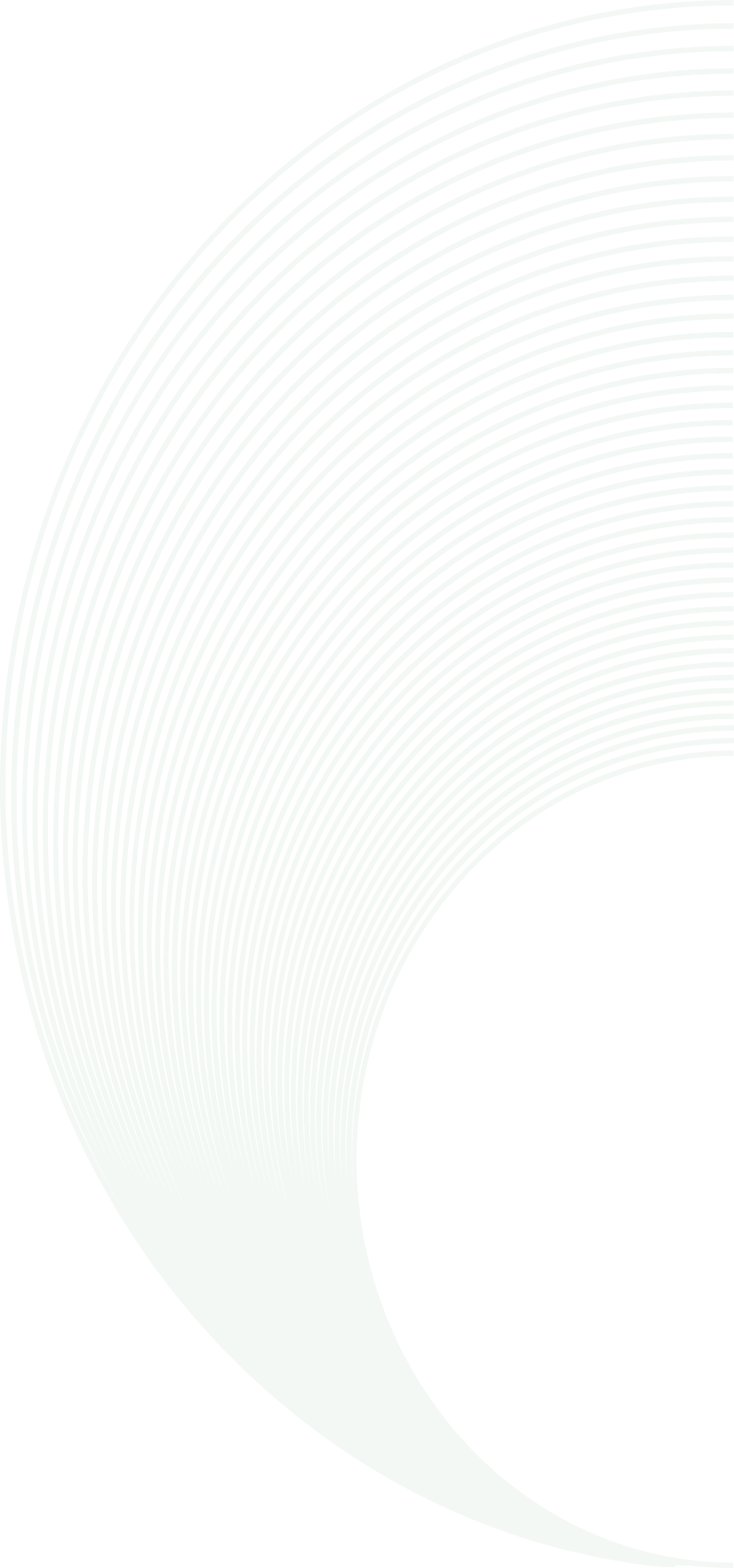
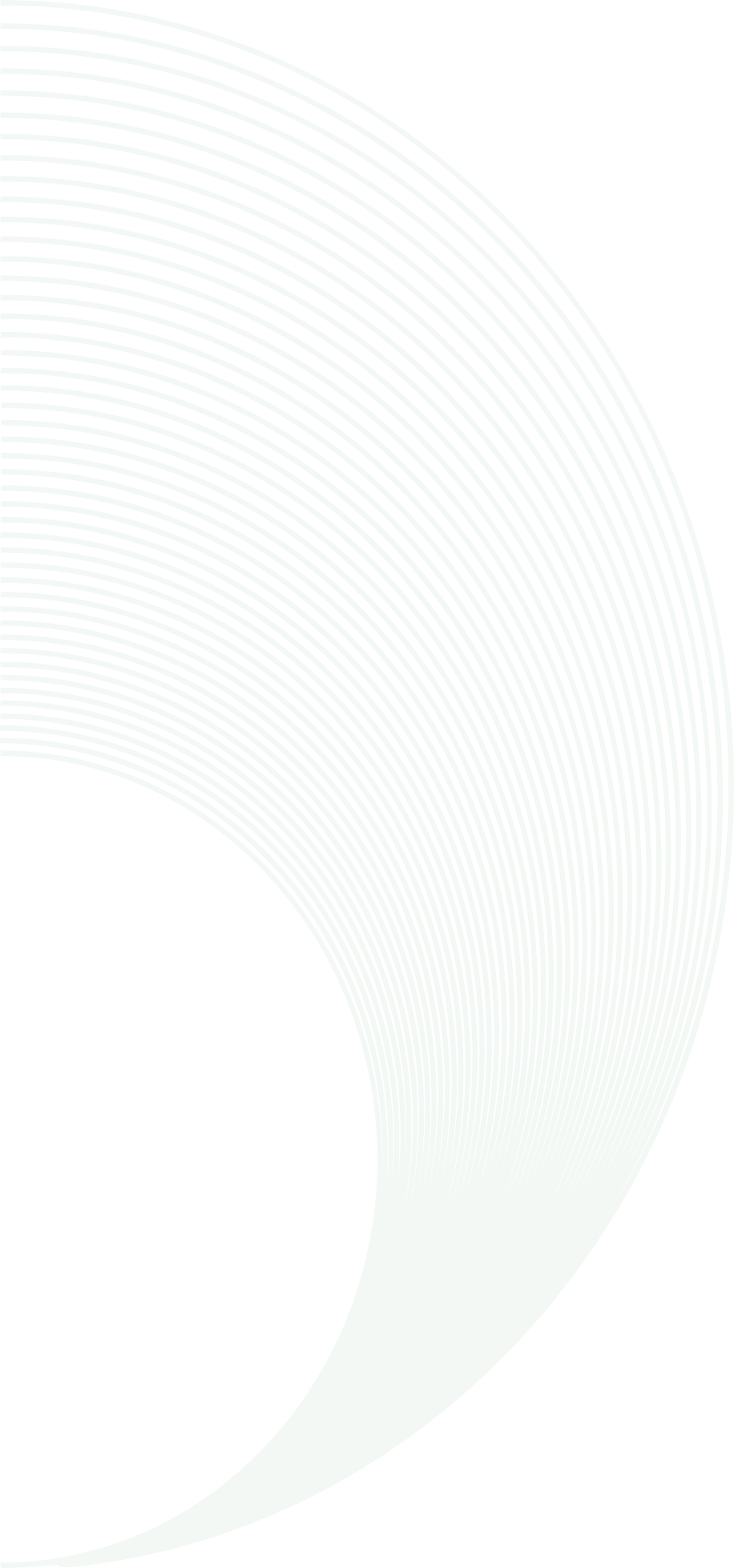
Work Order Maintenance Software: Streamlining Operations and Enhancing Efficiency
Work order maintenance software plays a vital role in improving the management of maintenance tasks in businesses, ranging from manufacturing plants to facilities management. It provides a centralized platform to handle work orders, track maintenance activities, and optimize resource allocation, resulting in increased efficiency and reduced downtime. By automating various aspects of maintenance operations, this software enables companies to keep their equipment, machinery, and facilities running smoothly while extending their lifespan.
What is Work Order Maintenance Software?
Work order maintenance software is a digital tool designed to help businesses manage maintenance requests, track the status of tasks, and ensure the efficient allocation of resources.
It allows managers and maintenance teams to create, assign, and monitor work orders for regular maintenance tasks or emergency repairs. The software can generate reports, maintain an inventory of spare parts, and send notifications or reminders to ensure that all work orders are completed on time and in accordance with company standards.
Benefits of Using Work Order Maintenance Software
Improved Efficiency:
Work order software centralizes all maintenance activities, making it easy for managers to assign tasks and track progress. This reduces the likelihood of missing deadlines or overlooking critical maintenance work, allowing teams to address issues proactively rather than reactively.
Reduced Downtime:
By enabling more efficient scheduling and tracking of maintenance work, companies can reduce unplanned downtime. Whether it’s routine inspections or urgent repairs, the software helps teams prioritize tasks, ensuring that the most important issues are addressed first, leading to less disruption in operations.
Cost Savings:
The software helps optimize resource allocation and manage inventory, preventing over-purchasing of parts or running out of necessary supplies. Additionally, by scheduling regular preventive maintenance, businesses can avoid costly repairs and extend the lifespan of equipment.
Data-Driven Insights:
Many work order maintenance software tools come with reporting and analytics features that allow managers to monitor performance metrics such as response times, task completion rates, and maintenance costs. This data can be used to identify areas for improvement, reduce inefficiencies, and make informed decisions about future maintenance strategies.
Improved Communication:
With work order software, communication between maintenance teams, managers, and other stakeholders is streamlined. All parties involved in a maintenance task can access real-time updates, which minimizes confusion and ensures that everyone is on the same page.
Better Compliance:
In industries where regulatory compliance is crucial, work order maintenance software helps track maintenance tasks and ensure that necessary inspections and repairs are performed as required. It also provides audit trails for compliance reporting.
Key Features of Work Order Maintenance Software
Work Order Creation and Assignment:
The software allows maintenance managers to create work orders for preventive or corrective tasks, assign them to technicians or teams, and set priorities and deadlines.
Mobile Access:
Many work order maintenance systems offer mobile access, enabling technicians to receive tasks, update statuses, and capture data from the field in real-time, improving the speed and accuracy of work orders.
Inventory Management:
Efficient inventory management is a critical part of maintenance operations. Work order software often includes tools for tracking parts, materials, and tools to ensure that maintenance teams have the resources they need when they need them.
Preventive Maintenance Scheduling:
A key feature is the ability to schedule recurring maintenance tasks, reducing the likelihood of equipment failure and extending the lifespan of assets. The software can automatically generate work orders for preventive maintenance based on preset schedules.
Reporting and Analytics:
The software can generate detailed reports on work order completion, downtime analysis, and asset performance. This data can be used to improve future planning, identify cost-saving opportunities, and refine overall maintenance strategies.
Asset Management:
Work order maintenance software often integrates with asset management tools, helping businesses keep track of equipment health, maintenance histories, and warranty statuses. This integration allows for better long-term planning and decision-making regarding asset replacement or upgrades.
Choosing the Right Work Order Maintenance Software
When selecting work order maintenance software, businesses should consider several factors to ensure that the software meets their specific needs.
Ease of Use:
The software should be user-friendly, requiring minimal training for both managers and technicians. A complicated system can hinder productivity and lead to frustrations.
Customization:
Look for a system that allows customization to meet your business’s unique needs. This might include tailoring workflows, setting custom reporting parameters, or integrating with existing systems like ERP or CRM platforms.
Scalability:
Ensure that the software can grow with your business. Whether you plan to expand your operations or need to accommodate more work orders, the software should be flexible enough to scale with your requirements.
Integration Capabilities:
The software should integrate with other tools and platforms you already use, such as asset management systems or enterprise resource planning (ERP) software. Seamless integration reduces data silos and helps streamline operations.
Mobile Compatibility:
As maintenance teams are often on the move, mobile access is critical. Ensure the software has a mobile app or mobile-optimized platform that allows field technicians to receive, update, and close work orders from their smartphones or tablets.
Cost and Support:
While it’s important to choose software that fits your budget, don’t sacrifice quality for cost. Consider the long-term value of the software and the support offered by the vendor, including training, technical support, and software updates.
Popular Work Order Maintenance Software Solutions
Fiix:
Fiix offers cloud-based work order maintenance software with features like preventive maintenance scheduling, work order management, and asset tracking. It’s highly customizable and integrates with other enterprise software systems, making it a great choice for businesses of all sizes.
UpKeep:
UpKeep is a user-friendly, mobile-first work order management platform designed to help businesses streamline their maintenance processes. It’s suitable for small to mid-sized businesses and offers real-time notifications, reporting, and asset management.
Hippo CMMS:
Hippo CMMS is another powerful work order management software solution that offers easy-to-use features for creating, managing, and tracking work orders. It includes tools for inventory management, preventive maintenance scheduling, and asset tracking.
Maintenance Connection:
Maintenance Connection is a comprehensive work order and asset management system that helps businesses optimize their maintenance operations. It offers mobile capabilities, real-time reporting, and integration with other business systems.
Conclusion
Work order maintenance software plays a critical role in improving the efficiency and productivity of businesses. By automating and streamlining maintenance processes, companies can reduce costs, improve asset lifespan, and prevent unplanned downtime. With the right software, businesses can effectively manage work orders, track maintenance tasks, and keep operations running smoothly. Whether you’re a small business or a large enterprise, choosing the right work order maintenance software is essential to maintaining a high level of operational efficiency.