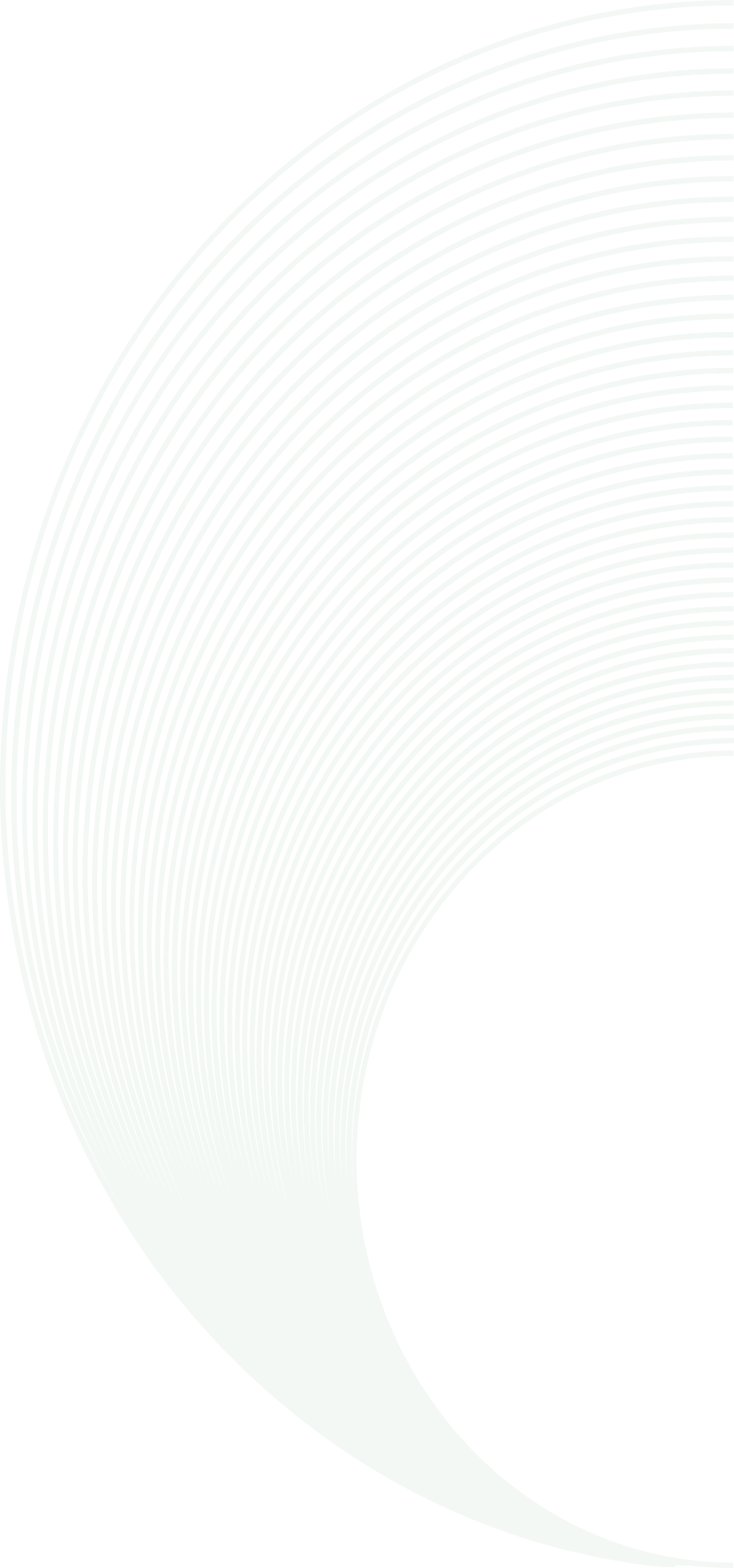
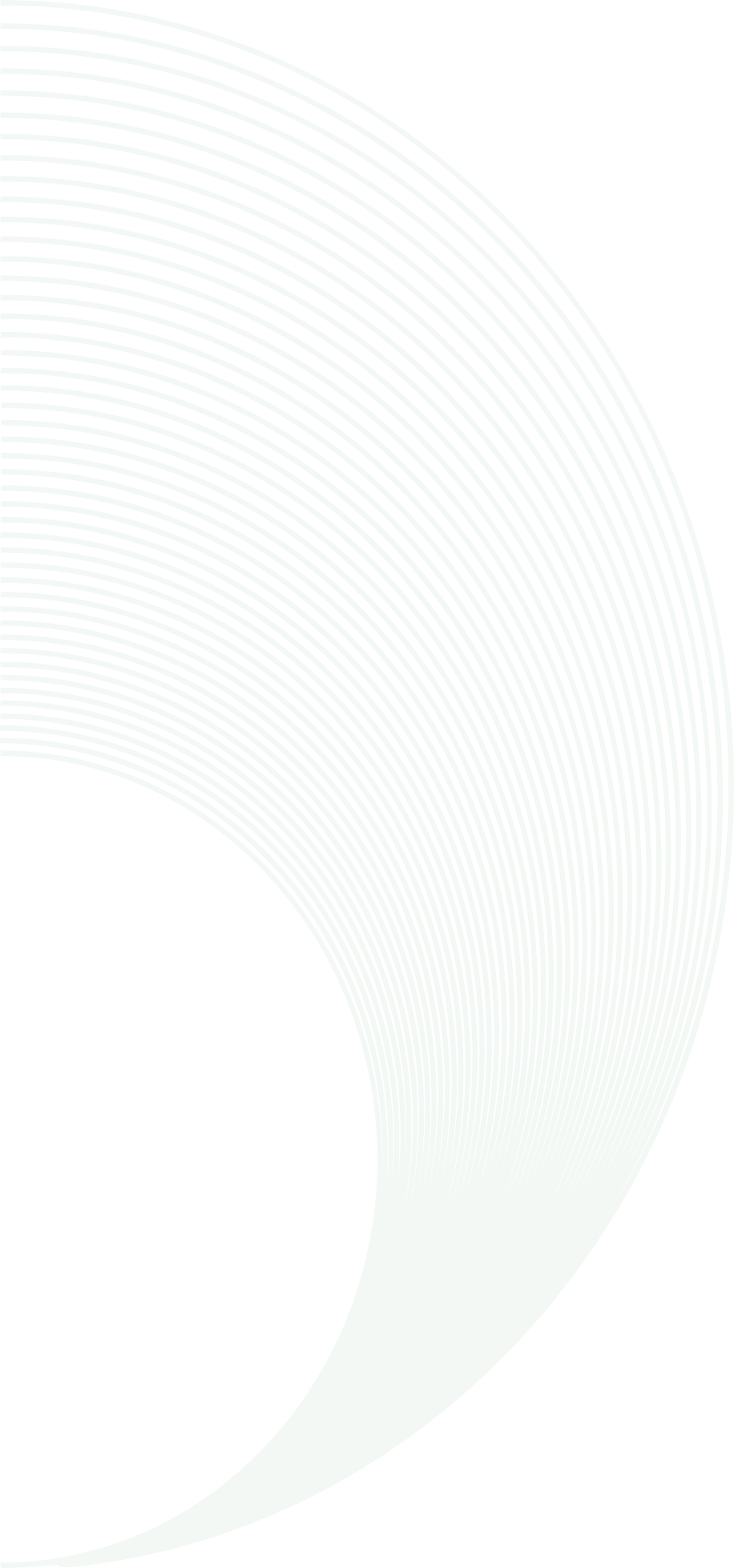
Understanding Cryogenic Argon Production
Cryogenic argon production is a critical process in the industrial gases industry, providing high-purity argon gas for various applications, from welding to electronics manufacturing. Argon, an inert gas, is the third most abundant gas in the Earth's atmosphere, making up about 0.93% by volume. However, its separation and production involve sophisticated techniques due to its low concentration and the need for high purity.
What Is Cryogenic Argon Production?
Cryogenic argon production involves the extraction of argon from the atmosphere using cryogenic air separation units (ASUs). The process leverages the fact that different gases in the air have different boiling points. By cooling air to extremely low temperatures, the various components can be liquefied and separated based on their boiling points.
The Cryogenic Air Separation Process
Air Intake and Compression:
- The process begins with the intake of ambient air, which is then filtered to remove dust and other particulates. The air is compressed to high pressures to make the separation process more efficient.
Air Cooling and Liquefaction:
- The compressed air is then cooled to cryogenic temperatures (around -196°C or lower) using a series of heat exchangers. At these temperatures, the air liquefies, allowing the different components (nitrogen, oxygen, argon) to be separated based on their unique boiling points.
Distillation:
- The liquefied air is fed into a distillation column. Nitrogen, which has the lowest boiling point (-196°C), boils off first and is separated. Oxygen, with a slightly higher boiling point (-183°C), is the next to be separated. Argon, with a boiling point of -186°C, is extracted during the middle of the distillation process.
Purification:
- The crude argon obtained from the distillation process still contains traces of oxygen and nitrogen. It is then subjected to further purification, often through additional distillation columns or other chemical processes, to achieve the desired purity level, typically 99.999% or higher.
Storage and Distribution:
- The purified argon is stored in cryogenic tanks as a liquid or converted into gas for distribution to end-users. It can be transported in specialized cryogenic containers or delivered via pipelines, depending on the customer's requirements.
Applications of Cryogenic Argon
1. Metal Fabrication and Welding:
- Argon is widely used as a shielding gas in welding, especially in processes like MIG (Metal Inert Gas) and TIG (Tungsten Inert Gas) welding. It prevents oxidation and contamination by creating an inert atmosphere around the weld area.
2. Electronics and Semiconductor Manufacturing:
- In the electronics industry, argon is used in the manufacturing of semiconductors and other electronic components. Its inert nature makes it ideal for processes that require a non-reactive environment.
3. Steelmaking:
- Argon is used in the steel industry to remove impurities during the production process. It helps in stirring molten steel, reducing oxidation, and improving the quality of the final product.
4. Lighting and Lasers:
- Argon is also used in the production of certain types of lighting, such as incandescent and fluorescent lamps, as well as in lasers for various industrial and medical applications.
5. Food and Beverage Industry:
- In the food and beverage industry, argon is used to displace oxygen in packaging, helping to preserve the freshness and extend the shelf life of products.
Advantages of Cryogenic Argon Production
- High Purity: Cryogenic processes can produce argon with extremely high purity, essential for industries like electronics and welding.
- Scalability: Cryogenic air separation units can be scaled to meet the demands of different industries, from small-scale operations to large industrial complexes.
- Efficiency: Modern cryogenic plants are highly efficient, recovering a significant amount of the argon present in the air, thus optimizing production costs.
Challenges in Cryogenic Argon Production
- Energy-Intensive Process: The cooling and compression of air to cryogenic temperatures require significant energy, making the process costly.
- Complex Equipment: The equipment used in cryogenic air separation, such as compressors, heat exchangers, and distillation columns, is highly specialized and requires regular maintenance.
- Capital Investment: Setting up a cryogenic air separation plant involves substantial capital investment, which can be a barrier for smaller companies.
Conclusion
Cryogenic argon production is a vital process for many industries that require high-purity argon gas. While the process is energy-intensive and requires significant investment, the advantages of high purity, scalability, and efficiency make it the preferred method for argon production. As industries continue to demand higher purity gases for advanced applications, cryogenic argon production will remain a cornerstone of the industrial gas sector.