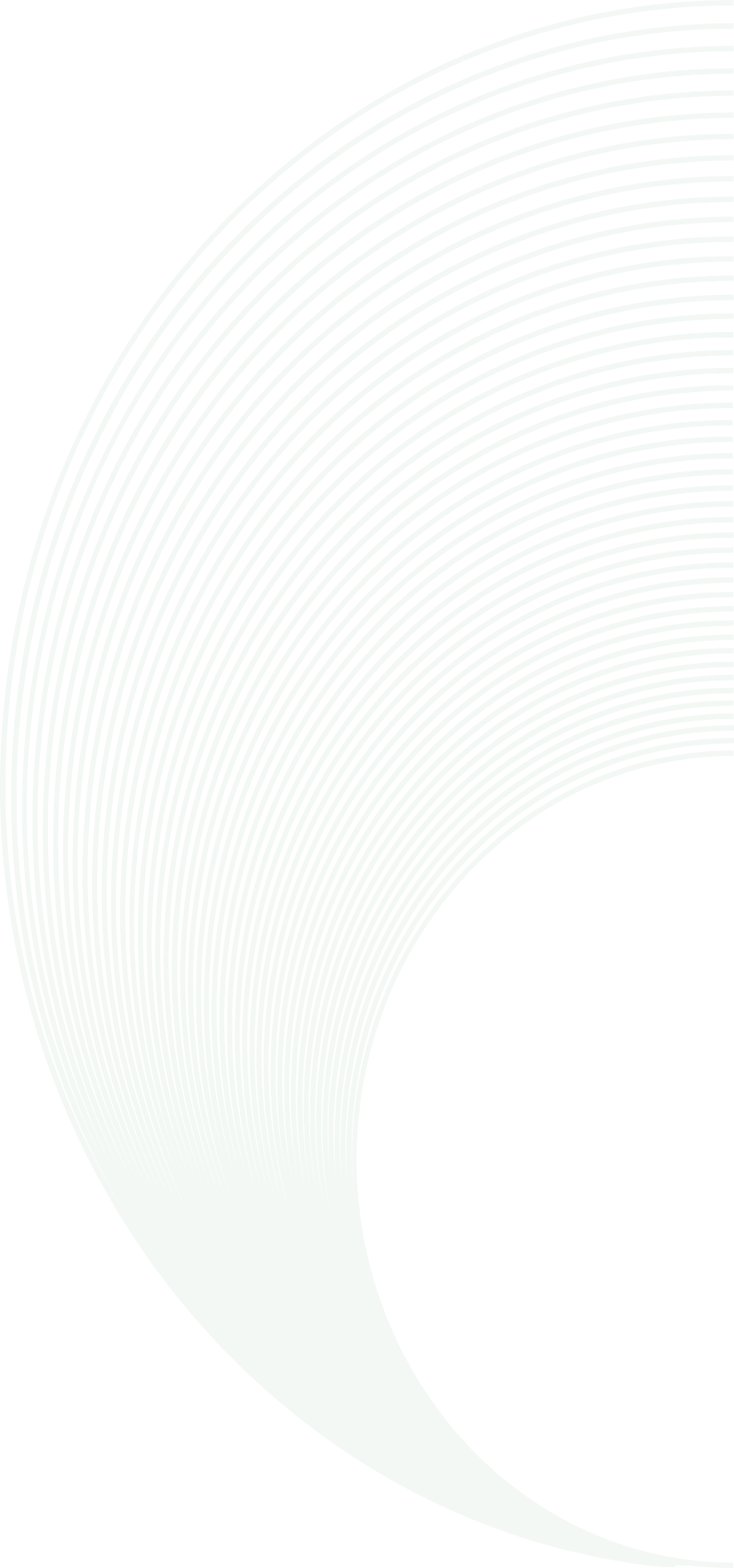
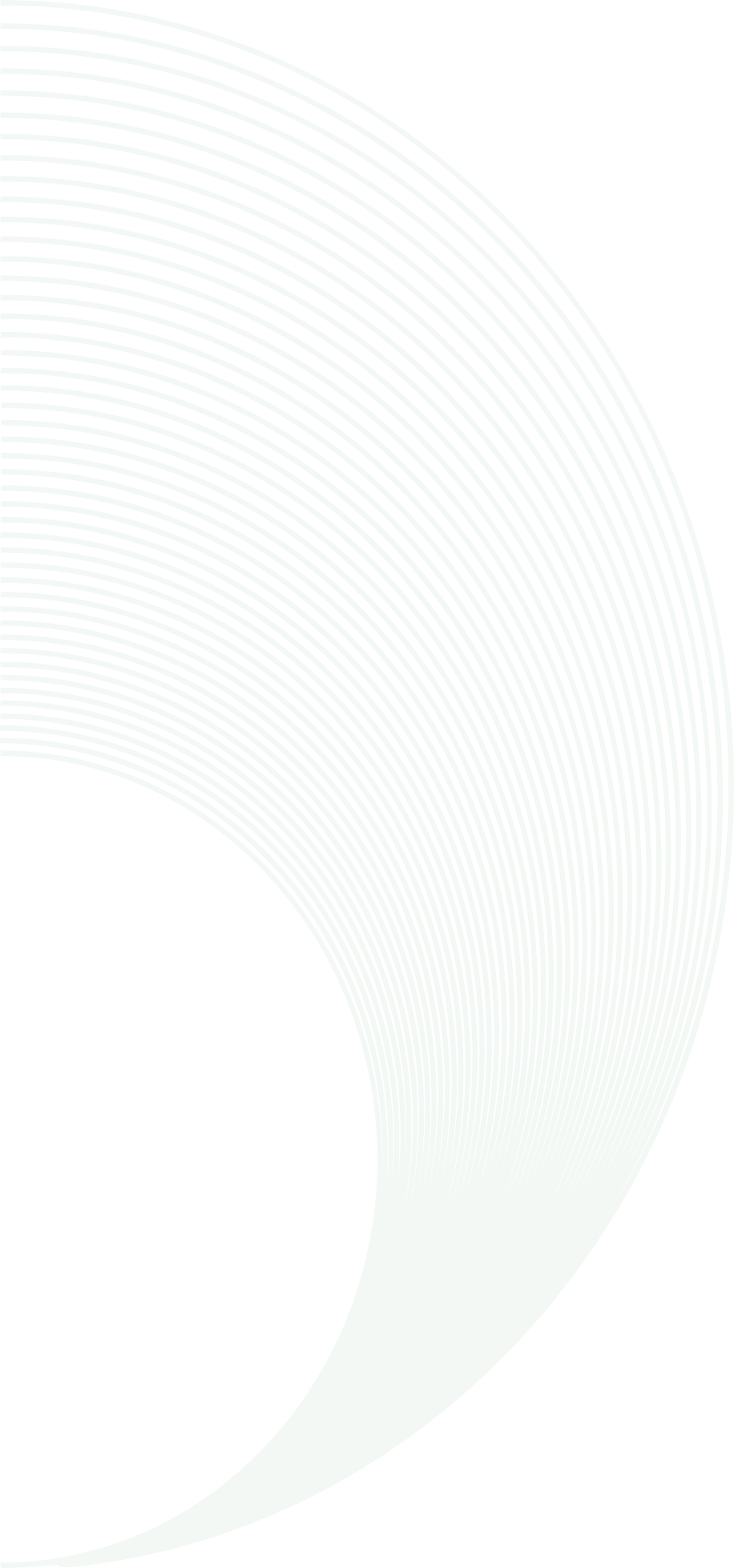
Vibration Monitoring Sensors: Key to Equipment Reliability and Performance
Vibration monitoring is an essential aspect of predictive maintenance in various industries. By continuously tracking vibrations in machinery, vibration monitoring sensors help detect potential issues before they lead to equipment failure. These sensors are widely used in industrial applications, such as manufacturing plants, power plants, and heavy machinery operations, to ensure smooth, efficient, and safe operations
What Are Vibration Monitoring Sensors?
Vibration monitoring sensors are devices used to measure and monitor vibrations in machines and equipment.
They capture mechanical vibrations caused by irregularities or imbalances in rotating parts, such as motors, pumps, fans, and compressors. These sensors are capable of measuring parameters like vibration amplitude, frequency, and velocity. The data collected helps identify abnormalities, such as misalignments, wear, or mechanical failure, that could affect the performance or lifespan of equipment.
The sensors typically consist of accelerometers or velocity sensors that detect vibrations and send real-time data to monitoring systems. With the advancements in sensor technology, many vibration monitoring sensors are now equipped with wireless capabilities, enabling remote monitoring and data collection for proactive maintenance management.
How Do Vibration Monitoring Sensors Work?
Vibration monitoring sensors work by detecting mechanical vibrations and converting them into electrical signals. These signals are then transmitted to a control system, where they are analyzed for any signs of abnormal vibration patterns. The most commonly used vibration sensors are accelerometers, which measure acceleration forces on a machine's components. Other sensors, such as velocity sensors or displacement sensors, can measure different aspects of vibration, such as the speed or the movement of components.
Once the vibrations are detected, the system compares them to preset thresholds or baseline vibration levels. If the vibration levels exceed safe limits, the system can trigger an alarm or send alerts to the maintenance team for immediate action. Early detection of unusual vibration patterns enables operators to address potential issues promptly, preventing costly repairs or unplanned downtime.
Key Features of Vibration Monitoring Sensors
Real-Time Monitoring
One of the key features of vibration monitoring sensors is real-time monitoring. These sensors continuously measure vibrations and provide immediate feedback, enabling operators to detect issues as they arise. Many modern sensors are equipped with wireless communication capabilities, allowing operators to receive data remotely, regardless of their location.
High Sensitivity and Accuracy
Vibration sensors are designed to capture even the smallest variations in vibrations, ensuring accurate readings. High sensitivity is particularly important when monitoring delicate equipment that may be prone to subtle but damaging vibrations. Accurate measurements ensure that any problems are detected early, allowing for timely interventions.
Ease of Installation
Vibration monitoring sensors are generally easy to install and integrate into existing machinery or systems. Many sensors are designed with a user-friendly setup process, and some models even come with mounting brackets or adhesive pads for quick attachment. This ease of installation minimizes the downtime during the deployment of monitoring systems.
Wide Range of Applications
Vibration monitoring sensors are used in a wide range of industries, from manufacturing and energy production to transportation and aerospace. They can be installed on various types of equipment, including electric motors, pumps, turbines, bearings, and fans. These sensors are versatile and suitable for both critical applications and less demanding equipment.
Data Logging and Analysis
Many vibration monitoring sensors come equipped with data logging capabilities. This allows for continuous tracking of vibration patterns over time, providing valuable insights into equipment performance and wear. Data logs can be analyzed to identify trends and patterns that may indicate developing issues, helping maintenance teams prioritize repairs and optimize schedules.
Benefits of Vibration Monitoring Sensors
Predictive Maintenance
Vibration monitoring sensors are a key component of predictive maintenance strategies. By continuously tracking vibrations, they enable maintenance teams to identify problems before they lead to equipment failure. Predictive maintenance minimizes the risk of unplanned downtime, reducing the need for emergency repairs and extending the lifespan of machinery. Early detection of issues like imbalance, misalignment, or bearing wear allows for more cost-effective interventions and helps prevent costly failures.
Improved Equipment Reliability
Consistent vibration monitoring leads to more reliable equipment. When operators can identify abnormal vibrations early, they can take corrective action before the issue escalates. This proactive approach improves the reliability of machines and equipment, reducing the risk of breakdowns and enhancing overall productivity.
Increased Operational Efficiency
The ability to detect issues before they cause failure helps optimize operations. Vibration monitoring sensors ensure that machinery is operating at peak efficiency, preventing performance degradation that can result from mechanical issues. By reducing unexpected maintenance events, businesses can maintain smoother operations, reduce downtime, and improve overall throughput.
Cost Savings
Regular vibration monitoring helps prevent major failures, which can be costly in terms of repairs, lost production, and safety incidents. By identifying minor issues before they become major problems, businesses can save significantly on repair costs and the cost of replacing equipment. Additionally, by improving operational efficiency, businesses can reduce energy consumption and minimize waste, further contributing to cost savings.
Enhanced Safety
Abnormal vibrations can be a sign of mechanical failure that poses safety risks to operators and other personnel. By detecting these issues early, vibration monitoring sensors contribute to a safer working environment. Identifying and addressing potential hazards before they cause accidents can help protect workers and prevent damage to equipment.
Applications of Vibration Monitoring Sensors
Manufacturing Industry
In manufacturing facilities, machinery such as motors, conveyors, and production lines rely on smooth operation for optimal performance. Vibration monitoring sensors are used to ensure that these machines are running efficiently and to detect early signs of malfunction, such as misalignments or imbalances.
Power Plants
Power plants rely on large, complex machinery like turbines and generators, which must operate smoothly to ensure the plant's efficiency and safety. Vibration monitoring sensors are essential for detecting any irregular vibrations that may signal potential problems, such as bearing failure or rotor imbalance. Early detection helps prevent costly repairs and power outages.
Aerospace and Aviation
In the aerospace industry, vibration monitoring is critical to ensuring the safety and reliability of aircraft engines and other mechanical systems. Vibration sensors help detect abnormalities that could affect flight safety, such as rotor imbalance or engine malfunction, allowing for timely maintenance interventions.
HVAC Systems
Heating, ventilation, and air conditioning (HVAC) systems use a variety of rotating components, such as fans and compressors, that can develop mechanical issues over time. Vibration monitoring sensors are installed in HVAC systems to monitor the health of these components and ensure the system operates efficiently.
Oil and Gas
In the oil and gas industry, vibration monitoring sensors are used to ensure the integrity of drilling rigs, pumps, and compressors. These sensors help detect irregularities in machinery that could indicate wear, misalignment, or potential failure, ensuring safe and efficient operations in this high-risk environment.
Conclusion
Vibration monitoring sensors are an essential tool for ensuring the reliability, safety, and efficiency of industrial equipment. By continuously tracking vibrations and providing real-time data, these sensors enable businesses to implement predictive maintenance strategies, reduce downtime, and improve equipment performance. Whether in manufacturing, power generation, or oil and gas operations, vibration monitoring sensors are crucial for preventing costly failures, enhancing safety, and maximizing operational efficiency.