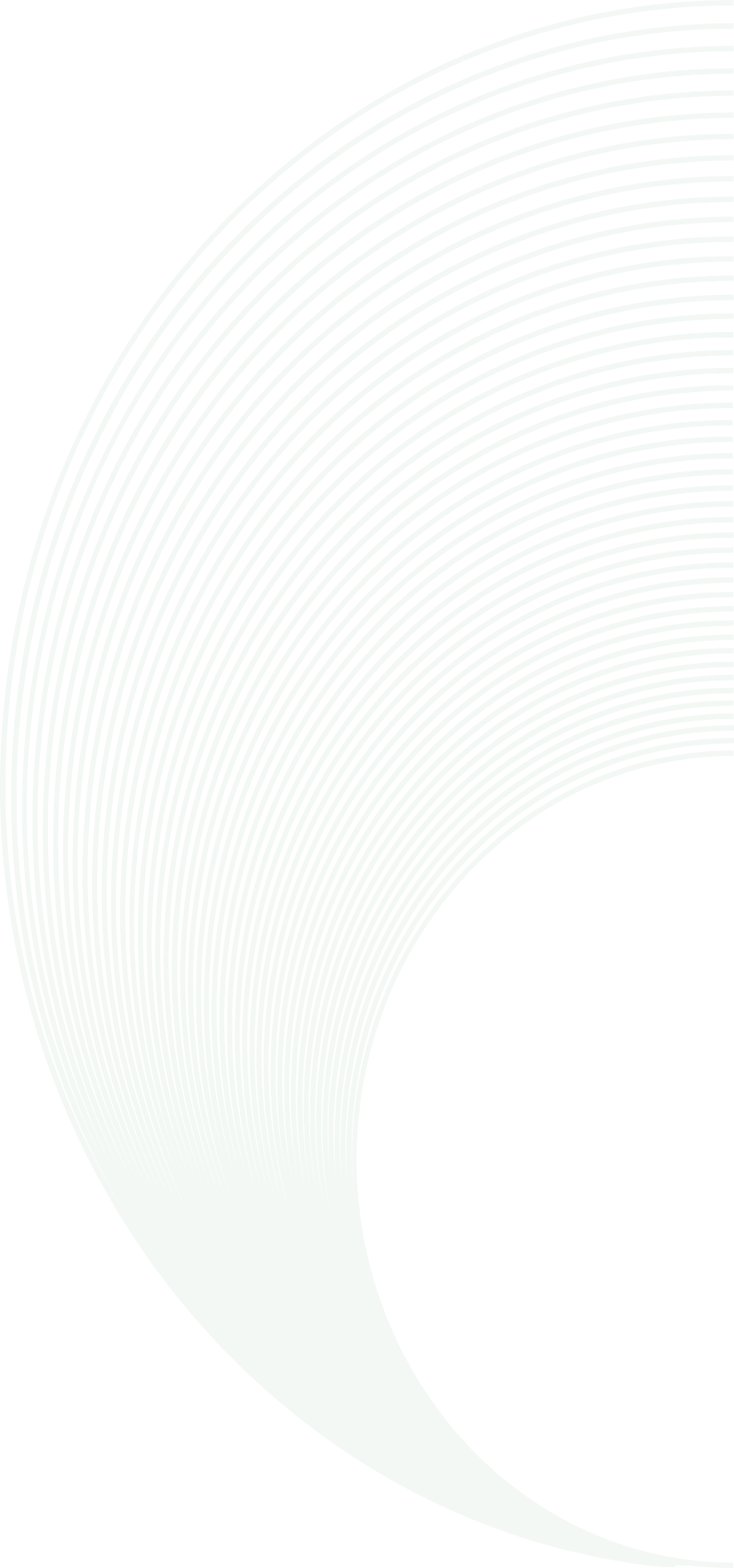
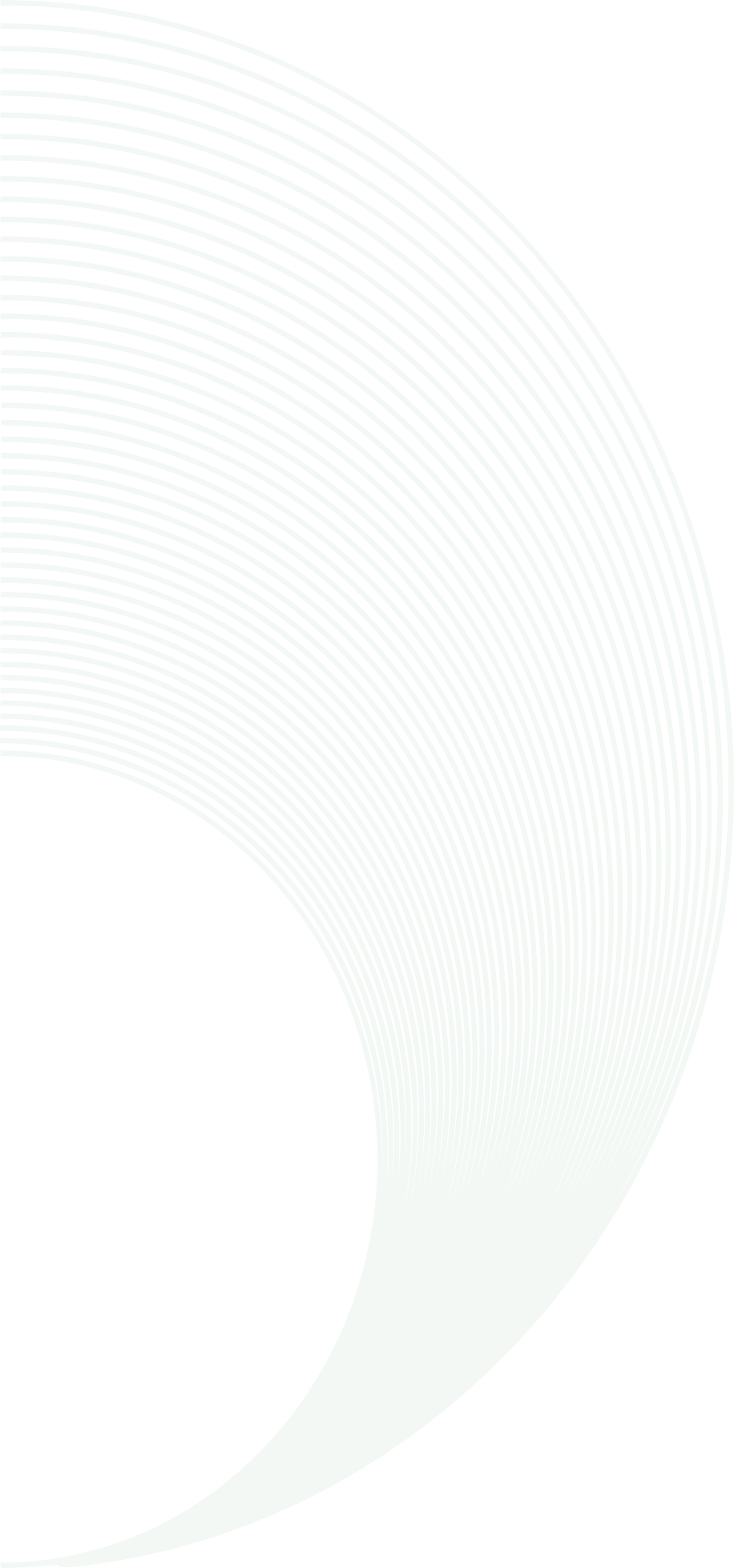
Understanding Manufacturing Overhead Costs
Manufacturing overhead costs are essential components of the total production costs incurred by a manufacturing company. These costs, which are sometimes referred to as indirect costs or factory overhead, include all expenses related to the manufacturing process that cannot be directly traced to specific products. Understanding these costs is crucial for accurate product pricing, budgeting, and overall financial management.
Components of Manufacturing Overhead Costs
Manufacturing overhead encompasses various expenses, which can be grouped into several categories:
Indirect Materials: These are materials used in the production process but not directly tied to a specific product. Examples include lubricants, cleaning supplies, and small tools.
Indirect Labor: This refers to wages paid to employees who support the manufacturing process but do not directly produce goods. Examples include supervisors, maintenance staff, and quality control inspectors.
Utilities: Costs associated with electricity, water, gas, and other utilities consumed in the manufacturing facility fall under overhead.
Depreciation: The reduction in value of manufacturing equipment and facilities over time is considered an overhead cost. This is calculated based on the useful life of the assets.
Rent and Property Taxes: If the manufacturing facility is leased, the rent is part of overhead costs. Similarly, property taxes on owned facilities also contribute to overhead.
Insurance: Premiums paid for insuring the manufacturing facility, equipment, and inventory are included in overhead costs.
Maintenance and Repairs: Expenses incurred for maintaining and repairing machinery and equipment used in the production process are also considered overhead.
Importance of Understanding Overhead Costs
Accurate Product Costing: Knowing manufacturing overhead costs allows businesses to allocate these expenses to the cost of goods sold (COGS), providing a clearer picture of product profitability.
Pricing Strategy: Accurate understanding of overhead costs helps manufacturers set competitive prices while ensuring profitability.
Budgeting and Financial Planning: By monitoring and controlling overhead costs, companies can make informed decisions on budgeting, investments, and cost-cutting strategies.
Performance Evaluation: Analyzing overhead costs helps identify areas of inefficiency, allowing businesses to streamline operations and improve overall productivity.
Methods of Allocating Overhead Costs
To accurately assign manufacturing overhead costs to products, companies use various allocation methods:
Traditional Costing: This method typically uses a predetermined overhead rate based on direct labor hours or machine hours to allocate overhead costs.
Activity-Based Costing (ABC): ABC allocates overhead costs based on the actual activities that drive costs. This method provides a more accurate reflection of how resources are consumed, especially in complex manufacturing environments.
Managing Manufacturing Overhead Costs
Effective management of manufacturing overhead costs involves several strategies:
Regular Monitoring: Regularly reviewing overhead costs helps identify trends, variances, and areas for improvement.
Cost Control Measures: Implementing cost-saving measures, such as energy-efficient practices and preventive maintenance, can help reduce overhead expenses.
Investing in Technology: Utilizing software for budgeting, tracking, and analyzing overhead costs can provide insights for better decision-making.
Employee Training: Ensuring employees are well-trained in efficient practices can reduce waste and improve productivity, subsequently lowering overhead costs.
Conclusion
Manufacturing overhead costs are a critical element of the overall production cost structure. By understanding and effectively managing these costs, businesses can improve their financial performance, enhance pricing strategies, and maintain competitiveness in the marketplace. Whether through traditional costing methods or advanced activity-based costing, accurately allocating overhead costs is essential for sound financial management and operational efficiency in manufacturing.