges and buildings.
What is Magnetic Particle Testing (MPT)?
Magnetic Particle Testing is a surface inspection method used for detecting cracks, seams, and discontinuities in ferromagnetic materials. It works by magnetizing the material and applying fine iron particles that accumulate around defect areas.
Advantages of Magnetic Particle Testing
- Quick and cost-effective for detecting surface and near-surface defects.
- Works effectively on welds, castings, and machined components.
- Provides immediate visual indication of defects.
Applications of MPT
- Inspecting automotive parts, pipelines, and offshore structures.
- Quality control in manufacturing and metal fabrication.
- Aerospace and railway maintenance for detecting fatigue cracks.
Choosing the Right Method for Flaw Detection
- Use Ultrasonic Testing when inspecting critical internal defects in materials like welded joints, pressure vessels, and composite structures.
- Opt for Magnetic Particle Testing when checking surface cracks in ferromagnetic metals, such as iron, steel, and nickel alloys.
Future of Flaw Detection in NDT
With advancements in AI-driven analysis, automated inspection systems, and real-time monitoring, both UT and MPT are evolving to offer greater accuracy and efficiency. The integration of robotic scanners and IoT-enabled devices is further enhancing data collection and predictive maintenance.